Four Fundamental Facts Regarding Notching Machines
Within the realm of sheet metal fabrication, notching machines play a pivotal role in achieving precise cuts and shapes. A comprehensive understanding of their features and capabilities can markedly elevate production efficiency and the caliber of the end products. Whether one is a newcomer to the industry or contemplating the upgrade of existing equipment, these insights will serve as a guide for making judicious decisions. Let us delve into the pivotal aspects of notching machines that can refine your workflow and enhance your operational processes.
Principle
As the terminology implies, a notching machine is a tool designed for cutting, but what precisely does it cut? In essence, the notching machine is predominantly utilized for the cutting of metal plate materials. It finds extensive application across numerous sectors, including automobile manufacturing, shipbuilding, elevator construction, electrical apparatus, piping, culinary utensils, and stainless steel products.
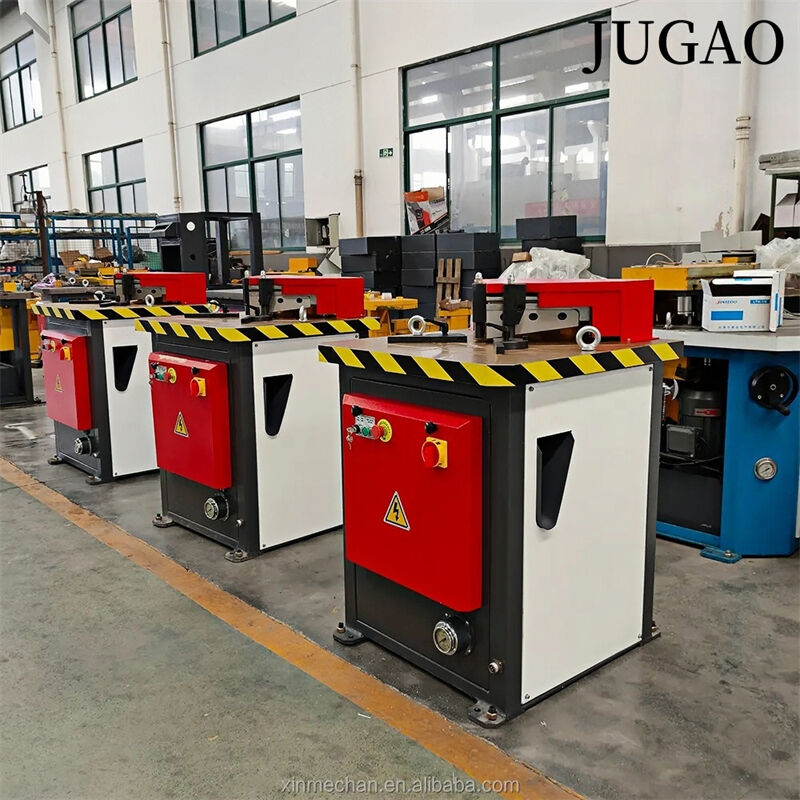
Evolution
The fundamental structure of the notching machine consists of steel plates that are integrally welded, conferring upon it exceptional robustness and durability. Only the tools provided with the standard machine are capable of meeting the processing requirements of typical sheet metal fabrication facilities. In contrast to conventional punching machines, there is no need to fabricate a set of molds for processing components with specific angles or thicknesses. The utilization of notching machines reduces costs, alleviates the inconvenience associated with the frequent replacement and clamping of molds inherent in traditional punches, and enhances operational efficiency. Furthermore, it serves to diminish the physical exertion of workers, mitigate occupational hazards, and concurrently, the implementation of low-noise processing fosters a tranquil working environment for both the factory and its workforce. What, then, are the principal classifications of notching machines? The subsequent discourse primarily elucidates the three prevalent types of notching machines and their distinctive attributes:
⒈ Pedal notching machine: As the name suggests, it operates using the pedaling method, which not only conserves effort during operation but also markedly enhances work efficiency. Additionally, the scissors of the general Pedal notching machines are typically made of silicon, and the blades are not easily damaged.
⒉ Pneumatic notching machine: It is primarily utilized for cutting the corners of square metal boxes and metal disk boxes. The primary feature is its relatively light weight, coupled with a style that is aesthetically pleasing and innovative, and there is no concern regarding cutting quality.
⒊ Hydraulic notching machine: It predominantly employs hydraulic transmission, which not only possesses sufficient strength but also exhibits a degree of toughness, rendering it suitable for various needs of various hardware processing industries, and it is also the most prevalent type of notching machine in the market.
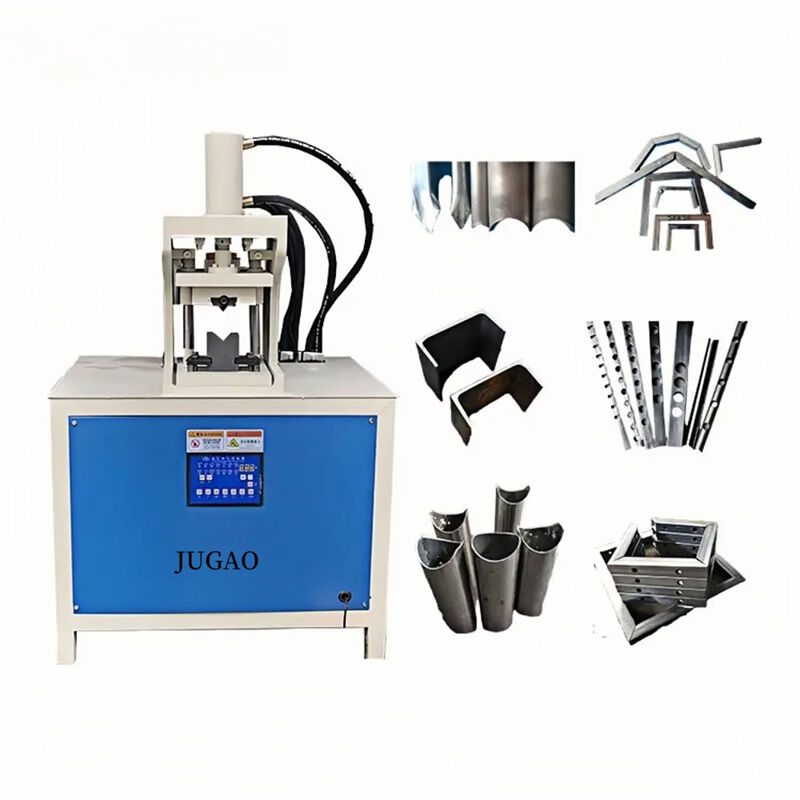
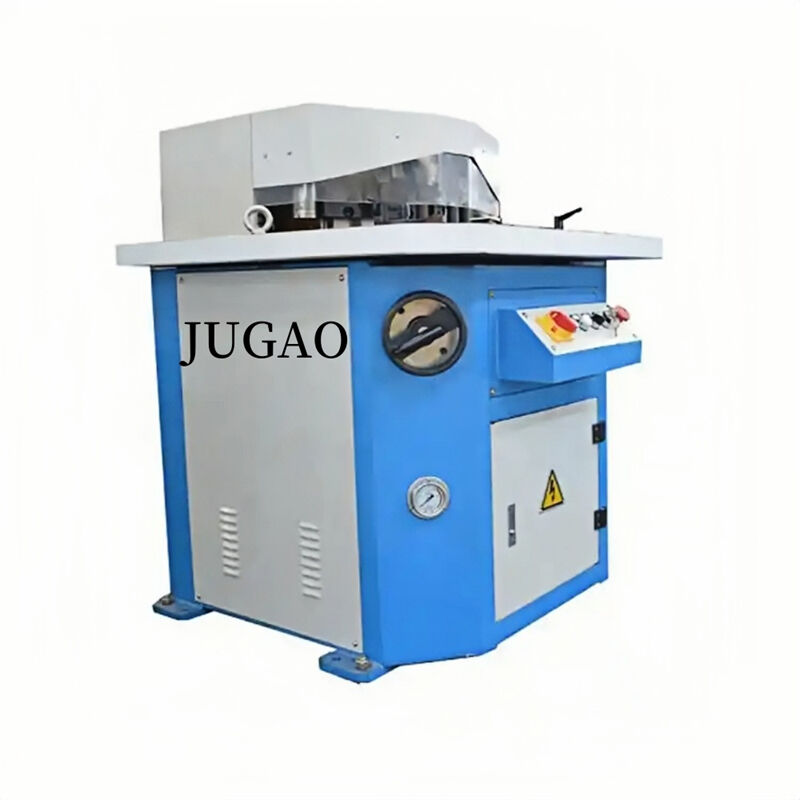
Classification
From a professional perspective, the notching machine can be categorized into adjustable and fixed types based on the varying angles of the blades at both ends. The fixed angle hydraulic notching machine boasts a shearing angle of 90 degrees, rapid shearing speed, compact structure, small volume, and convenient operation.
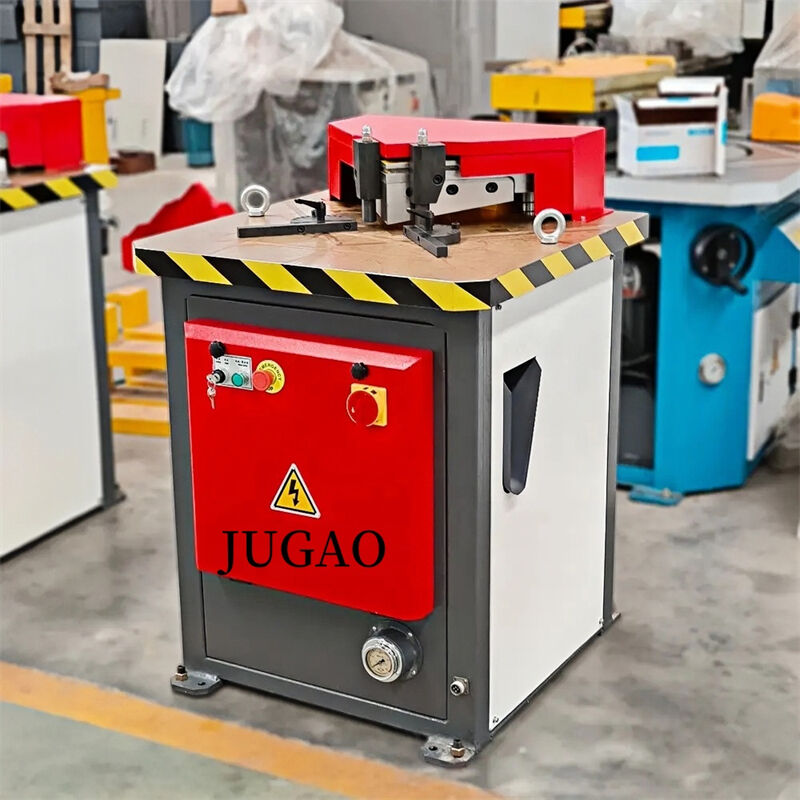
The adjustable angle hydraulic notching machine offers a relatively broad range of shearing angles, high shearing precision, and the cutting angle typically ranges from 40 to 135 degrees. If one wishes to adjust within this range, an ideal shearing state can be achieved; symmetrical or asymmetrical adjustment processing is suitable for various thicknesses and materials, resulting in a smooth and seamless cut of the sheet.
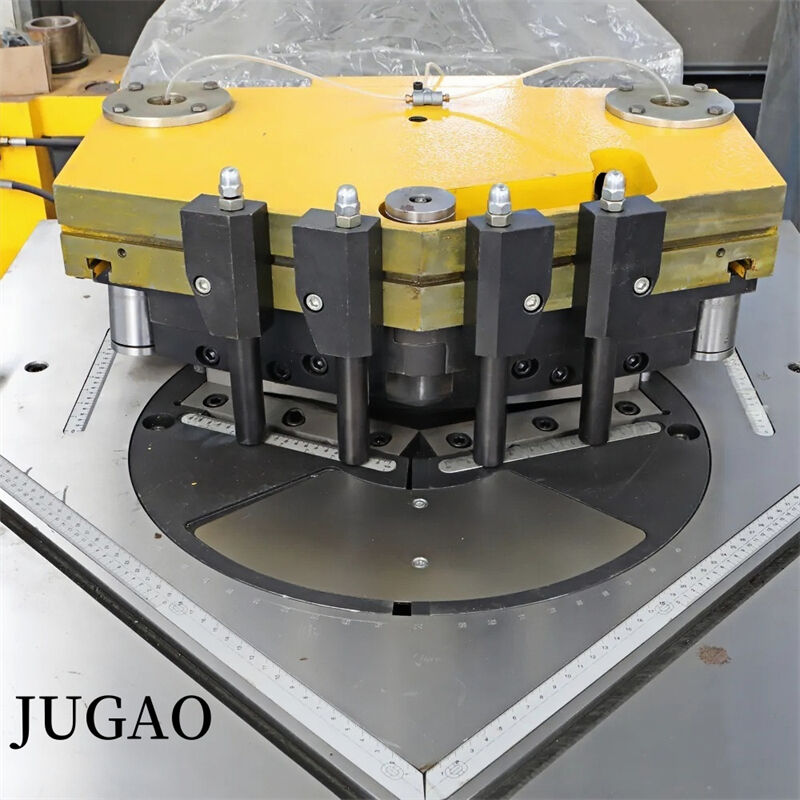
Features
The characteristics of the fixed angle notching machine are as follows: 1. The blade gap is automatically adjusted in accordance with the thickness of the shearing board. 2. Utilizing hydraulic transmission. 3. The fixed shear angle is 90 degrees. 4. Featuring an adjustable angle scale device. 5. The entire machine is constructed from a steel plate welded into an integral structure. 6. Equipped with a centralized lubrication system. The configuration is outlined below:
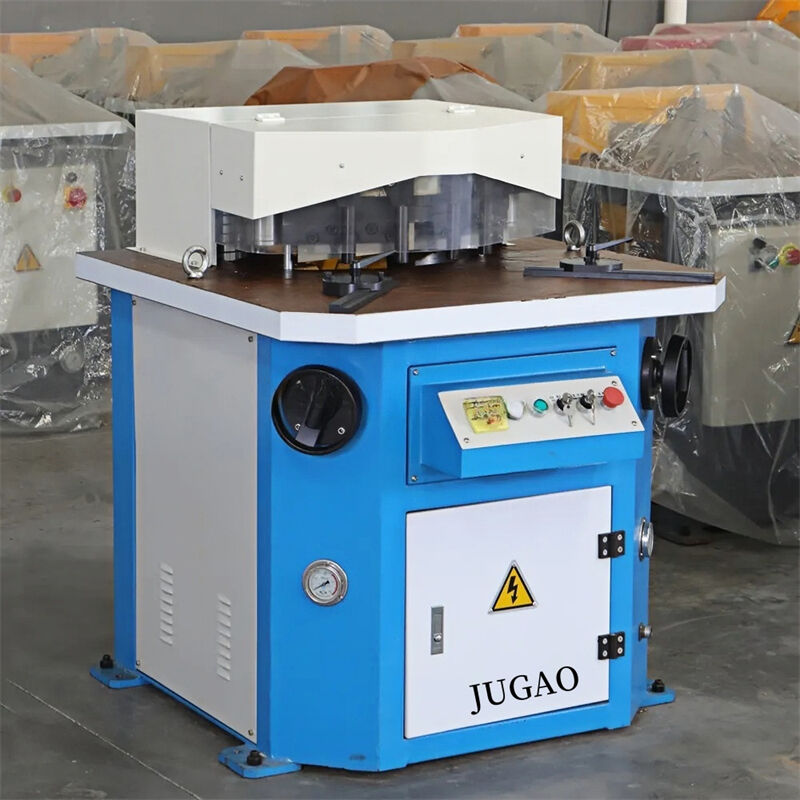
The adjustable angle notching machine is a shearing angle adjustment mechanism specializing in machinery, electricity and hydraulics. The blade gap can be automatically adjusted according to the thickness of the shearing plate. The specific configuration is as follows:
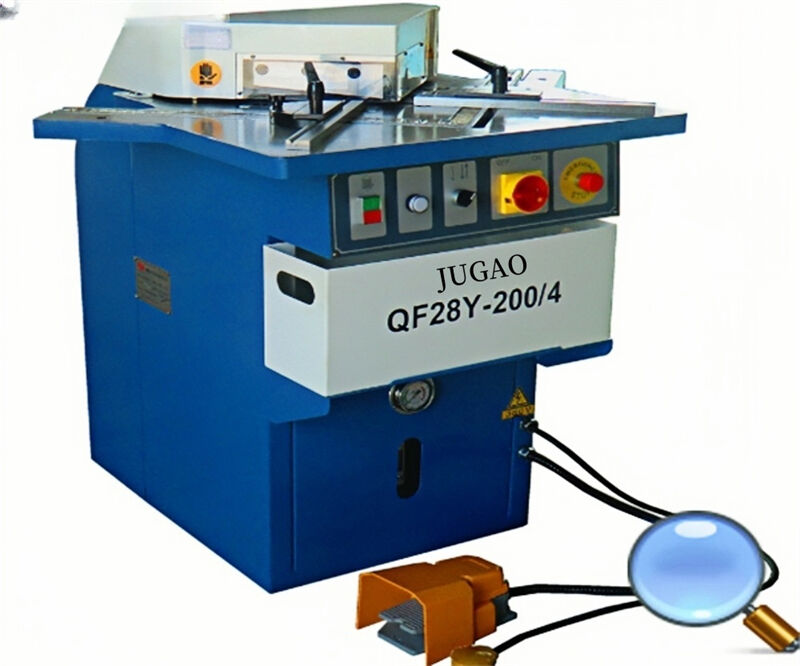
About Gary Olson
As a dedicated author and editor for JUGAO CNC, I specialize in delivering insightful and practical content tailored to the metalworking industry. With years of experience in technical writing, I focus on providing in-depth articles and tutorials that help manufacturers, engineers, and professionals stay informed about the latest innovations in sheet metal processing, including CNC press brakes, hydraulic presses, shearing machines, and more.