Essential Information Regarding Shearing Blades
As an individual with profound engagement in the sector, I frequently discern that the comprehension of shearing blades is imperative for the optimal functioning of machinery. In this discourse, "Shearing Blades: Essential Facts to Know," my objective is to impart critical insights regarding these pivotal components. I shall navigate you through the salient aspects, ranging from their design and material considerations to maintenance strategies, which can augment your understanding and application of shearing blades. Irrespective of whether you are an experienced practitioner or a newcomer to the field, this guide is intended to assist you in making judicious decisions for your projects.
Table of Contents
· Introduction
· Materials
· Procedures
· Safety Operations
· Maintenance
· Applications
Introduction
The shearing machine typically employs blade materials such as T10, 9CrSI, 6CrW2Si, Cr12MoV, H13, and various alloy steels. These machines find extensive application across multiple sectors including light industry, aviation, shipbuilding, metallurgy, instrumentation, electrical appliances, stainless steel products, steel structure construction, and decorative industries.
Utilizing a movable upper blade in conjunction with a stationary lower blade, the shearing machine exerts shearing force on metal sheets of varying thicknesses through an appropriately calibrated blade gap. This action results in the separation of the sheets along the desired dimensions. As a type of forging machinery, the shearing machine primarily serves the metal processing industry. Common classifications of shearing machines include pedal-operated (manual), mechanical, hydraulic swing, and hydraulic brake models.
Shearing machines are frequently utilized for the cutting of blanks with straight edges. The shearing process must ensure that the sheared surfaces of the cut sheets meet the requirements for straightness and parallelism, while also minimizing sheet distortion to achieve a high-quality end product.
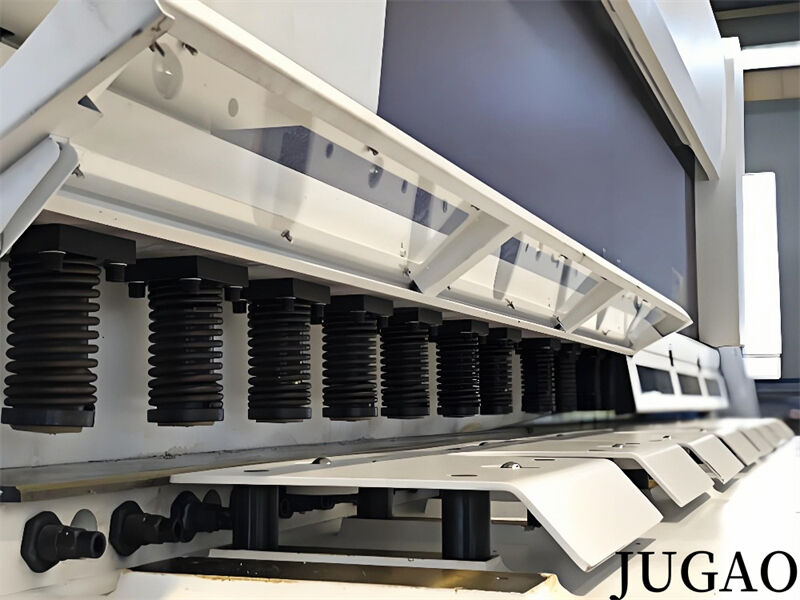
Material
The selection of materials for shear blades encompasses three primary categories: carbon-bonded tool steel, low alloy tool steel, and alloy tool steel.
1. Carbon-bonded tool steel: Typically, carbon-bonded steel encompasses materials such as 65, 75 steel, T8, T10, among others. The heat treatment hardness of blades crafted from these materials ranges from HRC57-59 degrees, rendering them appropriate for processing standard low-carbon cold-rolled plates and common A3 plates. This material's characteristic of being cost-effective and offering a reasonable product price is particularly advantageous when recycling and cutting waste materials.
2. Low-alloy tool steel: Commonly utilized materials for low-alloy tool steel blades include 6Crw2sI, Cr5Mo1V, 9CrSi, and Cr12MoV. The heat treatment hardness of these blades falls within the HRC58-62 degrees range, making them particularly suited for cutting stainless steel, hot-rolled plates, and medium to thick plates.
3. Alloy tool steel: The shear blade materials of alloy tool steel consist of 4Cr5MoSiV1 (H13K), 7Cr7Mo2V2Si9 (LD), W6Mo5Cr4V2 (6542), H13, and others. Blades made from these materials are employed for hot-rolled steel billets and for hot-cutting medium and thick steel plates. Notably, these materials exhibit high temperature resistance and are less prone to annealing, making them suitable for hot rolling and hot shearing processes in steel mills.
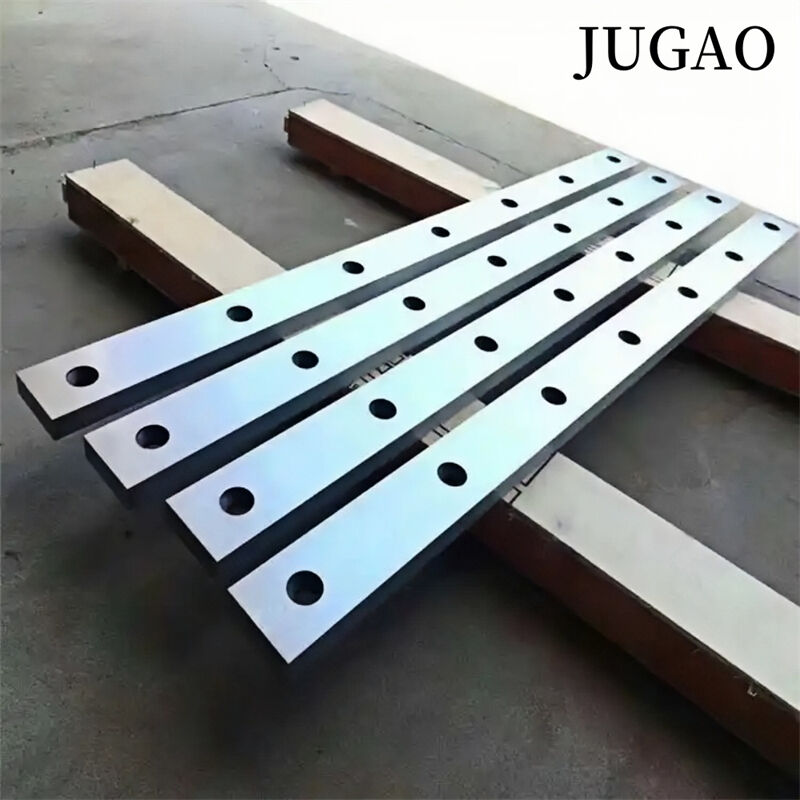
Instructions
1. Initiate the shearing machine for several cycles of idling to verify its normal operation and conduct test cuts of varying thicknesses, from thin to thick. Ensure the operator is well-acquainted with the blade performance of the hydraulic guillotine shearing machine.
2. Adjust the blade gap according to the thickness of the plate during trial cutting. Failure to adjust the corresponding blade gap can lead to compromised blade durability.
3. Activate the pressure gauge switch during the cutting operation and monitor the oil pressure reading. The pressure should not exceed 20MPa when cutting a 12mm plate. The remote pressure regulating valve No9 is factory-set to 20-22MPa; users are required to adhere to this setting and must refrain from increasing the pressure beyond the specified limit to avoid machine damage.
4. Maintain operational sound balance. Should noise be detected on the blades of the hydraulic guillotine shearing machine, cease operations and conduct an inspection.
5. During the operation of the hydraulic guillotine shear blade, ensure that the oil tank's maximum temperature remains below 60 degrees Celsius. If the temperature exceeds this limit, the machine should be shut down and allowed to rest.
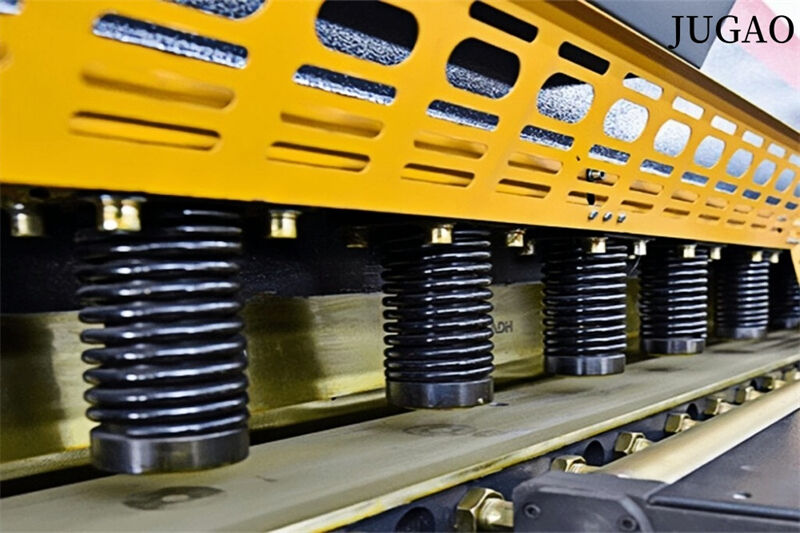
1.Ensure that protective clothing is snug-fitting, secure the cuffs, and refrain from opening the jacket's hem. Avoid wearing, removing, or draping clothing over the machine to prevent entanglement. Safety helmets are mandatory, with braids tucked inside the hat; skirts and slippers are prohibited.
2. Operators of this machine tool must be well-versed in the primary structure, functionality, and operation of the hydraulic guillotine shear blade.
3. This machine tool is designed for cutting a variety of steel, copper, aluminum, and non-metallic material plates, provided the material thickness does not exceed the machine's rated capacity. Materials must be free of hard marks, welding slag, slag inclusions, and welds, and excessive thickness is not permissible.
4. Instructions for using the blades of a hydraulic guillotine shearing machine:
A. Adjust the blade clearance to match the thickness of the material to be cut.
B. Modify the profiling or fixture in accordance with the width of the material intended for cutting.
C. Execute 1-3 idle strokes prior to operating the machine; cutting work may commence once the machine is functioning normally.
5. Should any operational irregularities be detected during use, promptly disconnect the power and conduct an inspection before restarting.
6. When adjusting the machine tool, ensure the power supply is disconnected. Exercise caution with hand safety when moving workpieces.
7. Maintain frequent lubrication of all machine components. Operators should replenish lubricating oil once per shift, while mechanics should apply lubricant to rolling bearing parts semi-annually.
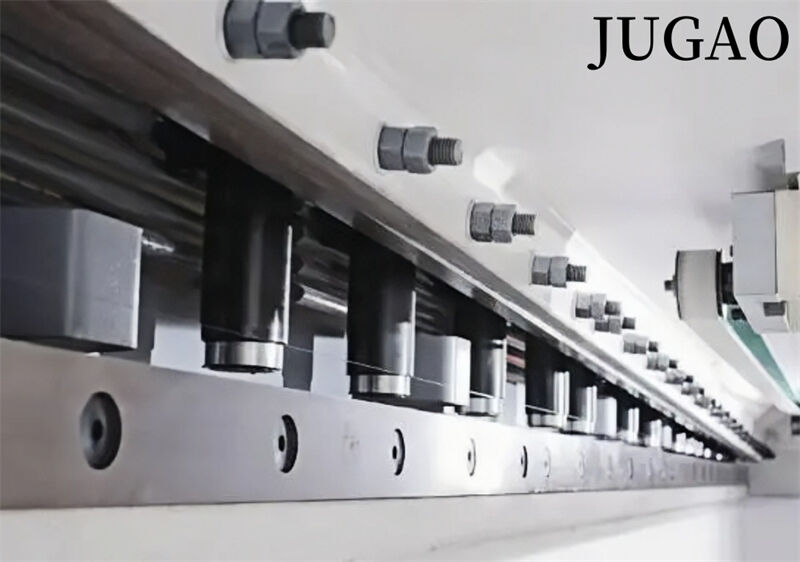
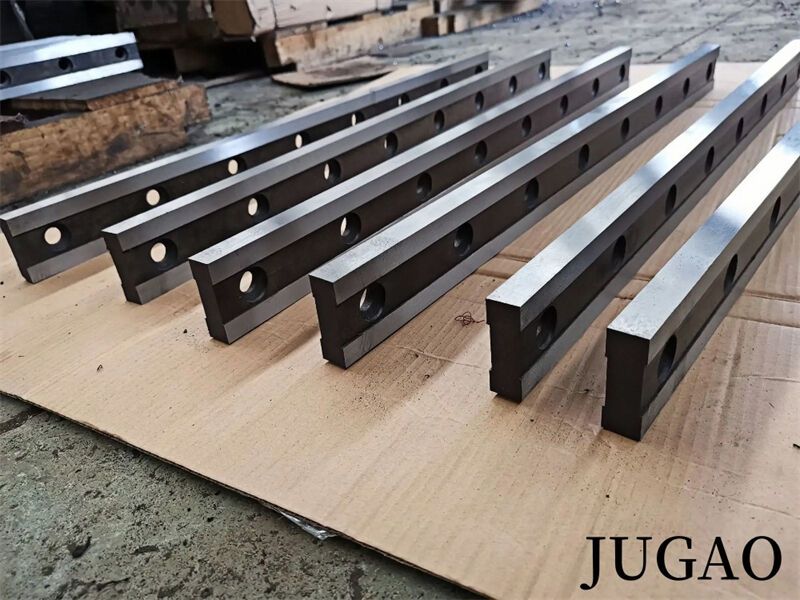
Maintenance
Proper maintenance of the shear blade is essential for extending its lifespan and ensuring user comfort. The shear blade, being a type of forging machinery, primarily serves the metal processing industry. The following outlines the maintenance procedures for the shear blade.
1. Adhere strictly to operating protocols.
2. Prior to each machine startup, apply lubricating oil as stipulated by the lubrication chart. Ensure the oil is clean and free from sediment.
3. Regularly clean the shear blades, applying anti-rust grease to any unpainted areas.
4. Routinely replace and refill the lubricating oil in the motor bearings, and conduct regular inspections of the electrical components to guarantee normal, safe, and reliable operation.
5. Periodically inspect the shearing machine blade's triangle belt, handle, knob, and button for damage. If the blade exhibits severe wear, replace it promptly and report the need for spare parts.
6. Regularly check and repair switches, insurances, and handles to ensure dependable operation.
7. Lubricate and clean the machine tool 10 minutes before the end of each workday.
8. Strictly prohibit operation by unauthorized personnel, and ensure the machine is halted by authorized individuals.
9. Select the shearing gap appropriately based on the board's thickness.
10. Ensure the board is free from impurities and hard objects.
11. Avoid cutting and welding old boards.
12. Refrain from excessive shearing of thick plates, and routinely adjust the gap between the upper and lower blades.
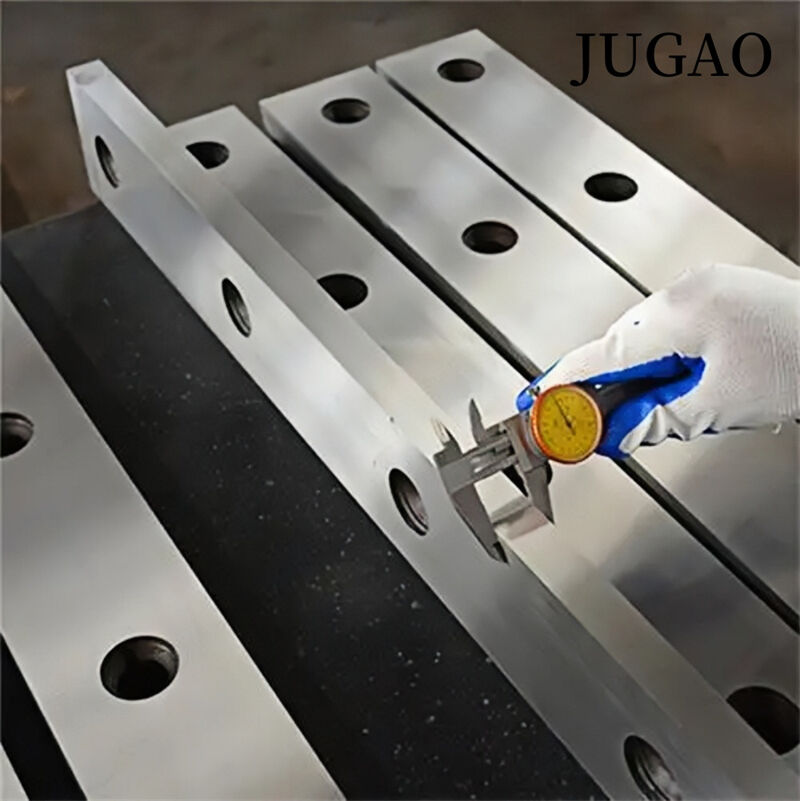
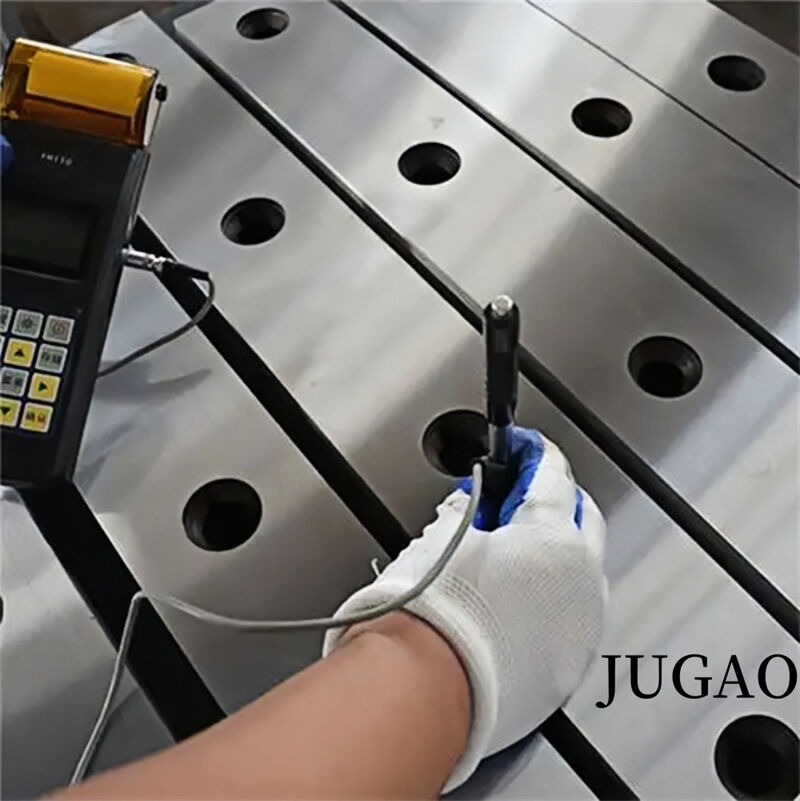
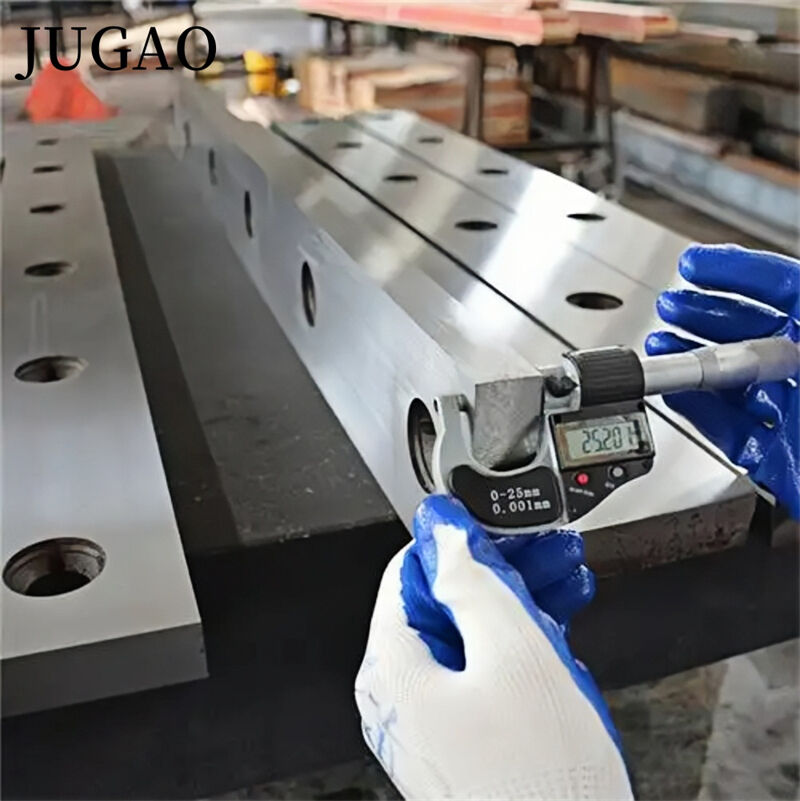
Application
Small and medium-sized CNC shearing machine blades are utilized in hydraulic guillotine shearing machines, hydraulic pendulum shearing machines, mechanical shearing machines, pedal shearing machines, and various other forging machine tools. They are commonly employed in sheet metal processing, light industry, electrical appliances, metallurgy, instrumentation, shipbuilding, aviation, stainless steel products, steel structure construction, and the decoration industry. Their application spans numerous major fields, including metallurgy, packaging, paper, printing, carton, garden wood, rubber and plastic, food, electronic materials, shipbuilding, construction and repair, automobile manufacturing, and mechanical equipment.
About Gary Olson
As a dedicated author and editor for JUGAO CNC, I specialize in delivering insightful and practical content tailored to the metalworking industry. With years of experience in technical writing, I focus on providing in-depth articles and tutorials that help manufacturers, engineers, and professionals stay informed about the latest innovations in sheet metal processing, including CNC press brakes, hydraulic presses, shearing machines, and more.