The Core Value of Press Brakes in Elevator and Hoisting Equipment Manufacturing
Content
1. Precision Forming: The Core Process for Building Safety Foundations
2. Technical Compliance: Full-Cycle Assurance from Design to Production
3. Efficient Production: Strategies for Equipment Parameter Optimization
4. Long-Term Maintenance: Critical Measures for Operational Stability
5. Industry Insights: In-Depth Analysis of High-Frequency Questions
6. Technological Advancements: Innovative Pathways Toward Smart Manufacturing
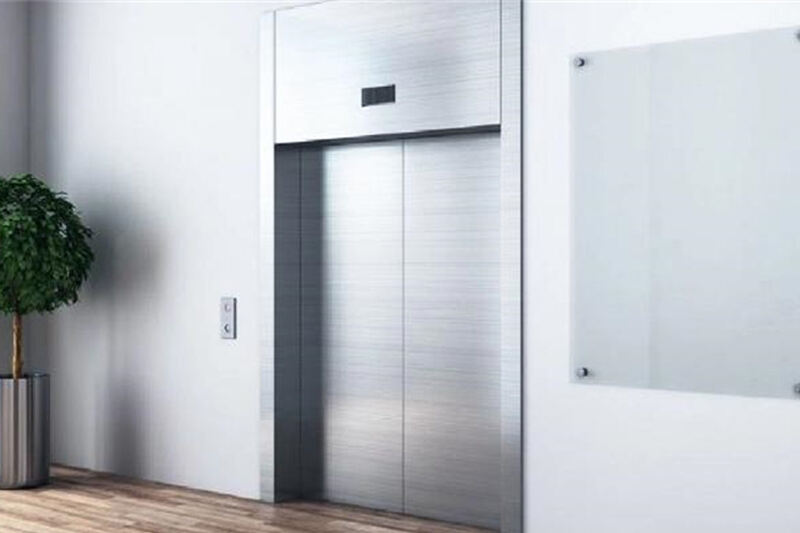
1. Precision Forming: The Core Process for Building Safety Foundations
The functionality of critical components such as elevator cabins and crane load-bearing frames relies on the precise forming of metal parts. Press brakes, with their high-tonnage pressure and CNC precision, enable the processing of high-strength alloys (e.g., wear-resistant steel, aerospace-grade aluminum) into complex geometries, such as the curved cross-sections of elevator guide rails or reinforcement ribs for crane booms. Through multi-axis mold configurations, these machines achieve sharp-angle bends with radii as small as 2mm, meeting compact spatial requirements while ensuring undamaged material lattice structures to prevent stress concentration and potential fractures.
In customized scenarios, press brakes can integrate rotating tube-bending modules or segmented molds to address challenges in fabricating irregular components, such as elevator door linkage mechanisms. For instance, elevator door panels require progressive bending to create continuous corrugated structures for enhanced deformation resistance, while crane pulley brackets demand stepwise bending techniques to balance load distribution.
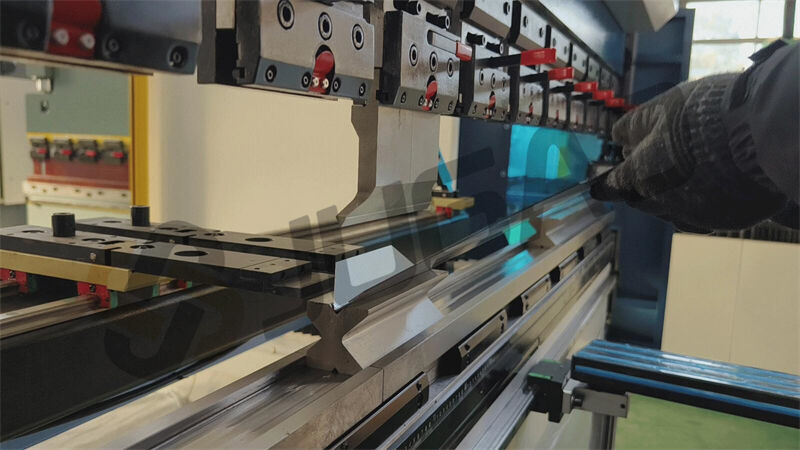
2. Technical Compliance: Full-Cycle Assurance from Design to Production
Global safety standards (e.g., EN 81, ISO 4306) impose stringent tolerance requirements on load-bearing components. For example, bending angle deviations for elevator guide rails must be controlled within ±0.3°. CNC press brakes utilize laser dynamic monitoring systems to real-time correct machining parameters, combined with automatic backgauge compensation to eliminate manual operational errors. Additionally, the machines’ built-in process databases allow one-click retrieval of preset programs, ensuring consistent mechanical performance across mass-produced parts aligned with design specifications.
For risk mitigation, AI algorithms embedded in press brakes predict material springback and automatically adjust ram depth. For instance, when processing crane counterweight blocks from AR500 steel, the system dynamically modifies bending curves based on material hardness characteristics to prevent assembly misalignment caused by springback.
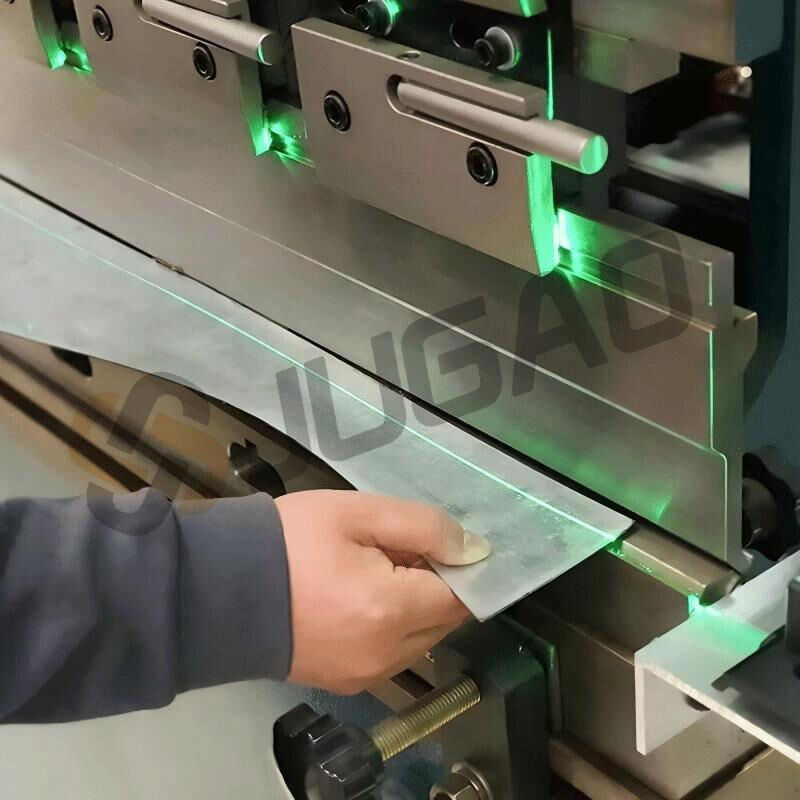
3. Efficient Production: Strategies for Equipment Parameter Optimization
**Key Step 1: Precision Mold Selection**
Select molds based on material properties and machining objectives. Mirror-polished V-dies (opening size = 8×material thickness) are recommended for stainless steel elevator panels to minimize surface scratches, while deep-groove dies (opening ≥30mm) paired with progressive pressure modes are ideal for thick crane hinge components to prevent mold overload.
**Key Step 2: Intelligent Parameter Calibration**
Achieve sub-millimeter backgauge positioning via CNC systems, validated by laser interferometers. For micro-tolerance components like elevator door frames, closed-loop feedback mechanisms ensure backgauge offset ≤0.05mm.
**Key Step 3: Pre-Production Simulation**
Conduct trial bends using scrap materials before mass production. For example, crane hooks require crack propensity testing at 90° bends during prototyping, with dwell time adjustments (recommended 3-5 seconds) to eliminate hidden defects.
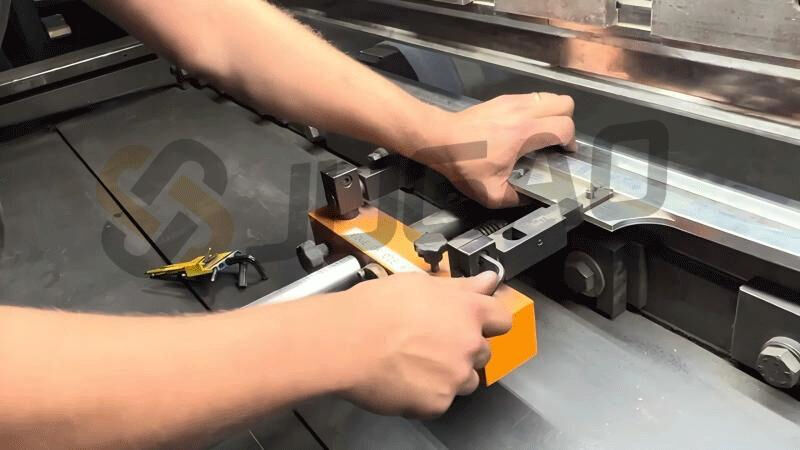
4. Long-Term Maintenance: Critical Measures for Operational Stability
- **Daily Inspections**: Monitor hydraulic oil viscosity and temperature fluctuations (ideal range: 40-60°C), replace filters promptly, and verify servo motor encoder signal stability to prevent CNC program interruptions.
- **Monthly Protocols**: Use magnetic particle inspection to detect surface micro-cracks on molds and retest hardness of high-frequency punches (≥58 HRC).
- **Fault Prediction**: If angular drift occurs during continuous operation, prioritize checks on machine guideway parallelism (tolerance ±0.01mm/m) and hydraulic cylinder synchronization accuracy.
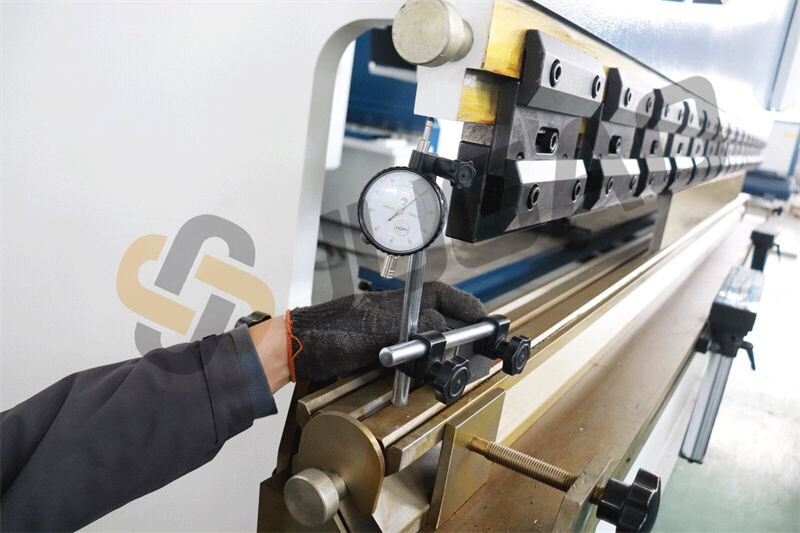
5. Industry Insights: In-Depth Analysis of High-Frequency Questions
**Q1: Recommended press brake models for elevator guide rail processing?**
We recommend CNC electro-hydraulic press brakes with dual servo drives (e.g., JUGAO 8+1 Axis CNC Hydraulic Press Brakes with DA-66T Controller), offering closed-loop control accuracy up to ±0.1° and multi-process integration to minimize repositioning errors.
**Q2: How to prevent edge cracking during stainless steel bending?**
Use annealed materials (hardness ≤HB200) with a bending radius ≥4T (T = material thickness). Apply PTFE-based lubricants to reduce friction between molds and sheets.
**Q3: How to set equipment calibration intervals?**
Perform full-parameter calibration every 200 operating hours under normal conditions. Recalibrate pressure curves when switching materials (e.g., from 6061 aluminum to S355JR steel).
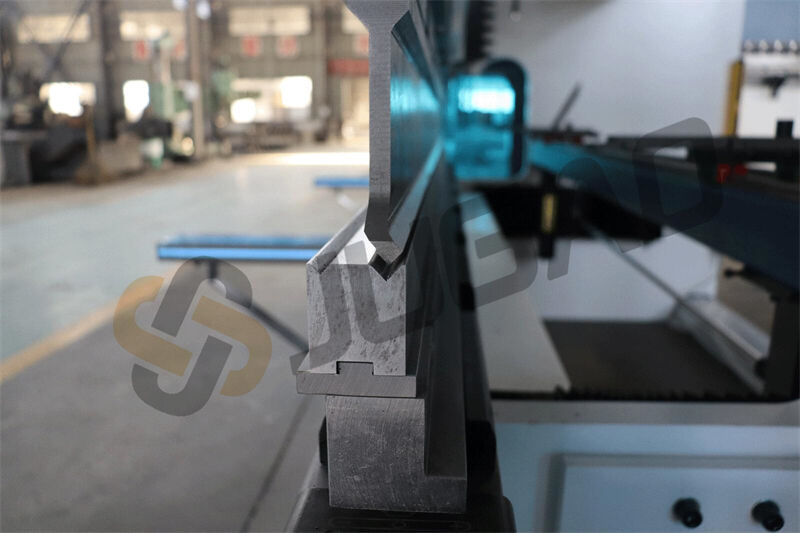
6. Technological Advancements: Innovative Pathways Toward Smart Manufacturing
With the integration of Industry 4.0 technologies, next-gen press brakes enable remote diagnostics and process optimization via IoT platforms. For example, big data-driven mold lifespan prediction systems issue replacement alerts 30 days in advance, while AR-assisted interfaces project real-time bending parameters to minimize human error.
Conclusion
As the "process heart" of elevator and crane manufacturing, press brakes directly influence industry safety and efficiency ceilings. By implementing refined parameter management, proactive maintenance strategies, and intelligent upgrades, manufacturers can achieve breakthroughs in both quality and productivity under rigorous industrial standards. For tailored solutions, JUGAO’s engineering team offers end-to-end support from equipment selection to process optimization.