Revolutionizing Aerospace Manufacturing: The Transformative Impact of Advanced Press Brake Technology
The aerospace industry operates at the pinnacle of engineering precision, where micron-level accuracy can determine mission success. Modern press brake technology has emerged as a cornerstone in this demanding sector, enabling manufacturers to transform specialized alloys into the complex structural components that define contemporary aircraft design. This in-depth analysis explores how cutting-edge press brake solutions are addressing the unique challenges of aerospace manufacturing while setting new benchmarks for quality and efficiency.

Precision Engineering for Aerospace Excellence
Fabricating Mission-Critical Aircraft Components
Aerospace applications demand unparalleled precision in metal forming operations. Today's CNC press brake systems deliver:
Structural airframe components with exacting dimensional tolerances
Precision-formed control surface assemblies
Engine compartment shielding elements
Landing gear structural elements
These advanced systems utilize real-time angle measurement and adaptive correction technologies to maintain tolerances within ±0.1°, ensuring perfect compatibility with adjacent aircraft systems.
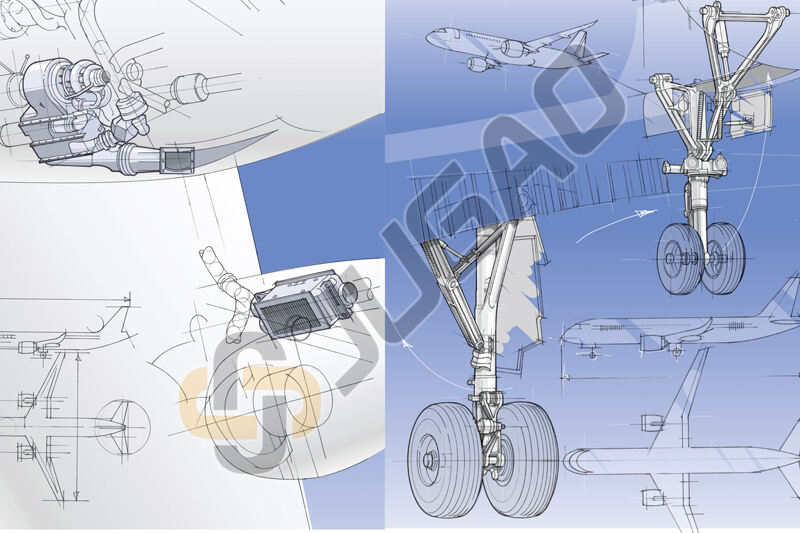
Advanced Material Processing Capabilities
Modern press brake technology has evolved to handle aerospace-grade materials with exceptional finesse:
Titanium Alloys: Specialized tooling configurations prevent stress cracking
Aluminum Composites: Adaptive bending sequences accommodate material memory
High-Strength Steels: Precision-controlled hydraulic systems manage extreme material resistance
This material versatility enables manufacturers to optimize component weight without compromising structural integrity - a critical factor in aerospace design.
Streamlining High-Stakes Production Workflows
Contemporary press brake systems provide significant advantages in aerospace manufacturing environments:
Automated tool changing reduces setup time by up to 70%
Integrated vision systems verify component geometry in-process
Cloud-connected monitoring enables predictive maintenance scheduling
Digital twin technology facilitates rapid process optimization
These capabilities prove particularly valuable when producing complex wing and fuselage components where traditional fabrication methods would be prohibitively time-consuming.
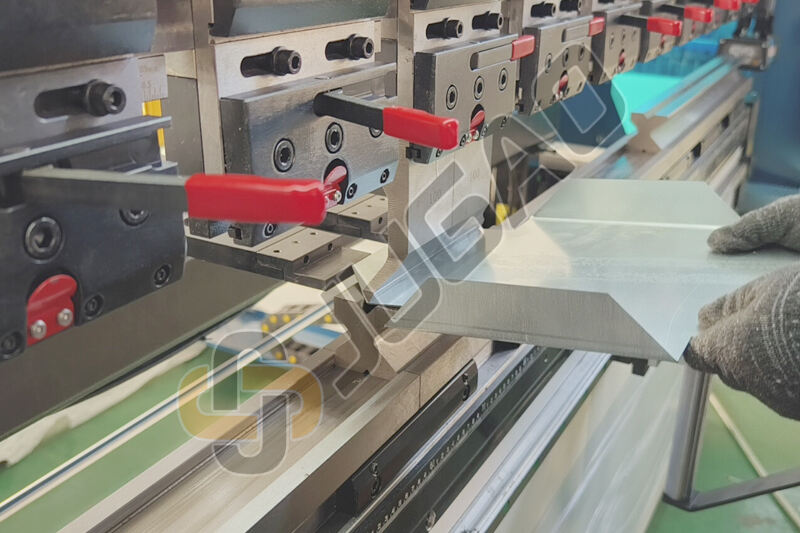
Optimizing Press Brake Operations for Aerospace Standards
Strategic Machine Configuration Protocols
Establishing optimal press brake performance requires meticulous attention to setup procedures:
1. Workspace Preparation
-Vibration-dampened foundation installation
-Climate-controlled environment maintenance
Ergonomic operator positioning considerations
2. Precision Tooling Configuration
-Material-specific die selection protocols
-Laser-verified tool alignment procedures
-Dynamic pressure distribution optimization
3. Calibration Excellence
-Multi-axis backgauge certification
-Real-time angle monitoring implementation
-Automated compensation for thermal expansion
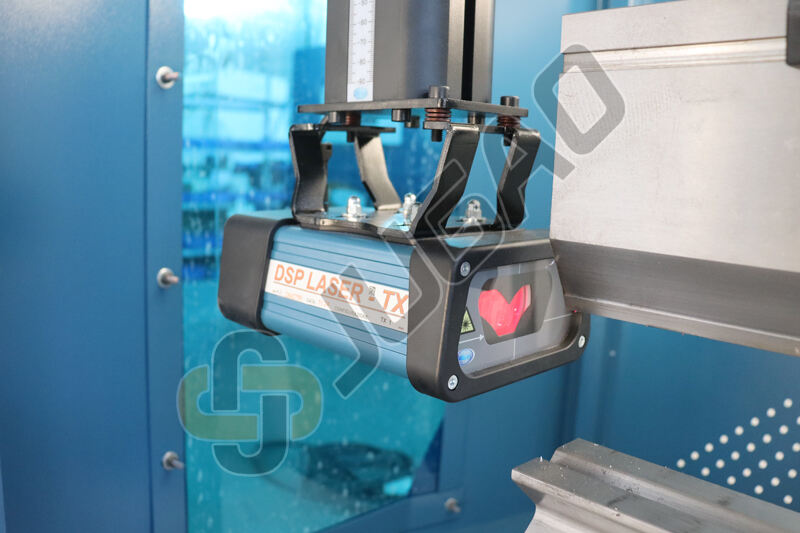
Comprehensive Maintenance for Peak Performance
Aerospace-grade maintenance protocols include:
Preventive Maintenance Schedule
-250-hour intermediate inspections
-500-hour comprehensive service intervals
-1000-hour full system recalibration
Advanced Diagnostic Procedures
-Hydraulic fluid spectrometry analysis
-Servo motor performance benchmarking
-Structural fatigue testing
Continuous Improvement Practices
-Software version control management
-Retrofit opportunity evaluation
-Operator skill enhancement programs
Expert Solutions for Aerospace Manufacturing Challenges
Q: What quality assurance measures ensure press brake precision in aerospace applications?
A: Implement a layered approach combining laser interferometer calibration, in-process CMM verification, and statistical process control methodologies.
Q: How does modern press brake technology address titanium's unique forming challenges?
A: Advanced systems utilize heated tooling options, strain-rate controlled bending sequences, and post-forming stress relief protocols to maintain material properties.
Q: What maintenance frequency is recommended for high-volume aerospace production?
A: Intensive operations require 200-hour inspection cycles with particular attention to hydraulic system integrity and guideway wear patterns.
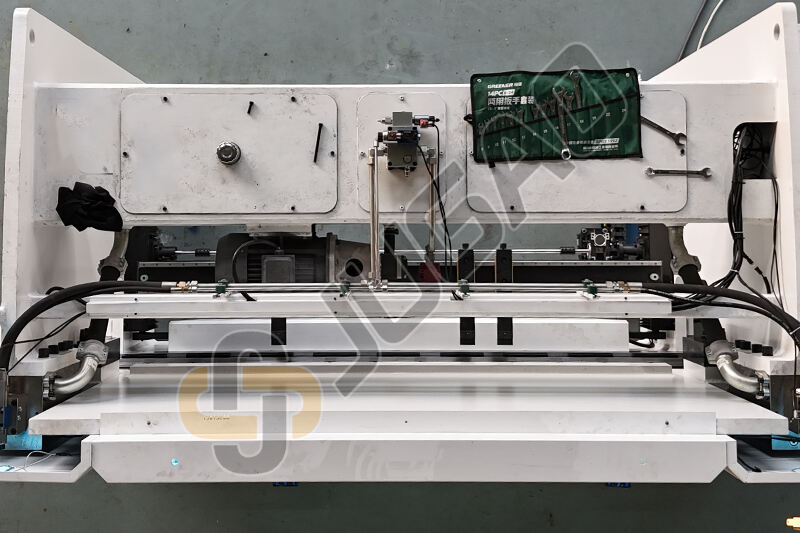
Pushing the Boundaries of Aerospace Fabrication
The aerospace industry's relentless pursuit of performance excellence continues to drive press brake innovation. Emerging technologies such as:
AI-powered adaptive forming algorithms
Hybrid additive/subtractive manufacturing integration
Nanocomposite-compatible tooling systems
are positioning press brake technology as a key enabler for next-generation aircraft development. For manufacturers ready to elevate their aerospace fabrication capabilities, partnering with technology leaders who understand the unique demands of this sector can provide the competitive edge needed in today's market.
Leading equipment providers now offer comprehensive aerospace solutions packages, including:
Material-specific process development services
Regulatory compliance documentation support
Turnkey training and certification programs
By embracing these advanced capabilities, aerospace manufacturers can achieve unprecedented levels of precision, efficiency, and innovation in their metal forming operations.