Distinguishing Characteristics of 3-Roller Plate Rolling and 4-Roller Plate Rolling
Throughout my tenure working with plate rolling machines, I have frequently encountered discussions regarding the comparison between 3-Roller Plate Rolling Machines and 4-Roller Plate Rolling Machines. Each variant presents distinct advantages and is tailored for various applications within the realm of metal fabrication. It is imperative to grasp the distinctions between a 3-roller and a 4-roller plate rolling machine to ensure the selection of appropriate equipment for specific projects. Over time, I have acquired a comprehensive understanding of their operational principles, efficiency metrics, and the quality of bends they yield. In this discourse, I shall delineate these differences, thereby aiding in the making of well-informed decisions for your plate rolling requirements.
A plate rolling machine is a type of forging machinery and equipment that bends non-metallic plates into conical, spherical, cylindrical, or other geometric shapes. This machinery is extensively utilized in the manufacturing of goods, boilers, steam systems, chemical industries, non-metallic structures, and mechanical engineering, among other sectors. The diversity of coiling machines is due to their varied applications across different fields.
Plate rolling machines are categorized based on the number of rollers, which leads to the classification into 3-roller and 4-roller types. A common misconception is that the primary difference between the two is merely the additional roller in the four-roller machine. Consequently, some individuals, when making a purchase, erroneously believe that the four-roller machine is superior due to the extra roller. However, this perspective is flawed, as the two machines possess significant differences.
Distinguishing Characteristics of 3-Roller and 4-Roller Plate Rolling Machines
Structural Aesthetics
The three-roller rolling machine is equipped with three rollers, while the four-roller rolling machine features four. Beyond this fundamental distinction, the three-roller machine presents a more straightforward and utilitarian aesthetic. Conversely, the four-roller machine, incorporating hydraulic CNC technology, boasts a more refined and elegant appearance. The attention to detail in its design not only enhances processing precision but also contributes to an improved user experience.
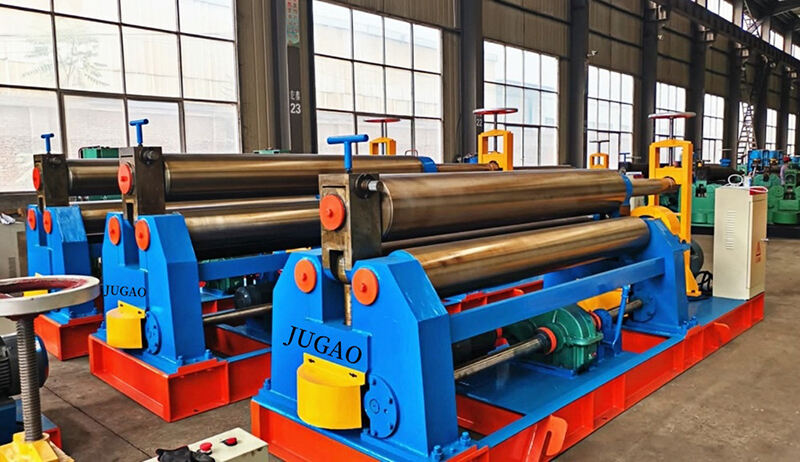
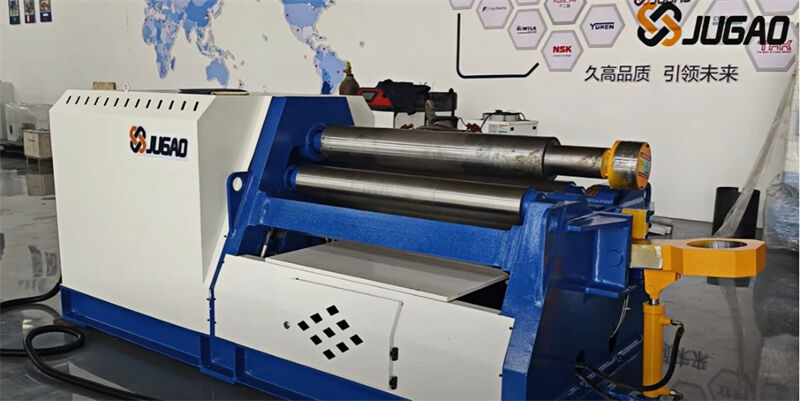
Machine Structure
The mechanical three-roller coiling machine is categorized into two types: the three-roller symmetrical coiling machine and the three-roller asymmetrical coiling machine. In the three-roller symmetrical coiling machine, one roller is positioned above, while the remaining two rollers are symmetrically aligned below. Conversely, the three-roller asymmetrical coiling machine features an asymmetric arrangement where one side consists of two rollers, with the other side having a single roller.
The distinction from the four-roller plate rolling machine lies in its main drive mechanism, which is connected to the upper rollers via a reducer and cross-slider coupling to provide torque for the rolled plate. The lower rollers are designed for vertical movement and are connected through a reducer worm gear (or bevel gear) to facilitate the clamping of the plate, thus enabling mechanical transmission. Additionally, side rollers are situated on both sides of the lower rollers and are capable of inclined movement along the rack rail, driven by a filament worm gear (or bevel gear). The four-roller plate rolling machine features two rollers at the top and two at the bottom, with all four work rollers equipped with dynamic bearings.
However, the variance in the number of rollers results in distinct step mechanisms between the three-roller and four-roller rolling machines.
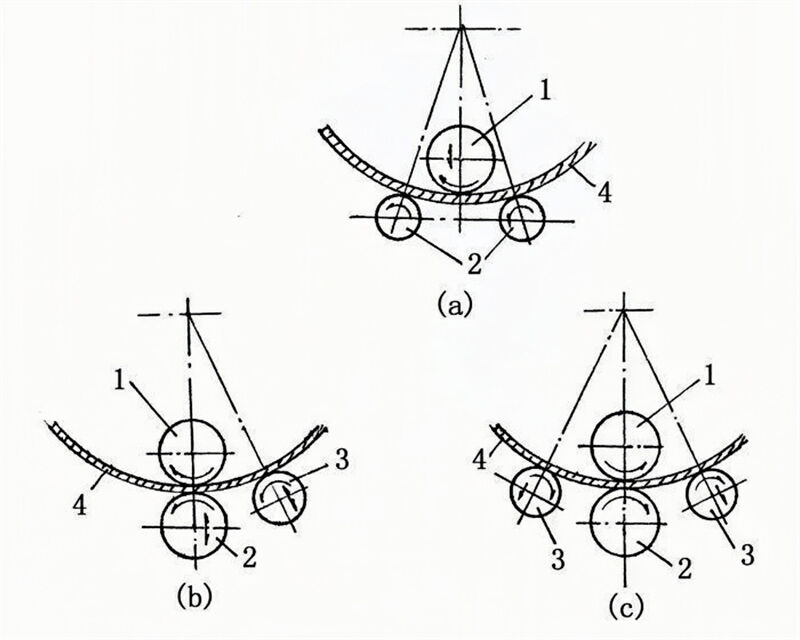
Type of Processing
The three-roll plate rolling machine is capable of producing cylindrical and curved metal plates. Its operation involves the vertical movement of the two lower rollers, which are centrally and symmetrically positioned. This vertical movement is achieved through a screw rod and a worm drive mechanism. The rotation of the lower rollers is powered by a motor, and torque is transmitted to the rolled plate via the meshing of the output gear of the gearbox with the lower roller gear. The ends of the plates require pre-bending, which can be facilitated by additional equipment.
The four-roll plate rolling machine is designed for the bending and shaping of metal plates. It is capable of producing cylindrical, curved, and conical components within a specified dimensional range. This machine also features a pre-bending function for the ends of the plates, resulting in minimal residual straight edges, and it can approximately level the metal plates.
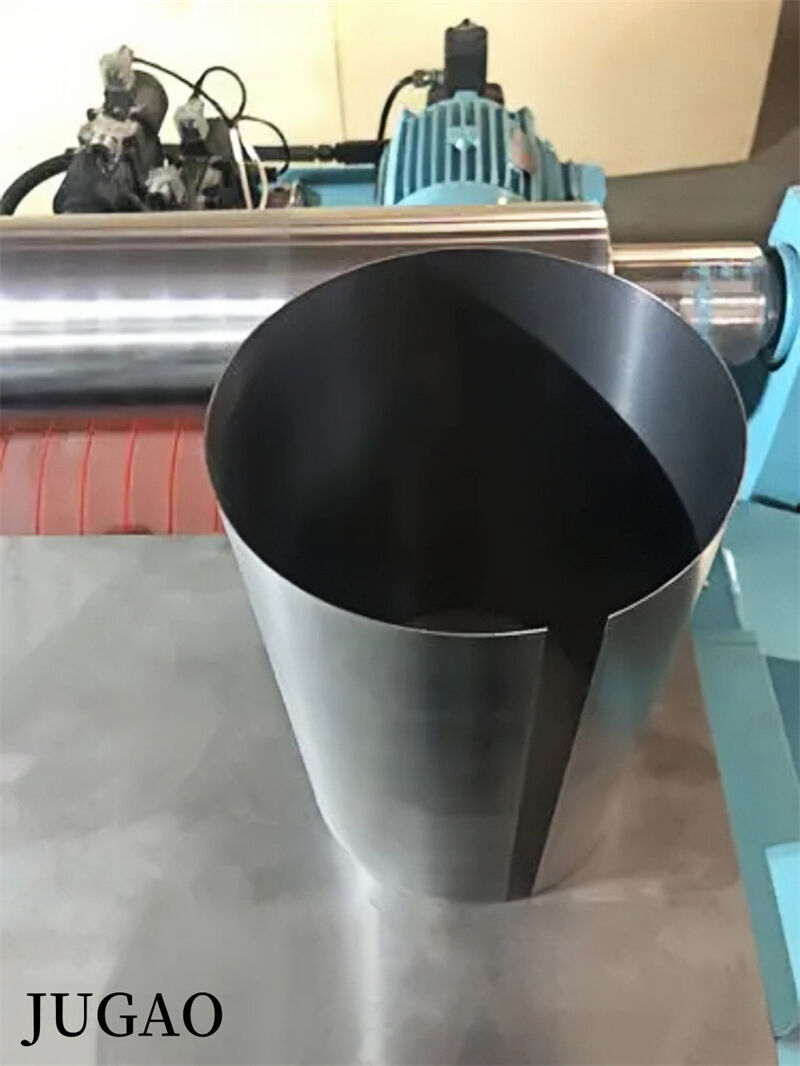
Degree of Automation
The three-roller rolling machine features a button-based control system, while the four-roller rolling machine is equipped with a touchscreen interface and a CNC system that allows for programmable operations. Digital control facilitates one roll forming process, with touchscreen capabilities for visual input, work step editing, and storage of up to 500 data sets. An electronic balancing system, integrated with EPS, ensures that roll movement remains parallel within a tolerance of 0.15 mm. The system supports human-machine interaction, self-diagnostic fault detection, and intelligent identification of operational errors. The drum-shaped rollers exhibit excellent roundness and high straightness. All movements are hydraulically driven.
The rollers are designed to move in straight lines within guide rails, allowing for a reduced center distance between the two sides of the rollers to achieve precise rolling accuracy. The robust frame, which is thick and capable of accommodating medium to large-sized rollers, is annealed as a single unit to eliminate stress and prevent deformation. The rollers are manufactured as a single piece, subjected to a hardening process, and are compatible with both manual and automatic operational modes.
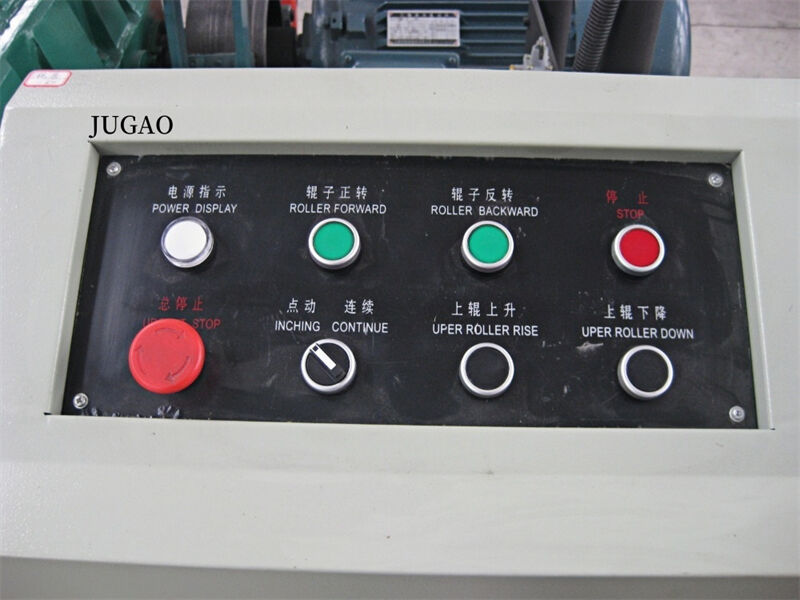
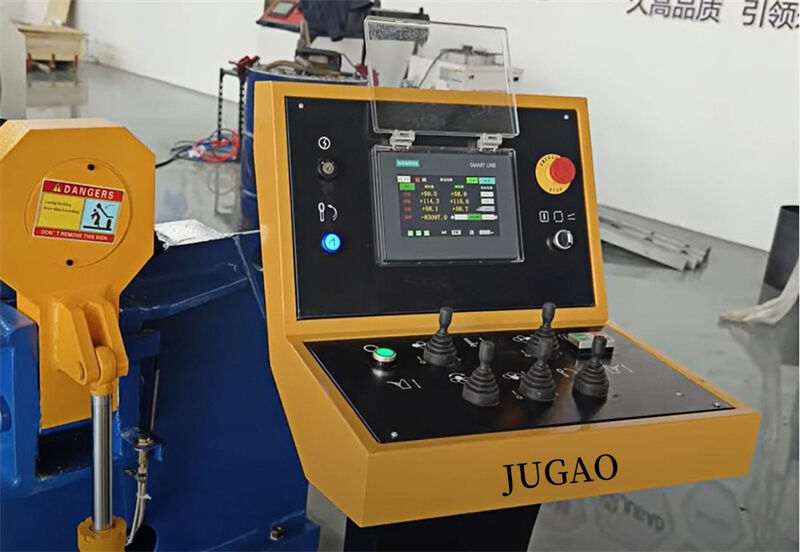
Method of Unloading
The three rollers necessitate manual Uninstall, mandating the manual Uninstall of the machined workpiece. In contrast, the four rollers are equipped with push buttons for control, facilitating an easy and expedient Uninstall process, which is notably swifter than that of the three rollers.
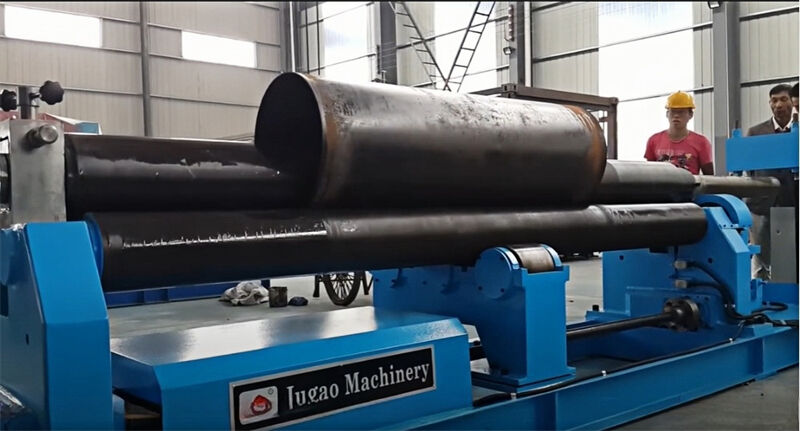
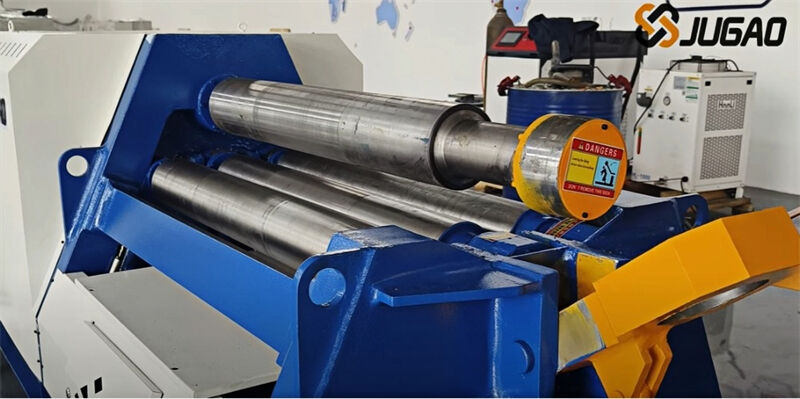
Roll Movement Form
The three-roller asymmetric plate rolling machine features an upper roller that serves as the primary drive mechanism. The lower roller is capable of vertical movement to secure the plate, and it engages with the upper roller gear to facilitate the main drive function. The side roller is designed for tilting and lifting actions, providing both pre-bending and rounding capabilities. In contrast, the three-roller symmetrical plate rolling machine positions the upper rollers symmetrically above the two lower rollers, which execute vertical lifting movements through screw and master worm drive mechanisms. The two lower rollers are responsible for rotational movement, driven by the output gear of the reducer engaging with the lower roller gear to generate the necessary torque for plate rolling.
Both types operate on the principle of the three-point fixed circle, which accommodates rolling systems with varying radii. Nevertheless, the four-roller plate rolling machine offers superior capabilities in pre-bending straight edges and achieving a more precise calibration of the circular profile compared to its three-roller counterpart.
Power Mode
The majority of three-roller rolling machines are mechanical in nature; however, hydraulic rolling machines also exist. It is noteworthy that all four-roller rolling machines are of the hydraulic type. The mechanical three-roller symmetrical plate rolling machine features a structural design where the upper roller is positioned symmetrically between the two lower rollers. This upper roller executes vertical lifting movements via bevel gear transmission, driven by the main reducer's single-stage gear. The two lower rollers engage in rotational movement through gear mesh, powered by the main reducer, to provide the necessary torque for plate rolling.
Flat metal plates are processed through the three working rollers—two lower rollers and one upper roller—where the upper roller exerts downward pressure and the lower rollers rotate. This action subjects the metal plate to multiple continuous bends, resulting in permanent plastic deformation and forming the plate into the desired cylindrical, conical, or other specified shapes. A drawback of the mechanical three-roller plate rolling machine is that the plate's edges require pre-bending with additional equipment.
The hydraulic three-roller symmetrical plate rolling machine also adopts a three-roller symmetrical structure. In this design, the upper roller is situated symmetrically between the two lower rollers and is capable of vertical lifting movements through the action of hydraulic oil within the hydraulic cylinder. The two lower rollers are driven to rotate via the main reducer's final gear, thereby providing torque for the rolling process.
Flat metal plates are processed through the three working rollers—two lower rollers and one upper roller—where the upper roller exerts downward pressure and the lower rollers rotate. This action subjects the metal plate to multiple continuous bends, resulting in permanent plastic deformation and forming the plate into the desired cylindrical, conical, or other specified shapes. A drawback of the hydraulic three-roller symmetrical rolling machine is that the plate's edges require pre-bending with additional equipment. This type of machine is particularly suitable for rolling plates with thicknesses exceeding 50 mm. The design of the large plate rolling machine includes an additional row of fixed rollers on the two lower rollers, which shortens the span distance between them. This modification enhances the accuracy of the rolled workpiece and the overall performance of the machine.
The four-roller plate rolling machine is a hydraulic type, where the upper roller serves as the primary drive. It provides torque to the plate through the output gear of the reducer meshing with the upper roller gear. The lower roller is capable of vertical lifting movements, driven by hydraulic oil acting on the piston within the hydraulic cylinder, for clamping the plate. Additionally, the side rollers on both sides of the lower roller are designed for tilting movements along the rack rail, transmitted through a filament master worm gear. The machine's advantage lies in its ability to perform plate end pre-bending and rounding on the same apparatus.
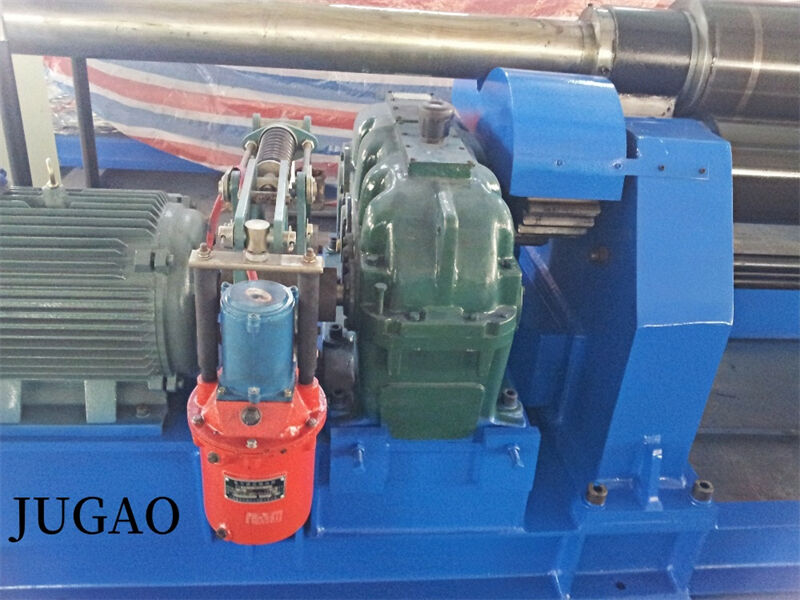
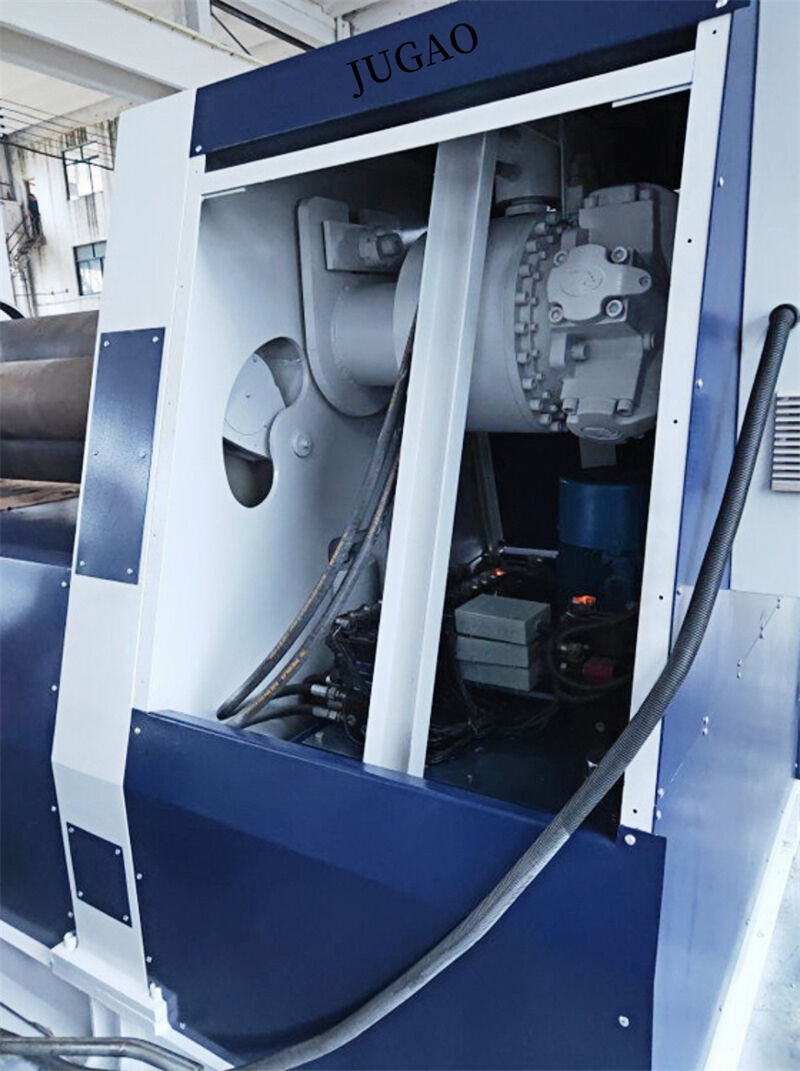
Work Efficiency
The efficiency of three-roller plate rolling machines is often lower due to the mechanical nature of the equipment and the necessity for manual intervention in various processes, which consequently diminishes overall productivity. In contrast, four-roller rolling machines, equipped with hydraulic systems and CNC (Computer Numerical Control) technology, exhibit significantly higher motor processing efficiency and, by extension, superior overall work efficiency. The output rate of workpieces from four-roller machines is also markedly greater than that of their three-roller counterparts.
Processing Precision
The processing precision of the three-roller scrolling machine is generally satisfactory and capable of fulfilling the fundamental requirements of the majority of manufacturing facilities; the processing precision of the four-roller scrolling machine is superior, enabling the production of cones and other specialized shapes of workpieces.
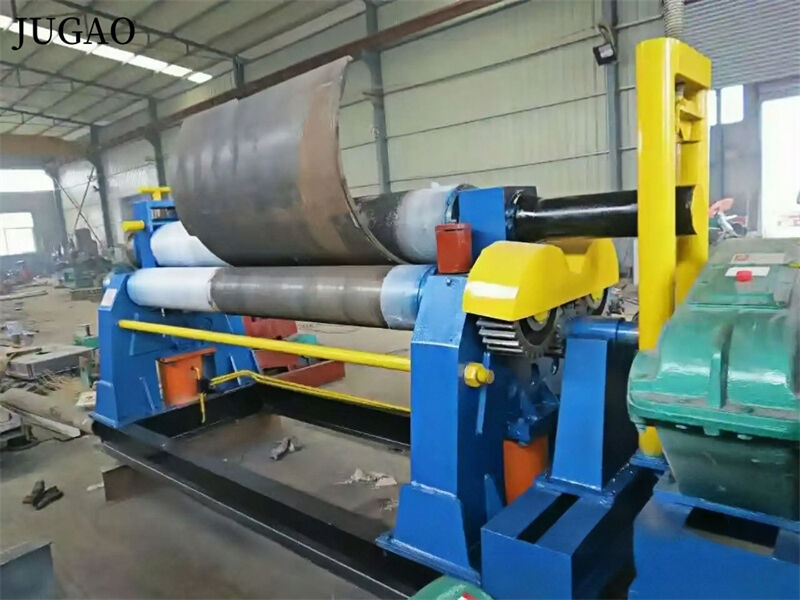
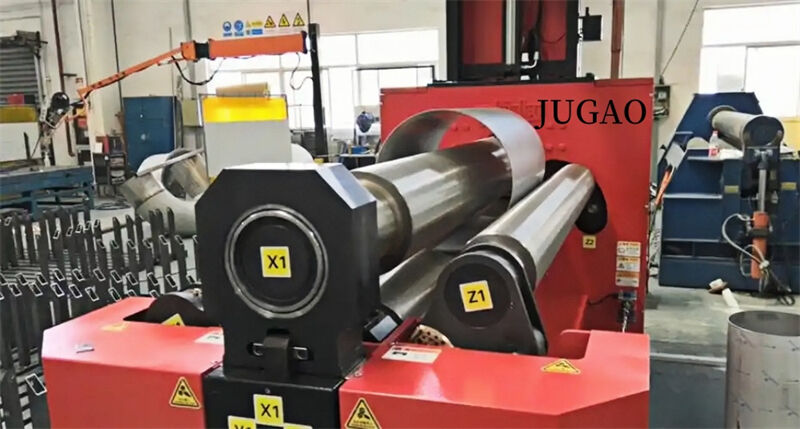
Price Comparison
When comparing models, it is evident that the cost of a three-roller rolling machine is typically less than that of a four-roller rolling machine. This discrepancy arises from the fact that the precision and efficiency of a three-roller rolling machine are generally inferior to those of a four-roller rolling machine. Should the frequency of machine utilization be relatively low and the precision demands on the workpiece not stringent, opting for the more affordable three-roller rolling machine may be advisable. Conversely, if the product specifications necessitate a higher standard of precision, the four-roller rolling machine, despite its higher cost, presents a more economically advantageous choice.
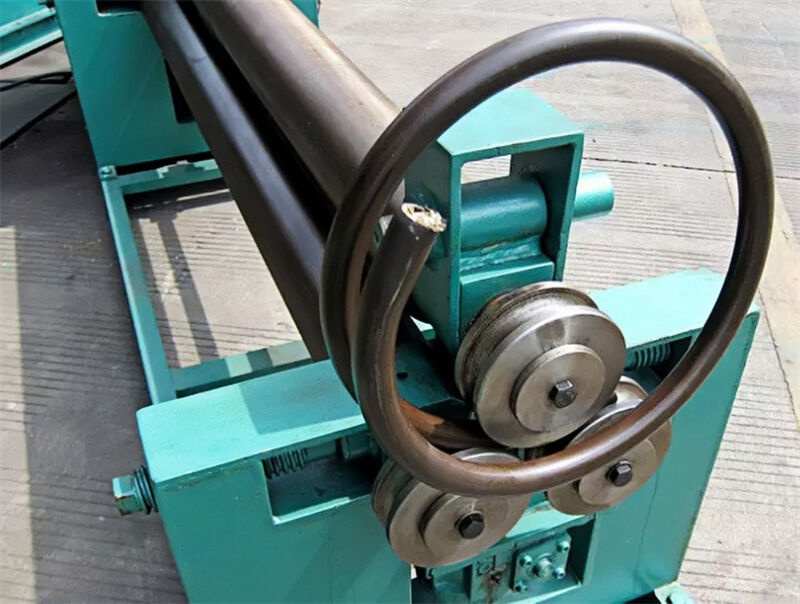
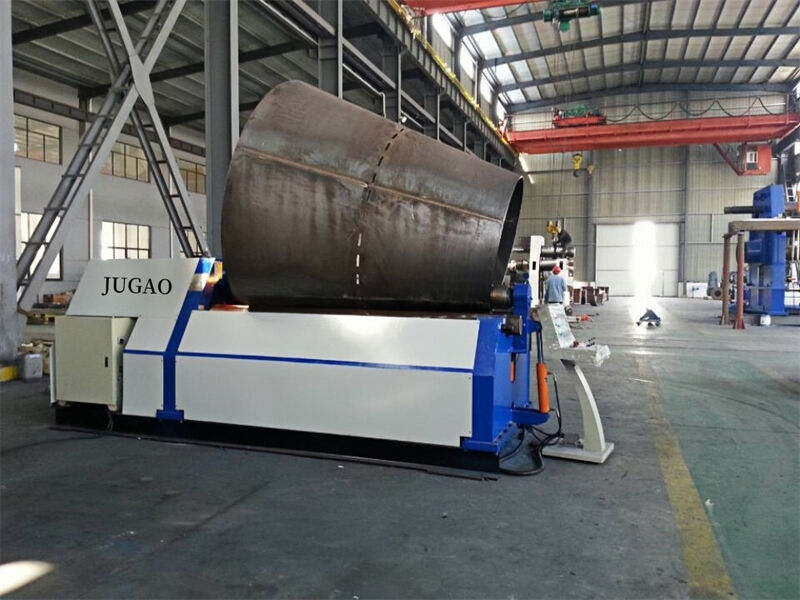
Rolling machines are available in a variety of models, each with a distinct structural composition and performance capabilities. Prospective purchasers of rolling machines should endeavor to comprehend the disparities among these models. It is imperative to avoid any misconceptions during the purchasing process. Failure to do so may result in acquiring a machine that fails to satisfy one's operational requirements, thereby hindering its optimal utilization and potentially introducing numerous complications into one's workflow.
About Gary Olson
As a dedicated author and editor for JUGAO CNC, I specialize in delivering insightful and practical content tailored to the metalworking industry. With years of experience in technical writing, I focus on providing in-depth articles and tutorials that help manufacturers, engineers, and professionals stay informed about the latest innovations in sheet metal processing, including CNC press brakes, hydraulic presses, shearing machines, and more.