Optimizing Bending Processes for Superior Quality in Metal Fabrication
Optimizing Bending Processes for Superior Quality in Metal Fabrication
Table of Contents
1. The Critical Role of Bending Process Optimization
Why Bending Optimization Matters
Key Factors Influencing Bending Quality
2. A Step-by-Step Guide to Optimizing Bending Operations
Selecting the Right Equipment
Precision Tooling Configuration
Material Readiness and Handling
Calibration and Quality Assurance
3. Troubleshooting Common Bending Challenges
Recognizing Frequent Bending Defects
Proactive Solutions for Consistent Results
4. Expert Answers to Press Brake FAQs
Best Practices for Press Brake Calibration
Maintenance Frequency for Peak Performance
5. Final Thoughts on Achieving Flawless Bends
In the competitive field of metal fabrication, optimizing bending processes is the cornerstone of delivering high-precision, defect-free products. Whether you operate a small workshop or a large-scale production facility, refining your bending techniques can dramatically improve efficiency, reduce waste, and elevate product quality. This guide delves into actionable strategies to perfect your bending operations, ensuring every bend meets exacting standards.
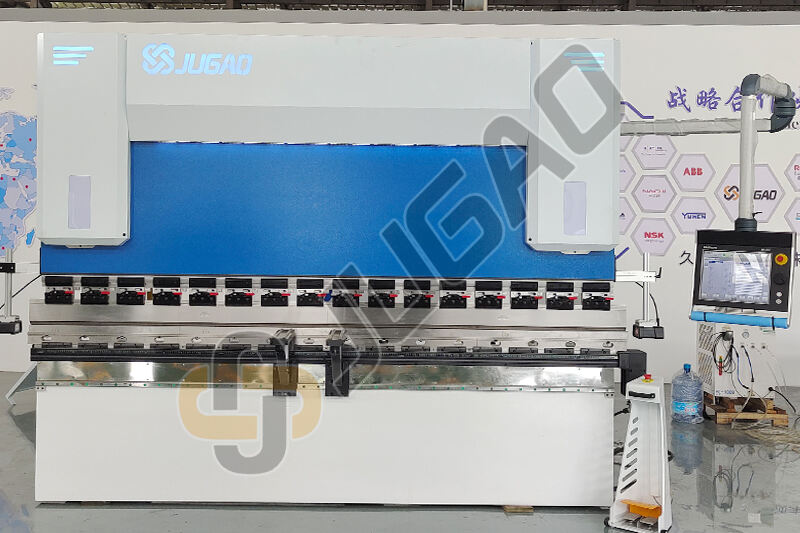
1. The Critical Role of Bending Process Optimization
Why Bending Optimization Matters
Precision in bending directly impacts product integrity, aesthetics, and functionality. Optimized processes minimize rework, lower material waste, and shorten production cycles—key drivers for cost efficiency and customer satisfaction.
Key Factors Influencing Bending Quality
Success hinges on three pillars:
Equipment Capability – Matching machine specifications to material demands.
Tooling Precision – Using dies and punches suited to the bend geometry.
Material Consistency – Ensuring uniformity in metal properties and surface condition.
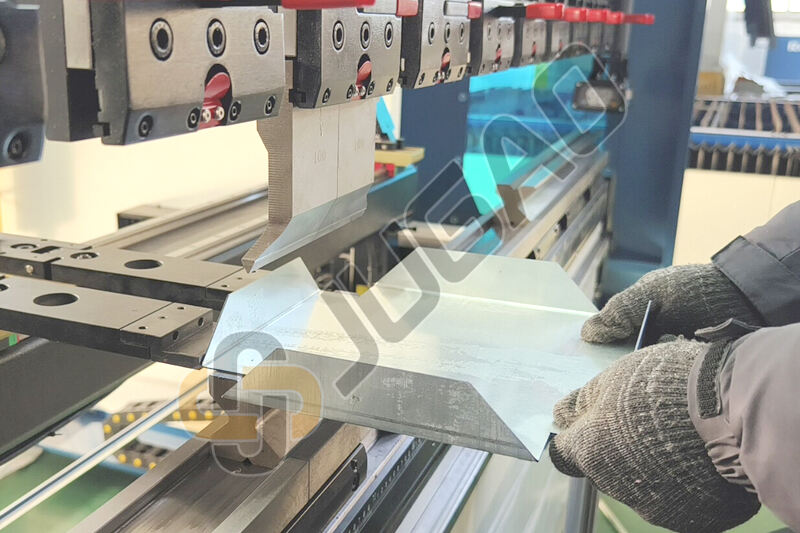
2. A Step-by-Step Guide to Optimizing Bending Operations
Step 1: Selecting the Right Equipment
Choose a press brake based on:
Tonnage and Bed Length – Align with material thickness and bend complexity.
Control Systems – CNC-enabled machines offer superior repeatability for intricate designs.
Pro Tip: Hydraulic brakes excel in heavy-gauge bending, while electric models provide energy savings for thin materials.
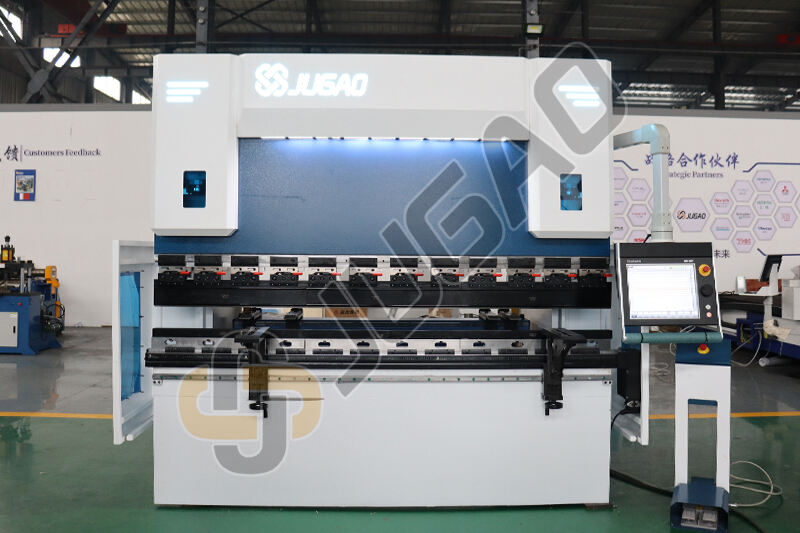
Step 2: Precision Tooling Configuration
Die and Punch Selection – Refer to manufacturer charts for optimal tool pairing.
Avoiding Springback – Use compensating techniques or air bending for resilient metals.
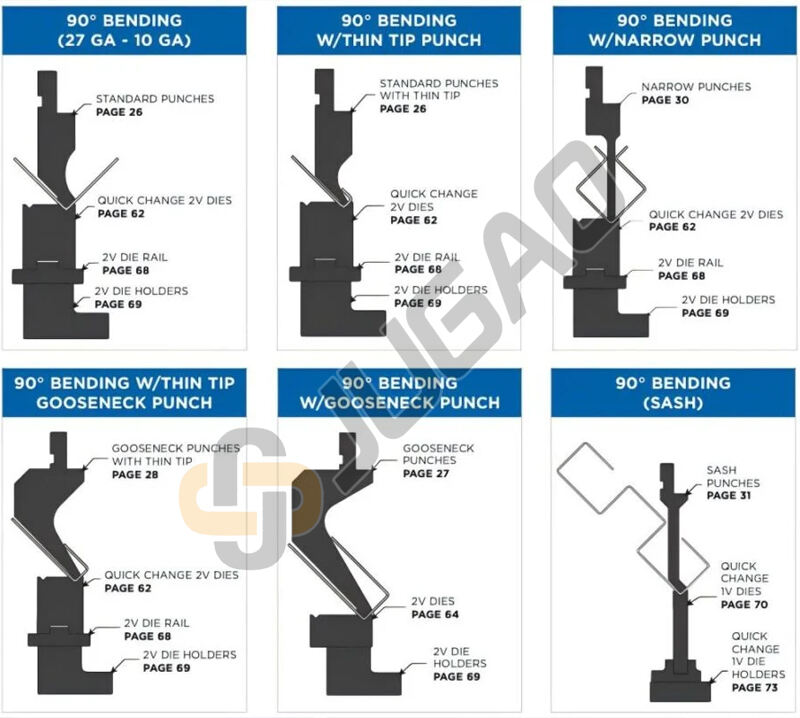
Step 3: Material Readiness and Handling
Surface Preparation – Remove contaminants like oil or scale to prevent imperfections.
Pre-Bend Marking – Laser or scribe lines ensure bend accuracy.
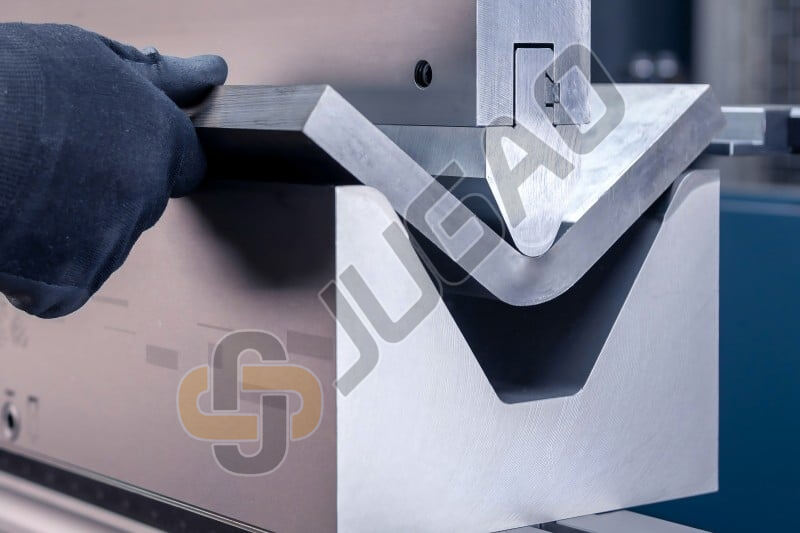
Step 4: Calibration and Quality Assurance
Backgauge Alignment – Verify positioning with digital measurement tools.
Test Bends – Conduct sample runs to validate settings before full production.
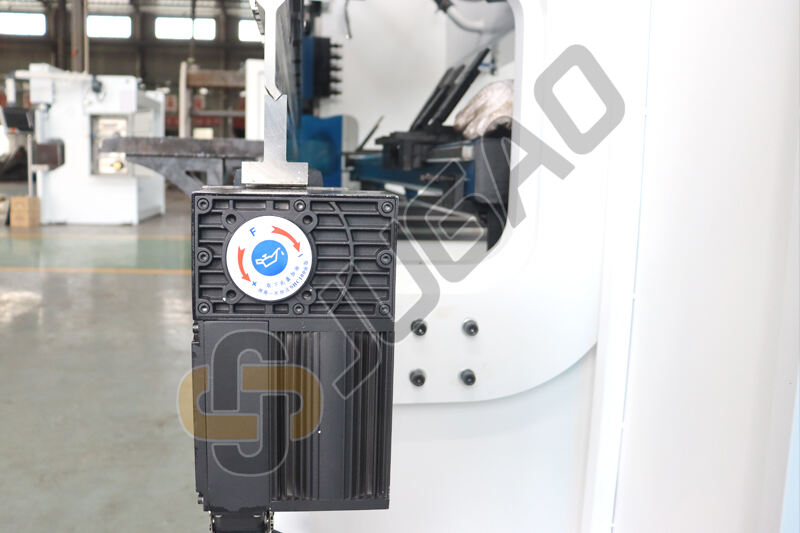
3. Troubleshooting Common Bending Challenges
Recognizing Frequent Bending Defects
Inconsistent Angles – Often caused by tool wear or misalignment.
Surface Scratches – Result from dirty tooling or improper material handling.
Proactive Solutions for Consistent Results
Routine Tool Inspections – Replace worn dies promptly.
Lubrication Protocols – Reduce friction to extend tool life and improve finish.
4. Expert Answers to Press Brake FAQs
Q: What’s the most reliable method for press brake calibration?
A: Begin with machine leveling, then use a digital angle finder to fine-tune the ram and dies. Regular laser calibration is recommended for high-volume operations.
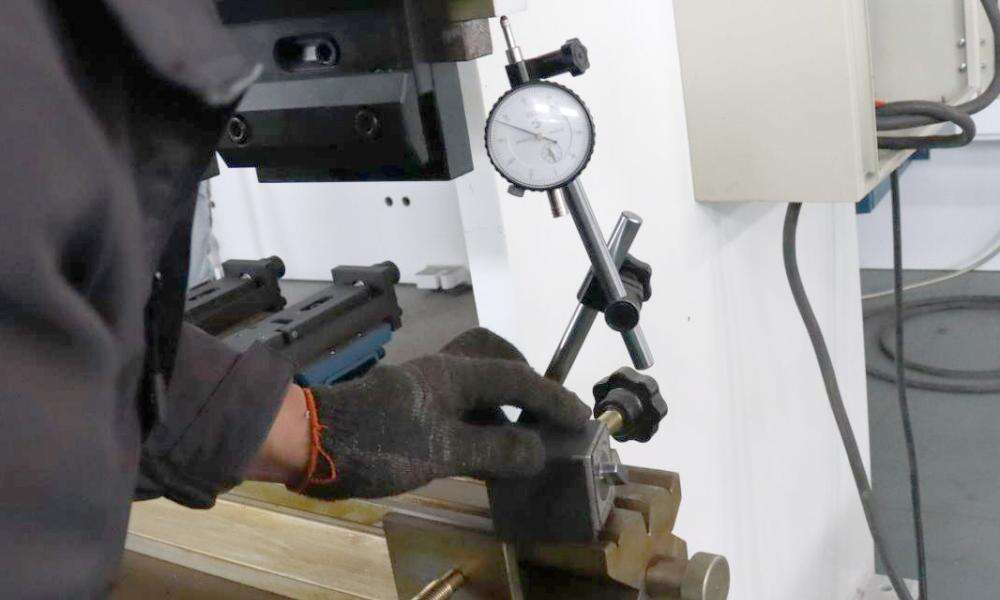
Q: How frequently should maintenance be performed?
A: Schedule inspections every 500 operational hours, focusing on hydraulic systems, guides, and electrical components.
5. Final Thoughts on Achieving Flawless Bends
Mastering bending optimization requires a blend of technical knowledge and meticulous execution. By investing in the right equipment, maintaining rigorous standards, and addressing issues proactively, fabricators can achieve unparalleled precision and efficiency. For tailored advice or advanced troubleshooting, consult with JUGAO CNC MACHINE to keep your operations at the cutting edge.
Optimize today—excel tomorrow.
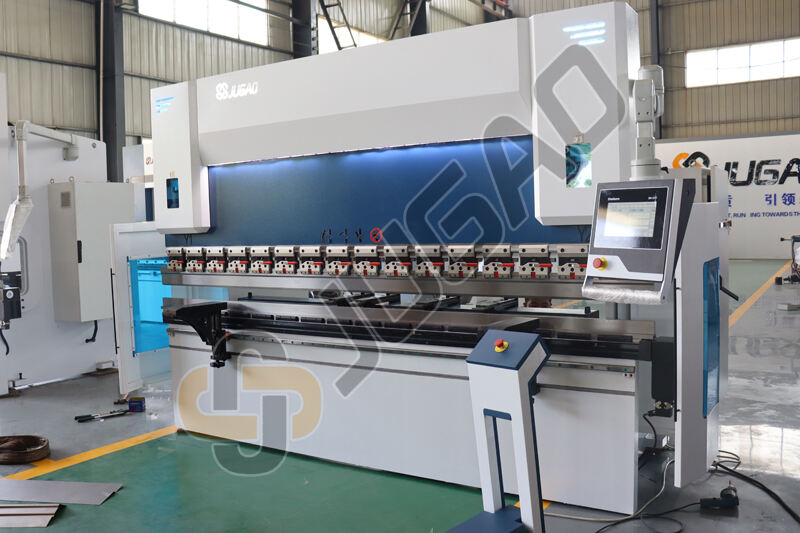
Key Takeaways:
✔ Prioritize equipment and tooling compatibility.
✔ Implement strict material prep and calibration routines.
✔ Adopt preventive maintenance to sustain performance.
This revised version enhances clarity, flow, and practicality while preserving the original’s technical foundation. If you'd like further refinements, Contact JUGAO CNC MACHINE!