The Ultimate Guide to CNC Turret Punch Presses0
In this Ultimate Guide to CNC Turret Punch Press, I’m excited to share my insights and expertise on this essential piece of equipment. Whether you're new to the world of CNC machining or seeking to enhance your current processes, this guide will equip you with comprehensive knowledge on best practices, optimization techniques, and programming strategies. From the fundamental principles of operation to tips for maximizing efficiency, I aim to provide a comprehensive understanding that will help you make informed decisions. Join me as we delve into the features, benefits, and best practices for using CNC turret punch presses effectively.
CNC turret punch is one of the main categories of CNC punch, the English name (CNC Turret Punch Press), abbreviation NCT. Numerical Control Turret Punch (NCT) integrates machine, electricity, liquid and gas. It is a pressure processing equipment for punching and shallow drawing and forming on the plate through the turret punch die.
Table of Contents
· Features
Features
Numerical Control Turret Punch (NCT) is composed of computer control system, mechanical or hydraulic power system, servo feeding mechanism, mold library, mold selection system, peripheral programming system, etc.
Numerical control turret punch (NCT) is a processing program compiled by programming software (or manual). The servo feeding mechanism sends the sheet to the position to be processed. At the same time, the mold selection system selects the corresponding mold in the mold library, and the hydraulic power system Press according to the program to automatically complete the processing of the workpiece.
Classification
Numerical control turret punch (NCT) is divided into full-electric servo CNC turret punch, mechanical CNC turret punch (flywheel CNC turret punch), and hydraulic CNC turret punch.
Among them, the full-electric servo CNC turret punch press is a brand-new type of turret punch. The device utilizes servo motor direct drive technology, thereby retaining the advantages of a simple, mature, and reliable mechanical main drive structure. At the same time, it has better characteristics than a hydraulic main drive. It possesses significant features and powerful functions. The device is equipped with a fully electric servo intelligent punch, capable of achieving various processes such as punching, forming, bending, and engraving.
Mechanical turret punch presses are widely utilized due to their long-term stability, longevity, and lower price compared to full-electric servo CNC turret punch presses; however, they lag significantly in efficiency and functionality.
Hydraulic turret punch presses have progressively fallen out of favor due to the requirement for consumable hydraulic oil and their unsuitability for high-temperature work environments.
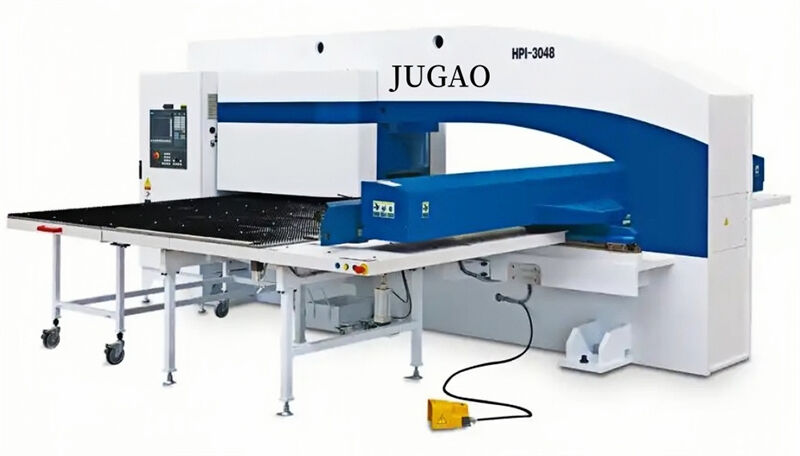
Motion axis
X axis: the servo drive axis that moves the workpiece along the direction perpendicular to the length of the bed
Y axis: Servo drive axis that moves the workpiece along the direction parallel to the length of the bed
A axis: Rotating turret-type tool magazine selects the rotation axis of the mold
C axis: the rotating axis for automatic mold indexing, which can rotate the mold at any angle
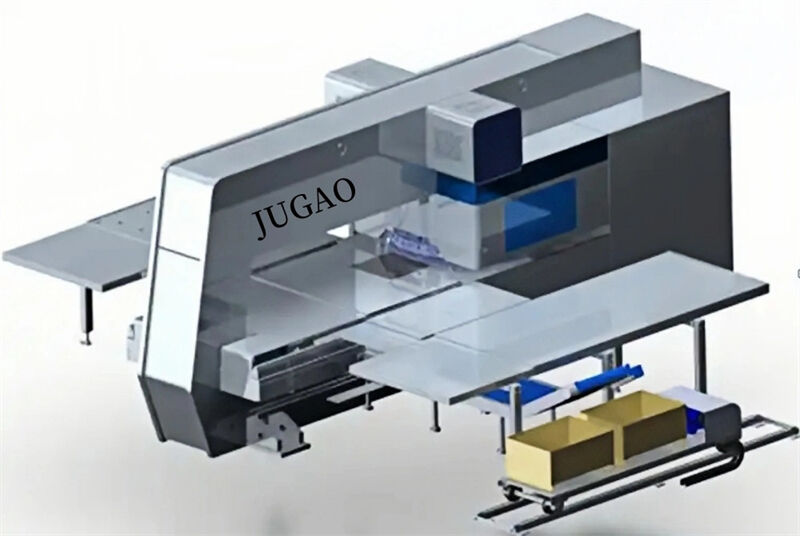
Processing methods
1. Single punching: complete punching in a single pass, including straight line distribution, arc distribution, circumferential distribution, and grid hole punching.
2. Continuous punching in the same direction: using rectangular molds to partially overlap the processing method, it is possible to process long holes and trim edges.
3. Multi-direction continuous punching: the processing method of using small molds to process large holes.
4. Nibble: Use a small round die to continuously punch the arc in a small step.
5. Single forming: the processing method of forming by shallow drawing at one time according to the mold shape.
6. Continuous forming: forming processing methods that are larger than the mold size, such as large-size shutters, rolling ribs, and rolling steps.
7. Array forming: processing multiple same or different workpiece processing methods on a large board.
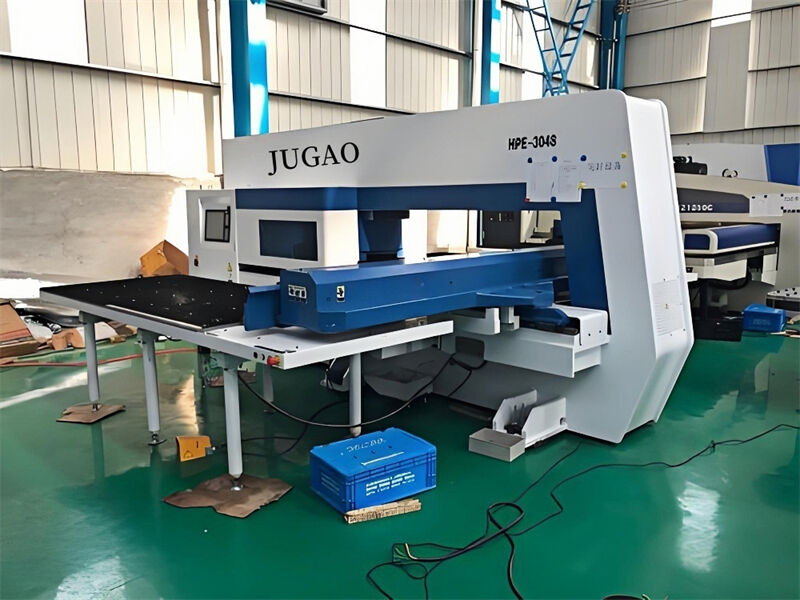
Processing station
Generally, turret die is classified according to the diameter of the holes it can process, which facilitates the selection of the die. They are typically divided into five grades: A, B, C, D, and E.
Grade A (1/2 inch) station: Processing range of Φ1.5 to Φ12.7 millimeters
Grade B (1-1/2 inch) station: Processing range less than Φ31.7 millimeters
Grade C (2 inch) station: Processing range less than Φ50.8 millimeters
Grade D (3-1/2 inch) station: Processing range less than Φ88.9 millimeters
Grade E (4-1/2 inch) station: Processing range less than Φ114.3 millimeters
Typically, when it is necessary to change the random configuration, the following conversions are followed: 1D = 8A = 4B = B + C.
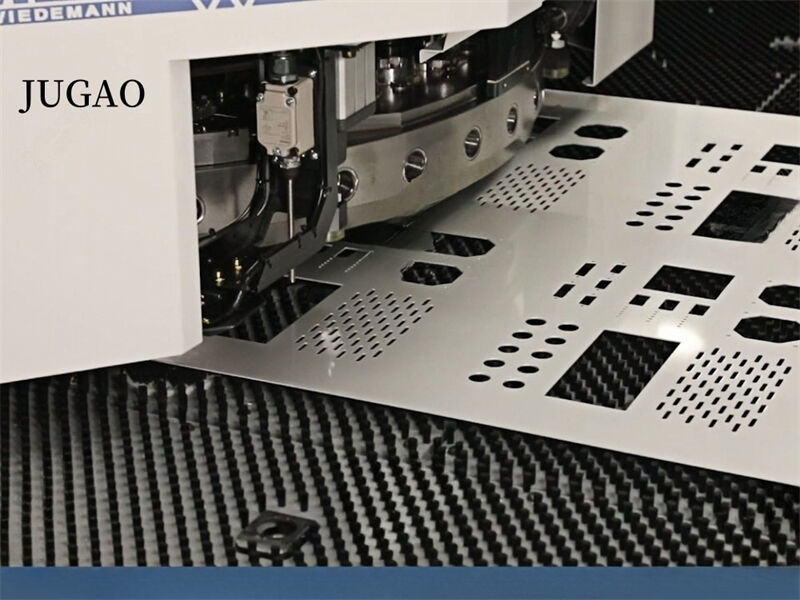
Application industry
Our products find widespread application in cold stamping processing industries, encompassing electric power equipment, chassis cabinets, curtain wall decorations, household appliances, the elevator industry, fire door manufacturing, air conditioners, kitchen appliances, office equipment, hardware furniture, medical machinery, and lighting fixtures, among others. The single punching method and the nibbling punching method are used to punch out holes and parts of various shapes and sizes, which is especially suitable for the punching of a variety of medium and small batches or single-piece plates.
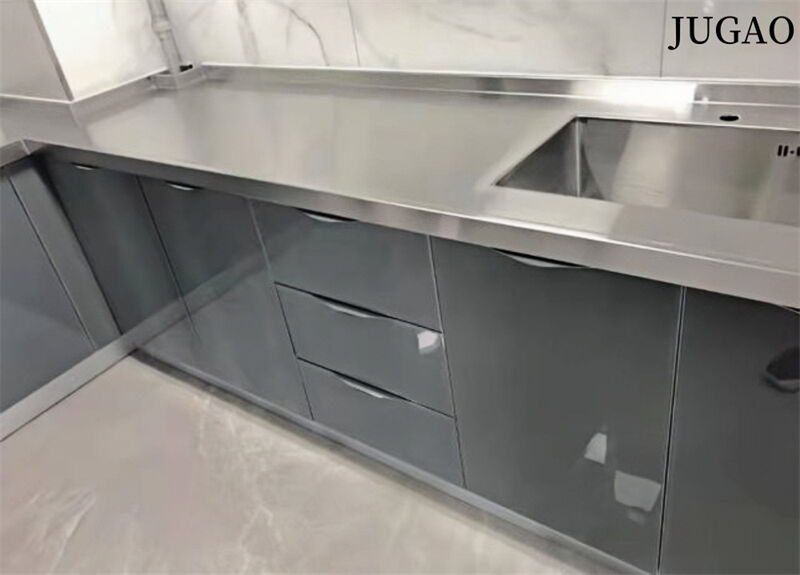
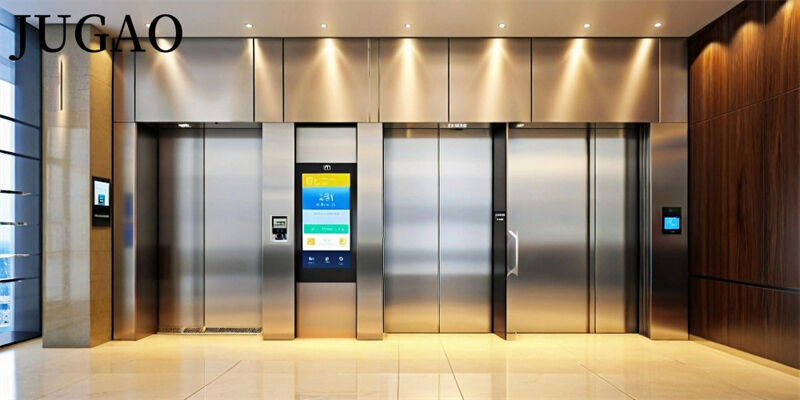
About Gary Olson
As a dedicated author and editor for JUGAO CNC, I specialize in delivering insightful and practical content tailored to the metalworking industry. With years of experience in technical writing, I focus on providing in-depth articles and tutorials that help manufacturers, engineers, and professionals stay informed about the latest innovations in sheet metal processing, including CNC press brakes, hydraulic presses, shearing machines, and more.