The Core Role of Sheet Metal Bending Equipment in Automotive Manufacturing
Table of Contents
Core Functions of Press Brakes in the Automotive Industry
Precision Forming Process for Structural Components
Artistic Processing of Body Panels
Performance Optimization Solutions for Automotive-Specific Press Brakes
Breakthroughs in Intelligent CNC Systems
Long-Term Equipment Maintenance Strategies
Solutions to Common Bending Challenges in Automotive Manufacturing
Material Springback Control Technology
Tooling Selection and Defect Prevention
High-Efficiency Solutions for Mass Production
FAQ: Bending Processes in Automotive Manufacturing
Conclusion
For professionals in automotive manufacturing, precision machining and efficient production are the lifelines of high-quality vehicle manufacturing. As a core equipment in metal forming, sheet metal bending machines play a pivotal role in automotive component production. This article delves into their specific applications, process optimization strategies, and best practices to enhance production line efficiency.
Core Functions of Press Brakes in the Automotive Industry
Precision Forming Process for Structural Components
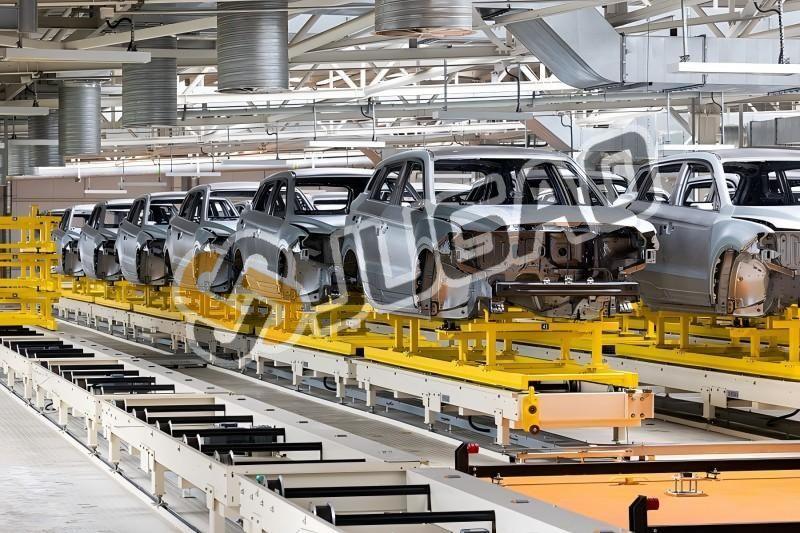
Press brakes are indispensable in manufacturing critical structural parts such as chassis reinforcements, bracket assemblies, and frame systems. These safety-critical components demand strict dimensional tolerances. Equipped with CNC control systems, modern press brakes achieve machining accuracy of ±0.1mm, even for complex 3D bends.
Mass Production Consistency Assurance Technology
In modern automotive assembly lines, consistency across tens of thousands of components is non-negotiable. Intelligent press brakes store hundreds of bending programs, ensuring millimeter-level repeatability across batches. This stability reduces scrap rates by over 30% and accelerates production cycles.
Artistic Processing of Body Panels
Beyond structural parts, press brakes shape aesthetic components like door assemblies, hoods, and fenders. These parts require not only dimensional precision but also surface smoothness exceeding Ra 0.8μm to meet automotive design standards.
Breakthroughs in Lightweight Material Processing
To address the industry’s shift toward aluminum, magnesium alloys, and advanced high-strength steel (AHSS), press brakes now feature specialized tooling systems and adaptive pressure control. These innovations prevent cracking and warping during high-strength material forming.
Performance Optimization Solutions for Automotive-Specific Press Brakes
Breakthroughs in Intelligent CNC Systems
Modern CNC systems integrate automatic angle compensation, intelligent back gauge positioning, and tooling library management. Real-time bending force monitoring and collision prevention reduce setup time by 50% and boost first-pass yield to 98%+.
Laser-Assisted Forming Systems
Industry leaders employ laser-guided bending with dynamic angle compensation. This technology is critical for complex 3D parts like exhaust system pipes and suspension arms.
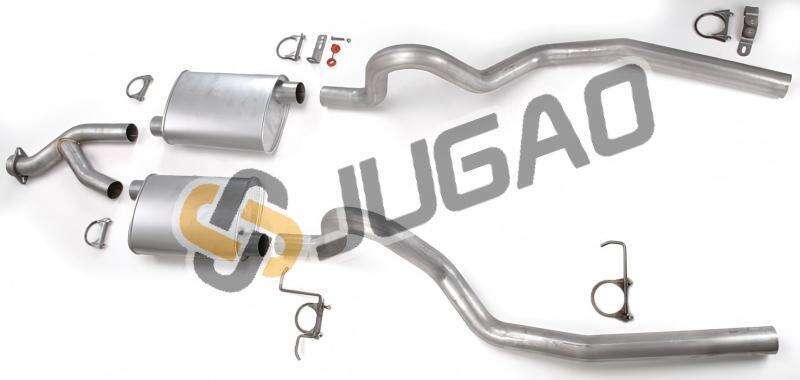
Long-Term Equipment Maintenance Strategies
In 24/7 automotive plants, equipment reliability directly impacts Overall Equipment Effectiveness (OEE). Scientific maintenance extends Mean Time Between Failures (MTBF) by 40%+.
Tiered Maintenance Protocols
Daily Maintenance:
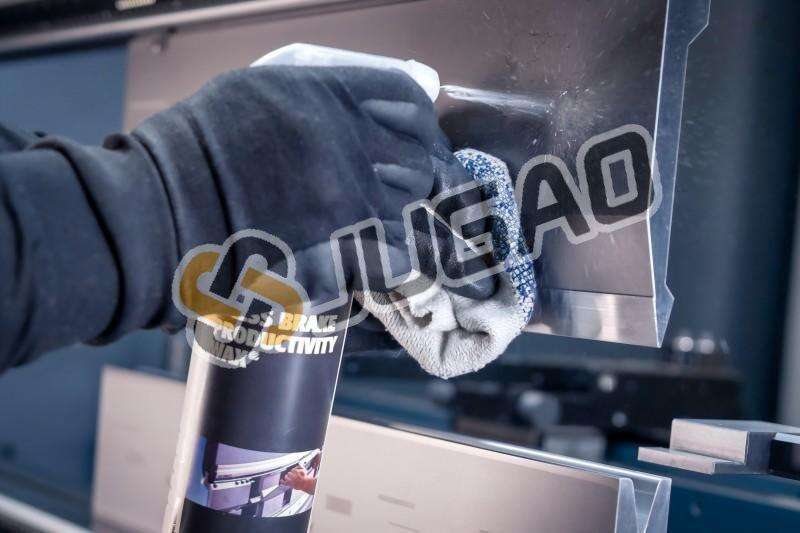
Check hydraulic oil levels (maintain H46 anti-wear hydraulic oil at 2/3 of the sight glass).
Clean tooling surfaces (apply specialized anti-rust coatings).
Verify positioning accuracy (using laser interferometers).
Weekly Maintenance:
Lubricate guide rails (use lithium-based grease).
Test safety light curtains (response time ≤0.1s).
Validate CNC programs (via CMM comparison).
Solutions to Common Bending Challenges in Automotive Manufacturing
Material Springback Control Technology
Compensation databases are built for different materials:
6061 Aluminum: 0.5°–1.2° overbend.
DP980 High-Strength Steel: 1.8°–2.5° overbend.
Finite element analysis (FEA) predicts deformation, with compensation values preset in CNC systems.
Tooling Selection and Defect Prevention
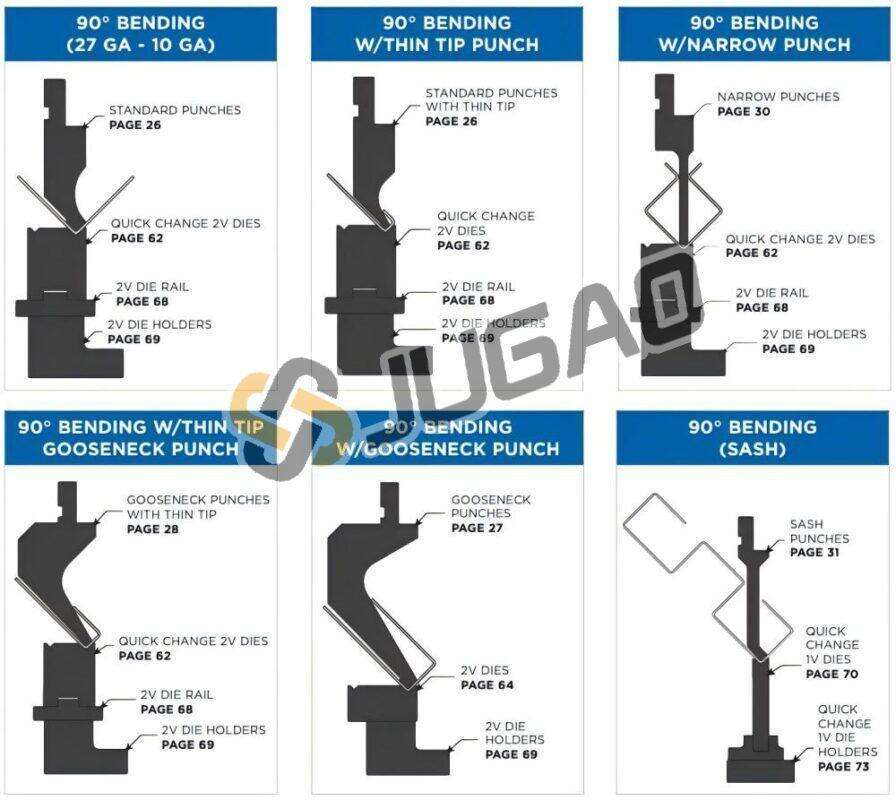
A material-thickness-tooling matrix ensures optimal results:
1.5mm CR Steel: V=12mm die.
2mm Aluminum: R=2T punch radius.
Multi-stage tooling for AHSS eliminates bend marks.
High-Efficiency Solutions for Mass Production
Quick-change tooling systems (<3-minute setup), RFID tool management, and MES integration enable unmanned production. One OEM achieved 85% equipment utilization post-implementation.
FAQ: Bending Processes in Automotive Manufacturing
How do CNC press brakes improve automotive manufacturing efficiency?
With automatic tool changers and programming software (compatible with AutoForm data), changeovers take 30 seconds. A door frame reinforcement production rate increased from 120 to 200 units/hour.
What advanced materials are used in automotive bending?
Beyond DC04 cold-rolled steel, common materials include:
HC420/780DP Dual-Phase Steel (780MPa yield strength).
6000-Series Aluminum (18% elongation).
AZ31B Magnesium Alloy (requires preheating to 200°C).
What is the tooling replacement cycle for mass production?
Implement a tool life management system:
Standard steel tools: Re-grind every 100,000 cycles.
Carbide tools: Lifetime exceeds 5 million cycles.
Vibration monitoring alerts for critical tooling fatigue.
How to process ultra-thin sheets (<0.6mm)?
Use precision servo-electric press brakes (±0.01mm accuracy) with polyurethane tools (90 Shore A hardness). One EV manufacturer achieved 0.4mm battery casing production using vacuum worktables.
Conclusion
Sheet metal bending equipment remains the backbone of automotive manufacturing, driving advancements in lightweight and electric vehicle trends. Through innovations like industrial IoT remote monitoring and hot-forming-assisted bending, these machines continue to evolve. For automotive-specific bending solutions or process optimization consulting, contact our engineering team. Explore our technical resource library for the latest Automotive Sheet Metal Processing Whitepaper.