Az űrművegipari gyártás átalakulása: A haladó nyomósztómű technológia átalakító hatása
Az űr- és repülőipari szektor a mérnöki pontosság csúcsában működik, ahol a mikron szintű pontosítás eldöntheti egy misszió sikert. A modern nyomósztály technológia már alapkövének vált ebben a követelményes területen, lehetővé téve gyártóknak, hogy specializált hengerekből előállítsanak azokat a bonyolult szerkezeti komponenseket, amelyek meghatározzák a modern repülőgépek tervezését. Ez a részletes elemzés megvizsgálja, hogyan járulnak hozzá a legmodernebb nyomósztály megoldások az űr- és repülőipari gyártás egyedi kihívásainak megoldásához új minőségi és hatékonysági szabványok bevezetésével.

Pontos mérnöki megoldások az űr- és repülőipar kiválóságáért
Missziókritikus repülőgépkomponensek gyártása
Az űr- és repülőipari alkalmazások nem átlagos pontosságot igényelnek a fémformálási műveletek során. A mai CNC nyomósztály rendszerek biztosítják:
Szerkezeti fuszkarétegkomponensek pontos dimenziós tűrésekkel
Pontosan alakított irányítási felületeszerelékek
Motorosztály védelmi elemek
Lejtőkar keretrendszeri elemek
Ezek a fejlett rendszerek valós idejű szög-mérési és adaptív javítási technológiákat használnak a ±0,1°-n belüli tűrhetőség fenntartására, így biztosítva a tökéletes kompatibilitást a szomszédos repülőgép-rendszerekkel.
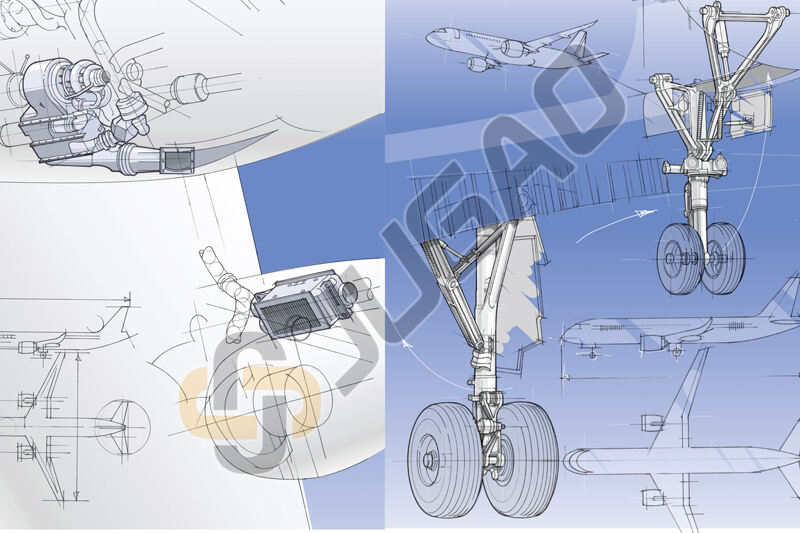
Fejlett anyagfeldolgozó képességek
A modern nyomósztály technológia fejlődött úgy, hogy repülőipari szintű anyagokat kezelhet kiváló finomsággal:
Titán-ligavak: Specializált eszközkonfigurációk megakadályozzák a tömeges törést
Alumínium összetevők: Az alkalmazkodó hajlítási sorozatok aanyag emlékezését veszik figyelembe
Magas erősségű acélok: Pontosságban ellenőrzött hidraulikus rendszerek kezelik az extrém anyagerjesztést
Ez anyagtól függő rugalmasság lehetővé teszi a gyártók számára, hogy komponenssúlyt optimalizáljanak anélkül, hogy strukturális integritást veszítenék – egy kritikus tényező a repülőipari tervezésben.
A magas súlyú termelési folyamatok optimalizálása
Az időkori nyomásfogórendszerek szignifikáns előnyöket biztosítanak az űrjárógyártás környezetében:
Automatizált eszközváltás csökkenti a beállítási időt maximum 70%-kal
Beépített látórendszerek ellenőrzik a komponens geometriáját a folyamat során
Hozzáféréses felhőmonitorozás lehetővé teszi a prediktív karbantartási ütemezést
A digitális ikrek technológiája teszi lehetővé a folyamatok gyors optimalizálását
Ezek a képességek különösen értékesek a bonyolult szárny- és hajtómű-szerkezetek gyártásakor, ahol a konvencionális gyártási módszerek túl időigényesek lennének.
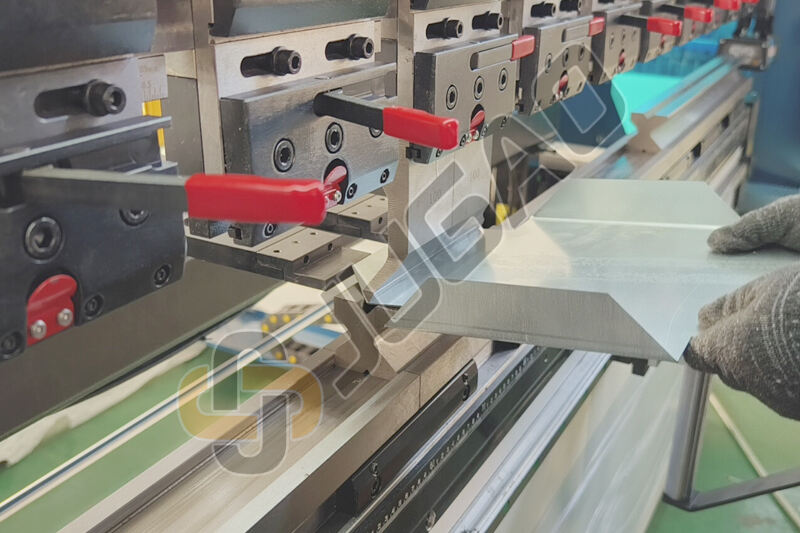
Nyomósztály műveleteinek optimalizálása repülőipari szabványok szerint
Stratégiailag kidolgozott gépkonfigurációs protokollok
A nyomósztály optimális teljesítménye eléréséhez szigorú figyelmet kell fordítani a beállítási eljárásokra:
1. Munkaterület készítése
- Rezgés-dúsított alap telepítése
- Klima-ellenőrzött környezet fenntartása
Ergonomikus operátorpozíciók figyelembevételének szempontjai
2. Pontos eszközökhöz kapcsolódó konfiguráció
-Anyagspecifikus meghajtó kiválasztási protokollok
-Lézereszközsel ellenőrzött eszköz igazítási eljárások
-Dinamikus nyomáseloszlás optimalizálása
3. Kalibrációs Kiválóság
-Többi tengelyű háttér-igazító tanúsítvány
-Valós idejű szögfigyelés implementálása
-Automatikus kompensáció hőszélességért
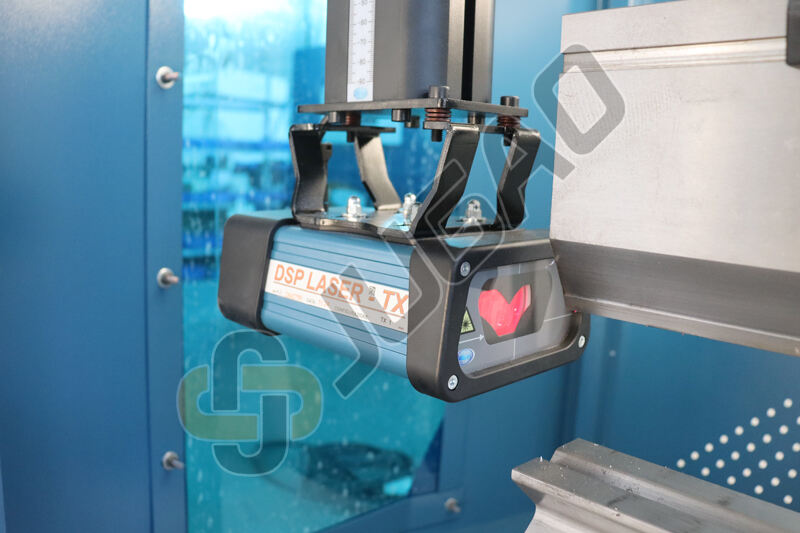
Komplex karbantartás maximális teljesítmény érdekében
Repülészeti karbantartási protokollok tartalmazzák:
Előventes Karbantartási Terv
-250 órás köztes ellenőrzéseket
-500 órás összetett szervízintervallum
-1000 órás teljes rendszer újrakalibrálás
Haladó diagnosztikai eljárások
-Hidraulikus folyadék spektrométeres elemzése
-Szervomotor teljesítmény benchmarking
-Strukturális türelmi tesztelés
Folyamatos Fejlesztési Gyakorlatok
-Szoftver verzióközeli felügyelet
-Frissítési lehetőség értékelése
-Művelettörők képességfejlesztési programok
Szakértői megoldások repülőgépipari gyártási kihívásokra
K: Milyen minőségbiztosítási intézkedések garantálják a nyomósztály pontosságát az űr- és repülőgépipari alkalmazásokban?
V: Régióként kombinált laservas kalibrációs, folyamatbeli CMM ellenőrzési és statisztikai folyamatvezérlési módszereket kell alkalmazni.
K: Hogyan oldja meg a modern nyomósztály technológia a titánium egyedi alakítási kihívásait?
V: A fejlett rendszerek hőmérséklet-ellenőrzött eszközöket, terhelésarány-ellenőrzött ívhajtást és utóbbi alakítási stresszlevonó protokollokat használnak a anyag tulajdonságainak fenntartására.
K: Milyen karbantartási gyakoriságot javasolnak a nagy térfogatú repülőipari termeléshez?
A: Intenzív műveletek 200 órás ellenőrzési ciklusokat igényelnek, különös figyelmet fordítva a hidraulikai rendszer integritására és az útvonalak auszalási mintáira.
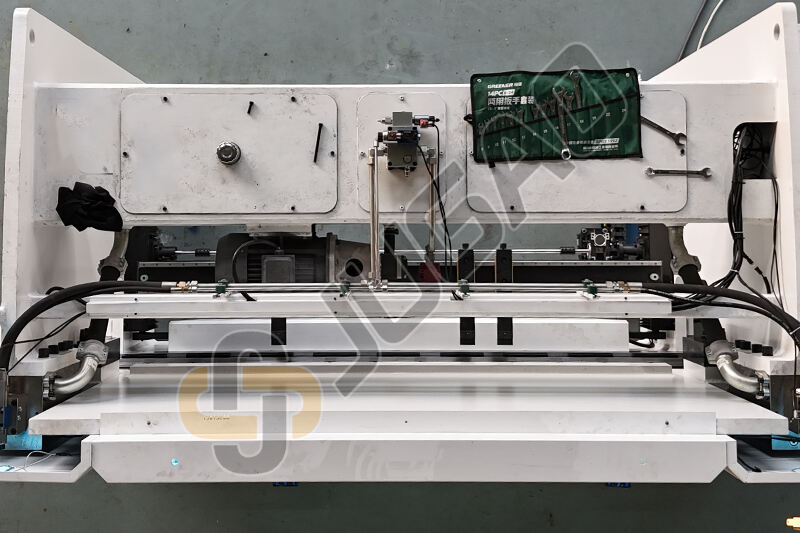
A repülőipari gyártás határértékeinek túlmutatója
A repülőipar végzetlen teljesítménynemesség után való törekvése folyamatosan ösztönzi a nyomósztóm innovációit. Az új technológiák, például:
MI-ralapú adaptív alakítási algoritmusok
Hibrid additív/szubtraktiv gyártási integráció
Nanokövisegtől kompatibilis eszközrendszer
pozicionálják a nyomósztó technológiát új generációú repülőgép-fejlesztés kulcseszközének. A gépzési képességeik fejlesztésére készen lévő gyártók számára az iparág egyedi követelményeit értő technológiai vezetőkkel való együttműködés biztosíthatja a mai piac versenyelőnyét.
A vezető berendezés-szolgáltatók mostantól teljes körű repülőipari megoldás-csomagokat ajánlanak, beleértve:
Anyagtípus-specifikus folyamatfejlesztési szolgáltatások
Szabályozási megfelelőségi dokumentációs támogatás
Kulcsfelosztási képzési és tanúsítási programok
Ezek a haladó képességek elfogadásával az űrjárógyártók elérhetik az eddig ismeretlen pontossági, hatékonysági és innovációs szinteket a fémformálási műveleteikben.