How can bending machines become the core engine of industrial automation upgrades?
Table of Contents
1. CNC technology: a new benchmark for reshaping bending accuracy
· The battle of millimeters: precision optimization solutions for automation systems
· Complex geometric bending: industrial practice of intelligent calibration
· Adaptive control: an efficiency revolution from debugging to production
2. Full process automation: a manufacturing transition of speed and collaboration
· Human-machine collaboration: deep integration of robotic arms and bending units
· Multi-process bending: the path to achieving offline programming and unmanned factories
· Zero-error logistics: precise linkage between AGV and vision systems
3. Flexible manufacturing: a breakthrough for small-batch customization
· Multi-material compatibility: a breakthrough in processing from carbon fiber to special alloys
· Modular molds: a practical case of rapid mold change in 3 minutes
· Cloud Smart manufacturing: cost reduction and efficiency improvement driven by design library sharing
4. Full life cycle management: operation and maintenance strategy of automated equipment
· Preventive maintenance: golden rule for efficient operation of equipment
· Hydraulic system: scientific solution for oil management and wear control
· Precision transmission: maintenance guide for guide rails and ball screws
5. Smart manufacturing upgrade: in-depth analysis of high-frequency problems
· Old equipment transformation: technical feasibility of automation upgrade
Industry 4.0 docking: protocol selection and practice of data interconnection
· Safety line: multiple protection system of automated equipment
Introduction: Smart bending opens a new era of manufacturing
As the core equipment in the field of metal forming, the bending machine is reconstructing the industrial automation landscape through intelligent upgrades. This article deeply analyzes how CNC technology, robot integration and flexible manufacturing enable bending processes, and provides a panoramic solution for the manufacturing industry from efficiency improvement to cost optimization.
How CNC Bending Machine Technology Revolutionizes Precision
Optimizing Bending Accuracy in Automated Systems
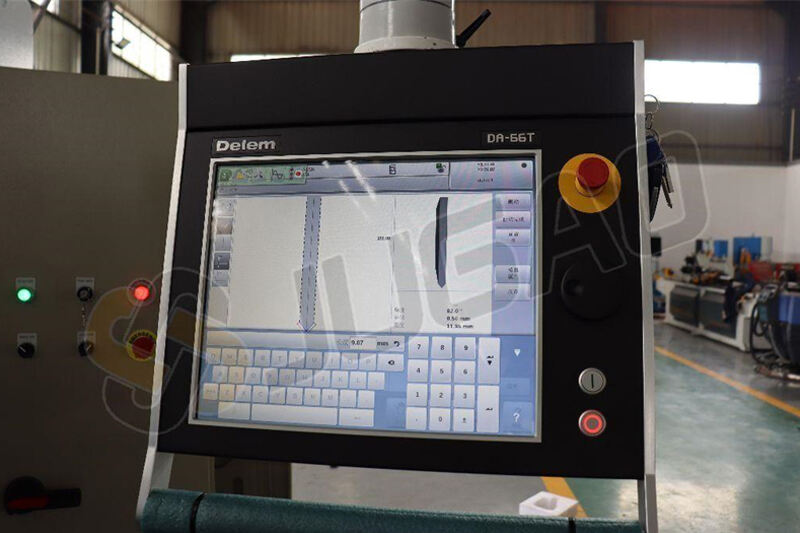
Modern industrial automation equipment relies on CNC (Computer Numerical Control) systems to achieve ultra-high-precision bending. Operators can pre-program parameters such as bending angle, depth, and speed to ensure consistency in mass production. For instance, JUGAO CNC bending machines utilize real-time feedback sensors to adjust slide positioning accuracy to ±0.0004 inches, significantly reducing material waste caused by deviations.
Angle Calibration for Complex Parts
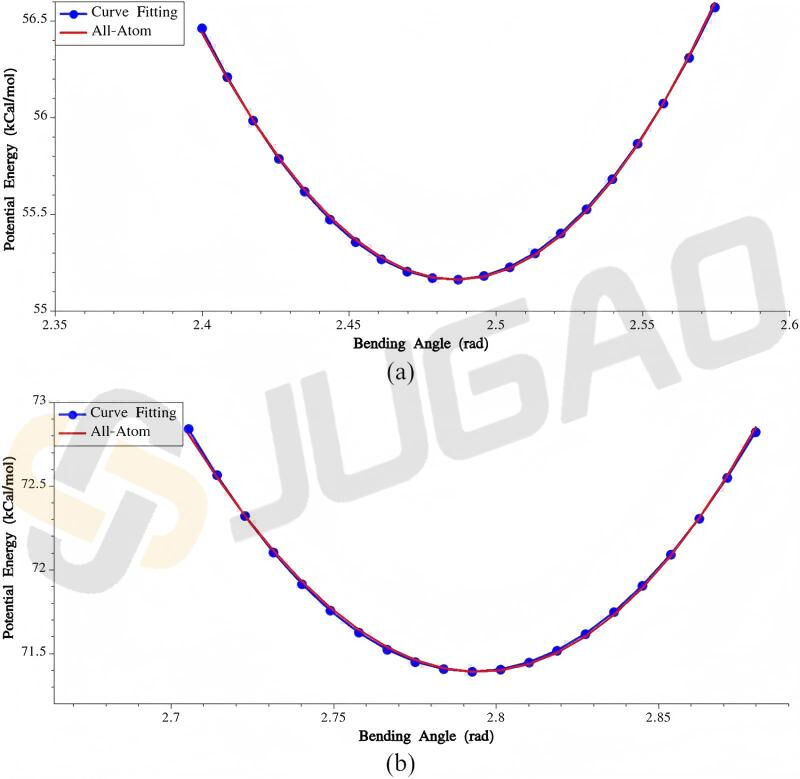
To handle intricate designs, operators input CAD-based blueprints into the CNC system. The system automatically calculates die positions and compensates for material springback, ensuring each bend adheres to strict specifications. This capability is critical for industries like aerospace, where part tolerances often fall below 0.1 mm.
Adaptive Control Systems Reduce Setup Time
Advanced bending machines are equipped with adaptive die systems that automatically adjust clamping pressure and die alignment based on material thickness. This eliminates manual trial-and-error adjustments, cutting setup time by 70% and accelerating delivery cycles for custom orders.
Enhancing Production Speed Through Automation
Integration of Bending Machines with Robotic Loaders
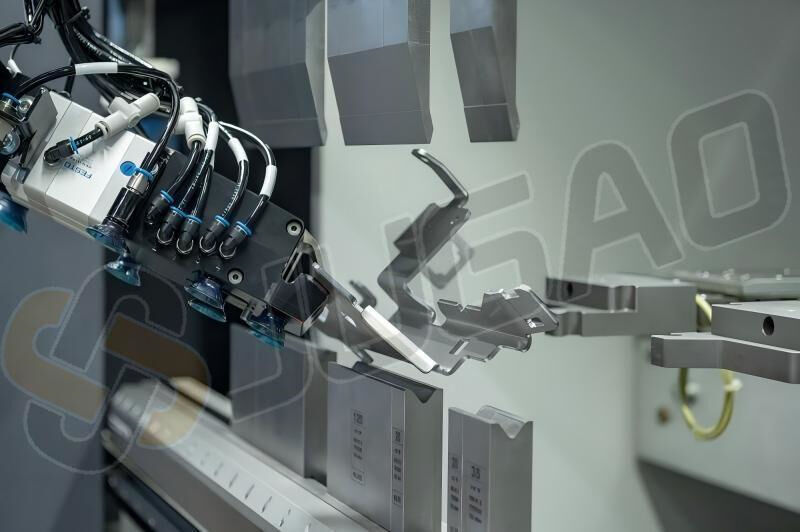
Combining bending machines with robotic arms creates fully automated bending cells. Robots handle raw sheet loading, reposition parts between bends, and unload finished products. For example, JUGAO bending machines synchronize with 6-axis robots to achieve dual-precision bending control, processing over 240 bends per hour—tripling efficiency compared to manual operations while reducing labor costs and enabling one-operator, multi-machine production lines.
Robot Path Programming for Multi-Stage Bending
Offline simulation software allows operators to plan collision-free robot motion paths, minimizing downtime. Once validated, programs are transferred to robot controllers, enabling unmanned operations for high-volume production.
Minimizing Material Handling Errors
Automated Guided Vehicles (AGVs) transport raw materials to bending units, while vision systems verify part orientation before bending. Such integration reduces human intervention, lowering error rates by over 90% in industries like automotive manufacturing.
Maximizing Flexibility in Customized Production
Adapting to Mixed-Material Workflows
Modern bending machines process diverse materials, including stainless steel and carbon fiber composites. Hydraulic models adjust tonnage settings to prevent brittle alloy cracking, while servo-electric machines balance efficiency and energy savings in aluminum forming.
Rapid Die Changeover for Small-Batch Orders
Quick-change die systems complete mold swaps in under 3 minutes. For instance, JUGAO bending machines employ standardized rapid clamping units compatible with multi-V dies, radius dies, and hemming tools. Rationalized segmentation of upper and lower dies allows multi-position, multi-size bending, simplifying non-standard part processing.
Leveraging Cloud-Based Design Libraries
IoT-enabled bending machines connect to cloud platforms, enabling manufacturers to access pre-validated bending programs for common parts. This feature allows small-scale producers to replicate high-precision designs without costly R&D investments.
Maintenance of Bending Machines in Industrial Automation
Routine Inspections for Sustained Performance
Regular maintenance is critical to ensure optimal machine operation. Key tasks include:
· Hydraulic Oil Quality Checks
Contaminated oil accelerates pump and valve wear. Replace hydraulic oil every 1,000 hours and use filtration systems to remove metal particles.
· Lubrication of Guides and Ball Screws
Apply high-viscosity grease to linear guides weekly to prevent misalignment from friction. For CNC bending machines, recalibrate ball screws every 500 hours to maintain positioning accuracy.
Frequently Asked Questions
Can Legacy Bending Machines Be Upgraded to Automation?
Yes! JUGAO CNC Retrofit Kits add CNC systems, servo pump controls, electro-hydraulic proportional valves, servo backgauges, ball screw linear guides, and robot interfaces to older models, extending service life by up to 15 years.
How Do Bending Machines Integrate with Industry 4.0 Systems?
Modern machines support OPC-UA or MTConnect protocols, enabling real-time data sharing with Enterprise Resource Planning (ERP) platforms for predictive maintenance alerts and production analytics.
What Safety Features Are Essential for Automated Bending Machines?
Prioritize models with laser guards, safety light curtains, and emergency stop relays. JUGAO bending machines feature dual-hand controls and pressure-sensitive floor mats to ensure operator safety.
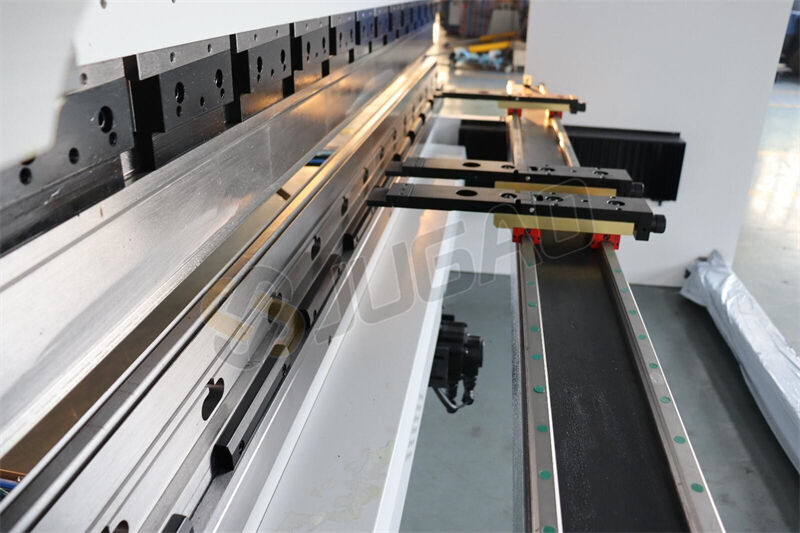
Bending machines in industrial automation are driving manufacturing advancements through precision, speed, and flexibility. From CNC-driven accuracy to robotic integration, these machines empower factories to reduce operational costs while meeting evolving demands. Ready to upgrade your production line? Explore the JUGAO Fully Automated Bending Machine Series or consult our engineering team for tailored solutions. Let’s shape the future of manufacturing together!