The Essential Role of Press Brakes in Modern Appliance Manufacturing
In today's competitive appliance manufacturing sector, press brakes serve as fundamental equipment for producing high-precision metal components. These sophisticated machines transform flat metal sheets into the complex geometries required for refrigerators, cooking ranges, laundry equipment, and other essential household appliances. This comprehensive guide explores the strategic implementation of press brake technology, offering professional insights to enhance your manufacturing operations, whether you're establishing new production lines or optimizing existing processes.
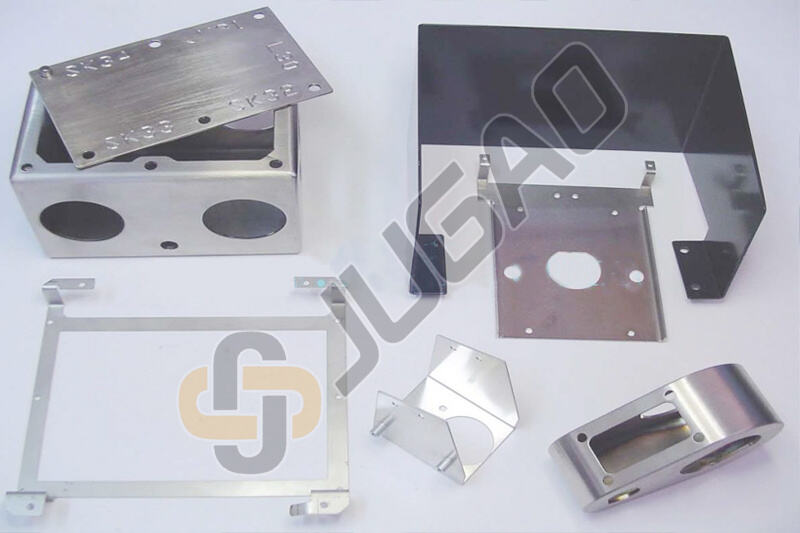
The Critical Functions of Press Brakes in Appliance Production
Achieving Micron-Level Precision in Component Fabrication
Contemporary appliance designs demand exceptional dimensional accuracy for proper assembly and functionality. Press brake systems, particularly CNC-controlled models, deliver the necessary precision for fabricating critical components such as:
Refrigeration system enclosures
Cooking appliance structural elements
Laundry machine chassis components
Ventilation system ductwork
Modern CNC press brake technology enables operators to program exact bending parameters, ensuring consistent replication of complex geometries across production runs. This capability proves particularly valuable when working with premium materials like brushed stainless steel, where even minor dimensional variations can compromise product quality.
Enhancing Production Efficiency for Mass Manufacturing
In high-volume appliance production environments, press brake systems provide significant operational advantages:
Automated bending sequences reduce manual intervention
Quick-change tooling systems minimize setup durations
Advanced measurement systems optimize material utilization
Integrated quality control features reduce rework requirements
These efficiency gains become particularly apparent when processing large batches of standardized components, allowing manufacturers to meet demanding production schedules while maintaining strict quality standards.
Optimizing Press Brake Configuration for Appliance Fabrication
Proper machine configuration forms the foundation for successful appliance component production. Follow these professional guidelines to ensure optimal press brake performance.
Workspace Preparation and Safety Considerations
Establishing an appropriate working environment involves:
Conducting thorough area inspections to eliminate potential hazards
Verifying machine leveling to prevent operational inaccuracies
Implementing proper illumination for visual inspection needs
Ensuring clear access paths for material handling operations
Tooling Selection and Configuration Strategies
Effective tooling management requires:
Careful selection of dies based on material specifications
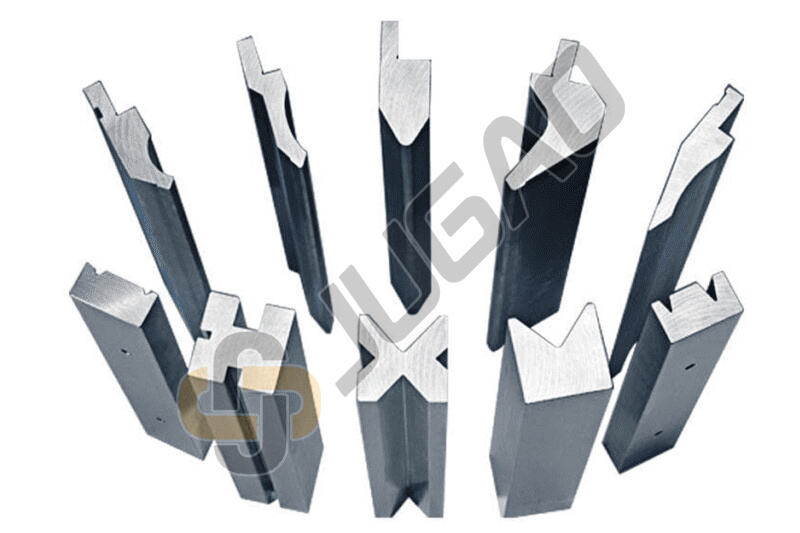
Proper installation and secure fastening of all tooling components
Comprehensive testing using sample materials before full production
Special consideration for material-specific requirements (e.g., wider V-dies for stainless steel applications)
Precision Calibration Techniques for Consistent Results
Achieving repeatable accuracy demands:
Meticulous backgauge alignment using digital measurement tools

Regular verification against technical specifications
Implementation of laser alignment systems for critical applications
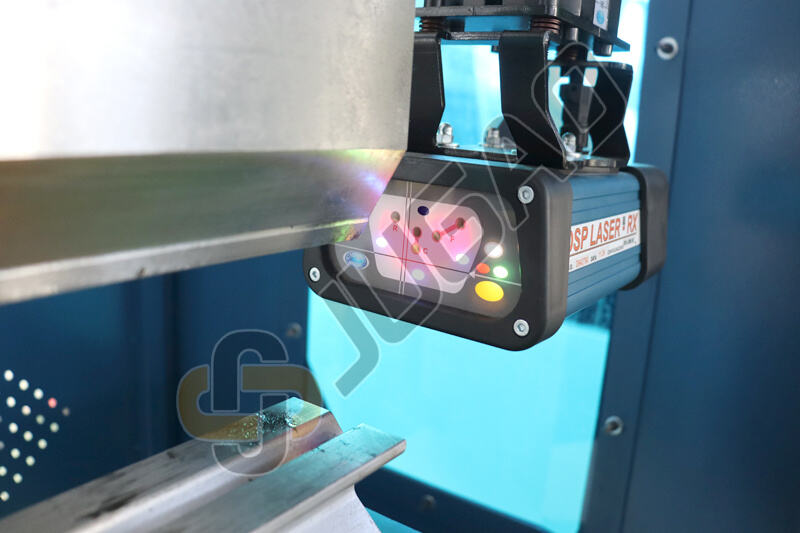
Continuous monitoring to maintain tolerances within acceptable ranges
Ensuring Long-Term Operational Excellence
Maintaining peak press brake performance requires a structured maintenance approach.
Comprehensive Maintenance Protocols
Implement a systematic inspection routine that includes:
Hydraulic system condition assessments
Electrical component evaluations
Tooling wear analysis
Structural integrity verification
Optimal Lubrication and Cleaning Procedures
Develop maintenance practices that incorporate:
Regular removal of particulate contaminants
Appropriate lubrication of moving components
Use of manufacturer-approved maintenance products
Scheduled deep-cleaning operations
Troubleshooting Common Operational Challenges
Address typical production issues through:
Systematic diagnosis of dimensional inconsistencies
Pressure system evaluations
Tooling alignment verification
Reference to manufacturer technical resources
Expert Insights: Press Brake Applications in Appliance Manufacturing
Q: What press brake specifications are most suitable for appliance production?
A: CNC hydraulic press brakes with advanced control systems provide the ideal combination of precision and productivity for high-volume appliance manufacturing.
Q: How can material deformation be minimized during bending operations?
A: Implementing controlled bending speeds, utilizing specialized tooling configurations, and applying uniform pressure distribution techniques can significantly reduce material stress.
Q: Are press brakes capable of producing customized appliance components?
A: Modern CNC systems can accommodate virtually any design requirement, from prototype development to specialized production runs.
Q: What is the recommended tooling replacement schedule?
A: Conduct monthly inspections and plan for complete tooling replacement every 18-24 months, adjusting for production volume and material characteristics.
Advancing Your Manufacturing Capabilities
Press brake technology continues to evolve, offering appliance manufacturers unprecedented opportunities to enhance product quality and production efficiency. By implementing the strategies outlined in this guide, manufacturers can achieve:
Improved production consistency
Enhanced material utilization
Reduced operational costs
Increased manufacturing flexibility
For organizations seeking to upgrade their fabrication capabilities or requiring specialized technical consultation, professional equipment providers offer JUGAO CNC MACHINE comprehensive support services and cutting-edge press brake solutions specifically designed for the appliance manufacturing sector. Consider scheduling a professional assessment to identify potential improvements in your bending operations.