Distinguishing Between CNC and NC Press Brakes: An Elucidation of Fundamental Distinctions
In this discourse, I shall undertake an exploration of the principal distinctions between Computer Numerical Control (CNC) and Numerical Control (NC) press brakes. As I navigate the complexities inherent in each system, you will attain a more lucid comprehension of their operational mechanisms and respective merits. Whether your intent is to upgrade your existing machinery or merely to augment your comprehension, the recognition of the differences between CNC and NC press brake systems is imperative. Accompany me as we dissect the characteristics, advantages, and optimal applications of these indispensable machines within the sheet metal fabrication sector.
Overview
Upon the intention to acquire a press brake, an individual may experience confusion between CNC press brake and NC press brake. Indeed, there exist numerous distinctions between these two types of press brake machinery. Today, we shall elucidate several key aspects that differentiate CNC press brakes from NC press brakes. It is our hope that this information will provide assistance when initiating your business endeavors. For the purpose of this discussion, we shall refer to the torsion-bar type press brake as the "NC Press brake" and the Electro-hydraulic type press brake as the "CNC press brake".
CNC Press Brake
Nc Press Brake
Difference
Structure
The design principles of the two machines differ, leading to distinct synchronous structures on either side of the ram. The NC press brake employs a torsion shaft to link both sides of the ram, compelling synchronous movement in an up-and-down direction. Consequently, the NC press brake relies on a mechanical compulsory synchronous method, which precludes the ability to self-check and adjust the parallelism of the ram.
In contrast, the CNC Press Brake is equipped with two linear encoders on either side of the machine. The CNC controller utilizes feedback from these encoders to analyze the synchronous state of the ram. Should discrepancies arise, the controller initiates adjustments via a proportional valve to maintain ram synchronization. The CNC controller, hydraulic system, and linear encoders together constitute a closed-loop control system.
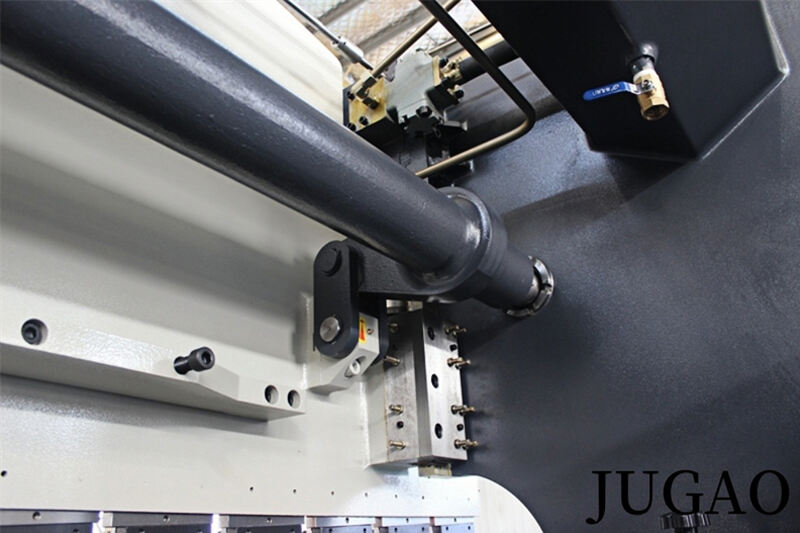
Torsion-bar
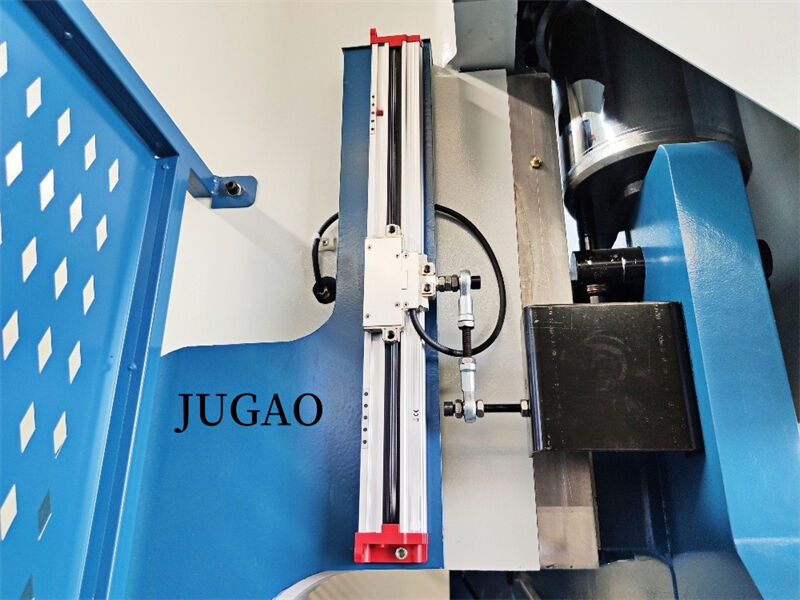
Linear encoder
Accuracy
Ram parallelism significantly influences the accuracy of the workpiece. The synchronization of the NC Press brake is maintained mechanically and lacks real-time feedback for error correction, which results in its inability to self-adjust, thereby leading to diminished bending accuracy. In the case of the NC press brake, the torsion-bar forces both cylinders to move in unison. Prolonged exposure to partial loads can induce deformation in the torsion-bar.
Conversely, the CNC Press brake employs a controller to manage ram synchronization through a proportional valve. Additionally, a linear encoder provides feedback on errors to the controller. Should an error arise, the linear encoder relays this information, prompting the controller to signal the proportional valve to make necessary adjustments, ensuring ram synchronization and enhancing bending accuracy.
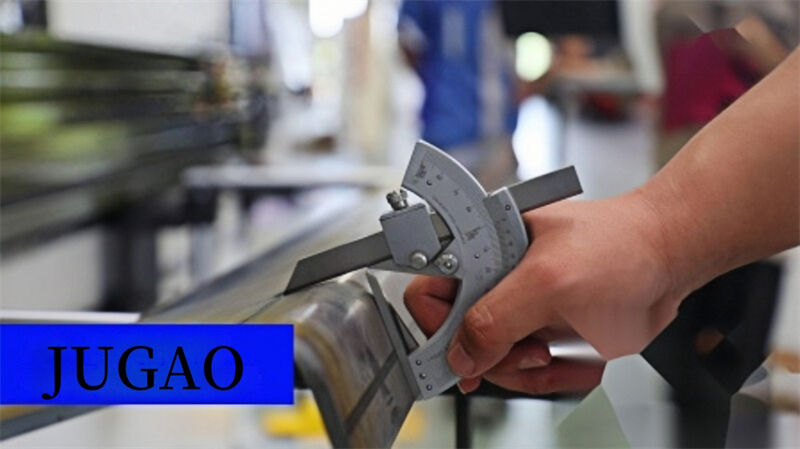
Operating Speed
In the context of press brakes, the discussion typically revolves around three distinct speeds: the downward speed, the working speed, and the return speed. In the case of NC (Numerical Control) Press Brakes, they are equipped with cylinders that have a ratio of 6:1 or 8:1, whereas CNC (Computer Numerical Control) Press Brakes utilize cylinders with a ratio of 13:1 or 15:1, resulting in the CNC Press Brake operating at a higher speed than its NC counterpart. During the downward movement of the ram in an NC Press Brake, the speed is approximately 80mm/s, while the backgauge movement speed is around 100mm/s. In contrast, the CNC Press Brake boasts a ram down speed of up to 200mm/s and exhibits a smooth transition during speed adjustments. Furthermore, its backgauge speed can reach up to 400mm/s, significantly enhancing the overall working efficiency.
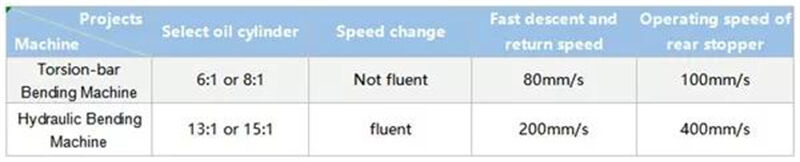
Mechanical Rigidity
Due to its design, the NC press brake is incapable of withstanding partial load bending. Prolonged operation under such conditions may lead to the deformation of the torsion-bar. In contrast, the CNC press brake allows for independent operation of both Y1 and Y2 axes, enabling partial load functionality without the risk of deformation.
Torsion-bar structure
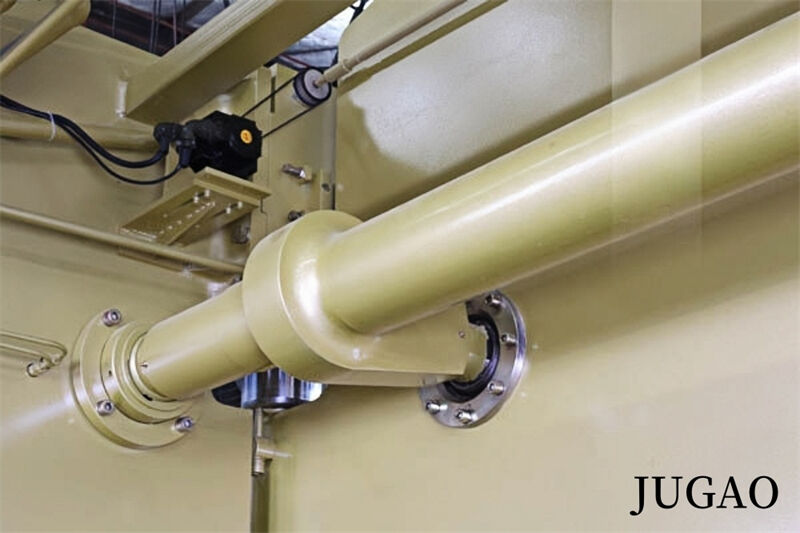
Crowning System
The majority of NC press brakes are not equipped with a crowning system as a standard feature. Operators are required to manually adjust the bending angle prior to the actual bending process, which is time-consuming and results in material waste. Additionally, achieving precise results with this method is challenging.
Customers may opt for a manual crowning system to be included with their press brake. However, this manual approach cannot be equated with the capabilities of a CNC press brake. In the latter, the crowning system is governed by a Controller that adjusts the system based on bending parameters, thereby enhancing both work efficiency and precision.
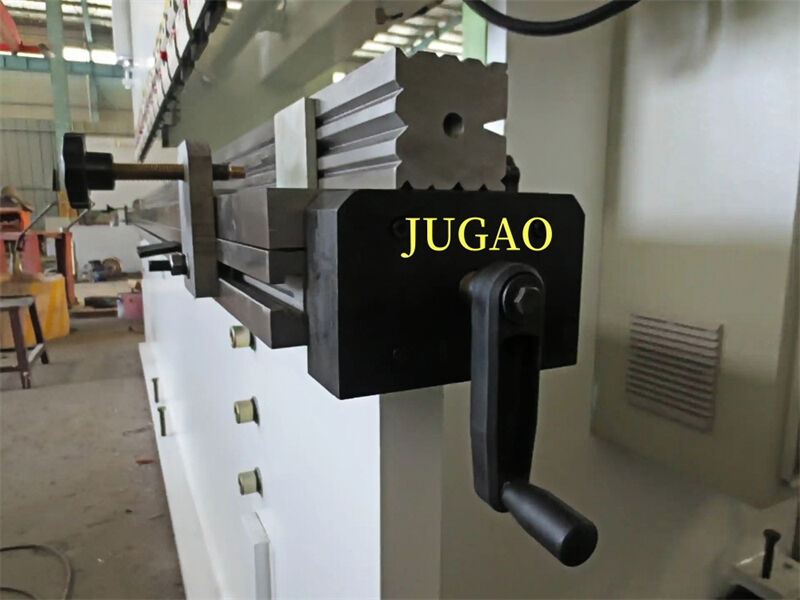
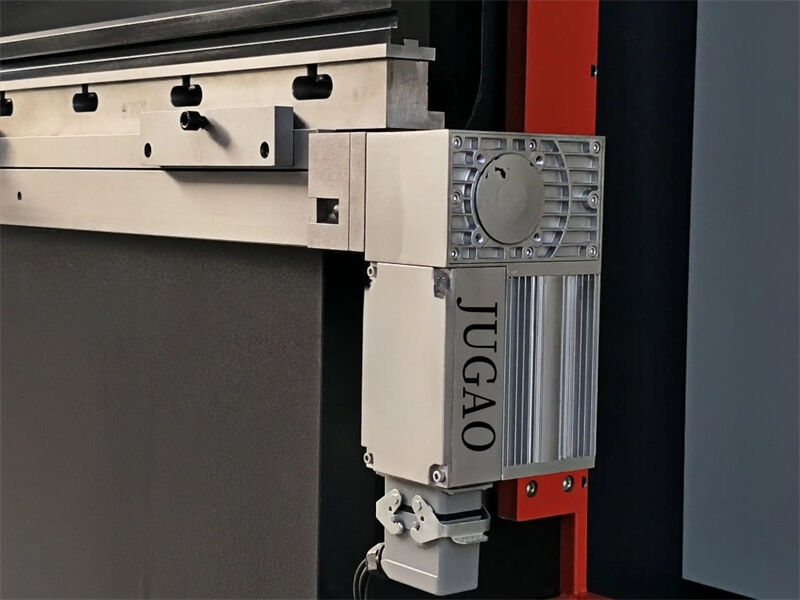
CNC Axis
Numerically controlled press brakes typically have the capability to control only the X and Y axes. In contrast, a CNC press brake can manage a minimum of three axes plus one additional axis. Additional configurations may include four axes plus one, five axes plus one, six axes plus one, seven axes plus one, eight axes plus one, and so forth. This expanded control enables the processing of more complex product bending tasks.
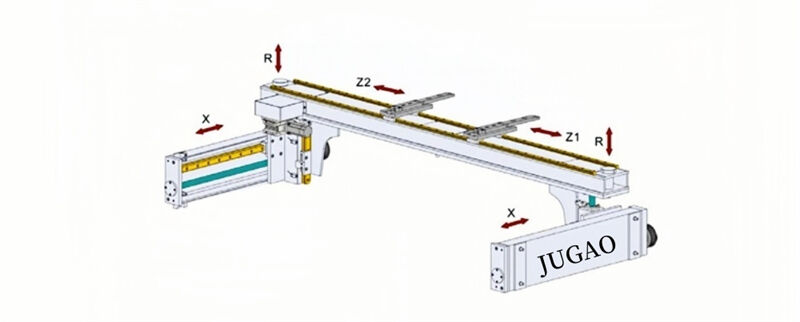
Optional Configurations
For the NC press brake, we shall employ mechanical fast clamps, manual crowning systems, manual height adjustment Z stoppers, ball screws, and linear guides, oil coolers, as well as light curtains. In contrast, the CNC press brake offers additional options beyond those of the NC press brake, including the selection of TYOKKO or AMADA type double-face clamps, hydraulic clamps, robotic arms, sheet followers, laser protection, laser angle measurement, and servo pump units.
Conclusion
No. | Item | Difference | |
CNC press brake | NC press brake | ||
1 | Ram Synchronization | The CNC controller exhibits stable synchronous performance and superior flexibility, enabling the detection and correction of ram inclination. | The torsion rod ensures the synchronization of the ram mechanically. |
2 | Bending angle calculation | The bending angle can be automatically determined by entering the press brake tooling angle, opening, radius, and metal sheet thickness into the CNC controller. | / |
3 | Feedback on Bending Depth | The linear encoder is capable of detecting the position of both sides of the ram and features a throat deformation crowning structure, ensuring a consistent angle within the bending channel's line. | / |
4 | Worktable crowning | The CNC controller is capable of automatically determining the requisite crowning force necessary to counteract worktable deformation throughout the bending process. This ensures the consistency of the bend angle along the entire length and enhances the linearity of the workpiece. | / |
5 | Angular correction | If the programming angle deviates from the actual bending angle, the CNC controller is capable of automatically rectifying the angle upon the user's input of the discrepancy value. | / |
6 | Back gauge position | The system is capable of automatically determining the position of each back-gauge axis based on the bending height, facilitating rapid movement and correction. | Back gauge can only move back and front by manually inputting value |
7 | Programming method | Date or graphical programming facilitates straightforward program modification and editing. | Program cylinder stroke and back gauge movement |
8 | Unfolding length | The CNC Controller is capable of determining the unfolding length through graphic programming of the interior or exterior dimensions. (DA-58T, DA-66T, DA-69T) | / |
9 | Interference calculation | The CNC controller is capable of automatically determining the optimal bending sequence based on the programmable graph, punch and die, machine outline, and will issue an alert in the event of bending interference. Additionally, the bending sequence can be verified and adjusted through manual intervention. | / |
10 | Ram down speed | 160-180mm/s | 80-100mm/s |
12 | Bending angle accuracy | ≤18' | ≤30' |
13 | Back gauge axis | Several CNC axes for optional | Only X axis(back and front) |
Price Comparison
It is observed that for machines with a capacity under 200 tons, the cost of a CNC press brake exceeds that of an NC press brake by more than double. Conversely, when the capacity surpasses 200 tons, the price of a CNC press brake is less than double that of an NC press brake. Consequently, for applications requiring higher bending machine capacity, the CNC press brake is the more advantageous choice.
About Gary Olson
As a dedicated author and editor for JUGAO CNC, I specialize in delivering insightful and practical content tailored to the metalworking industry. With years of experience in technical writing, I focus on providing in-depth articles and tutorials that help manufacturers, engineers, and professionals stay informed about the latest innovations in sheet metal processing, including CNC press brakes, hydraulic presses, shearing machines, and more.