Guidelines for the Utilization of Hydraulic Oil
This article presents nine crucial tips on hydraulic oil usage, based on my years of experience. Grasping the significance of hydraulic oil and mastering its maintenance can greatly improve the efficiency and lifespan of hydraulic systems. To ensure peak performance and longevity of your hydraulic machinery,it's crucial to select the appropriate hydraulic oil and adhere to recommended maintenance practices. This includes understanding the role of hydraulic oil,its impact on system efficiency, and the importance of regular checks and timely replacements. Whether you are an experienced professional or a newcomer, these insights will guarantee optimal performance for your hydraulic system.s operate efficiently and reliably. Let's explore the essential facets of hydraulic oil that are crucial for your understanding!
Table of Contents
What are the main causes of media contamination in hydraulic transmission?
How to Control the Pollution of Working Fluid?
What are the Factors that Affect the Quality of the Working Fluid? What are the Hazards?
How can I tell if There is Water in the Hydraulic System?
What Should I do if there is Water in the Hydraulic Fluid?
Hydraulic fluid should be free from air content as it can significantly compromise the system's performance and longevity. The presence of air in hydraulic fluid can lead to increased compressibility, which may cause inaccuracies in the movement of actuators, resulting in issues such as stalling, vibration, and noise. Additionally, air bubbles can cause severe damage to hydraulic components by creating localized heat upon compression, leading to oxidation and degradation of the fluid, as well as potential corrosion of metal surfaces.
The standard for cleanliness of working fluids is a measure of the residual contaminants on the surface of components or products after cleaning. It is crucial for ensuring the longevity and reliability of products by preventing damage from particulate wear and contamination. Cleanliness standards are set based on the impact of different contaminants on product quality and the required precision of cleanliness control.
What are the various techniques for changing hydraulic oil?
What are some simple methods for assessing hydraulic oil quality and corresponding handling measures?
What are the main causes of media contamination in hydraulic transmission?
The reasons why hydraulic fluid is contaminated are complex, but broadly speaking, there are the following aspects.
1. Contamination by residues. It mainly pertains to hydraulic components, pipes, and tanks that, during the processes of manufacturing, storage, transportation, installation, and maintenance, accumulate grit, iron chips, abrasives, welding slag, rust flakes, cotton, dust, etc. Despite cleaning efforts, these surface residues remain and contaminate the hydraulic fluid.
2. Contamination by intruders. Pollutants in the hydraulic transmission device's work environment, including air, dust, and water droplets, can enter the system through various potential intrusion points, like exposed piston rods, tank ventilation holes, and oil injection holes, thereby contaminating the hydraulic fluid.
3. The generation of pollution. Mainly refers to the hydraulic transmission system in the work process generated by metal particles, seal material wear particles, paint stripping tablets, water, bubbles and fluid degradation after the gel caused by hydraulic fluid pollution.
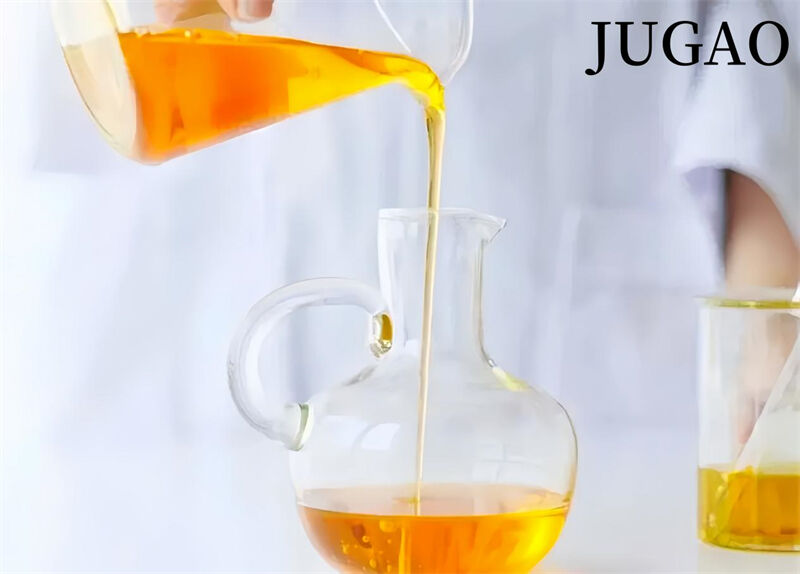
How to Control the Pollution of Working Fluid?
1. Prevent and reduce external pollution. Hydraulic transmission system before and after assembly must be strictly cleaned. In the filling and discharge of hydraulic oil and the process of disassembly of the hydraulic system, should keep the container, funnel. Pipe fittings, interfaces, etc. clean. Prevent contaminants from entering.
2. Filtration. Filter out impurities generated by the system. The finer the filtration, the better the cleanliness level of the fluid and the longer the service life of the components. The appropriate part of the system should be installed in the appropriate precision filter, well and to regularly check, clean or replace the filter element.
3. Control the working temperature of the hydraulic fluid. The high working temperature of hydraulic fluid will accelerate its oxidation and deterioration, produce various substances and shorten its service life, so the maximum operating temperature of the fluid should be limited. The ideal temperature required for hydraulic systems is 15~55℃, and generally cannot exceed 60℃.
4. Regularly check and replace the hydraulic fluid. The hydraulic fluid should be regularly checked and replaced according to the requirements of the operating instructions of the hydraulic equipment and the relevant provisions of the maintenance regulations. When replacing the hydraulic fluid, clean the tank,flush the system piping and hydraulic components.
5. Waterproof and drainage. The oil tank, oil circuit, cooler pipeline, oil storage container, etc. should be well sealed and not leaking. The bottom of the oil tank should be equipped with a drainage valve. Hydraulic oil polluted by water appears milky white, and measures should be taken to separate the water.
6. Prevent air from entering. Reasonably use the exhaust valve to ensure that the hydraulic system, especially the hydraulic pump suction pipe, is completely sealed. The system return oil should try to return from the hydraulic pump suction port, so as to provide sufficient time for the discharge of air in the oil. The return oil port should be Diagonal cut diagonal cut and extended below the oil surface of the oil tank to reduce the impact of liquid flow.
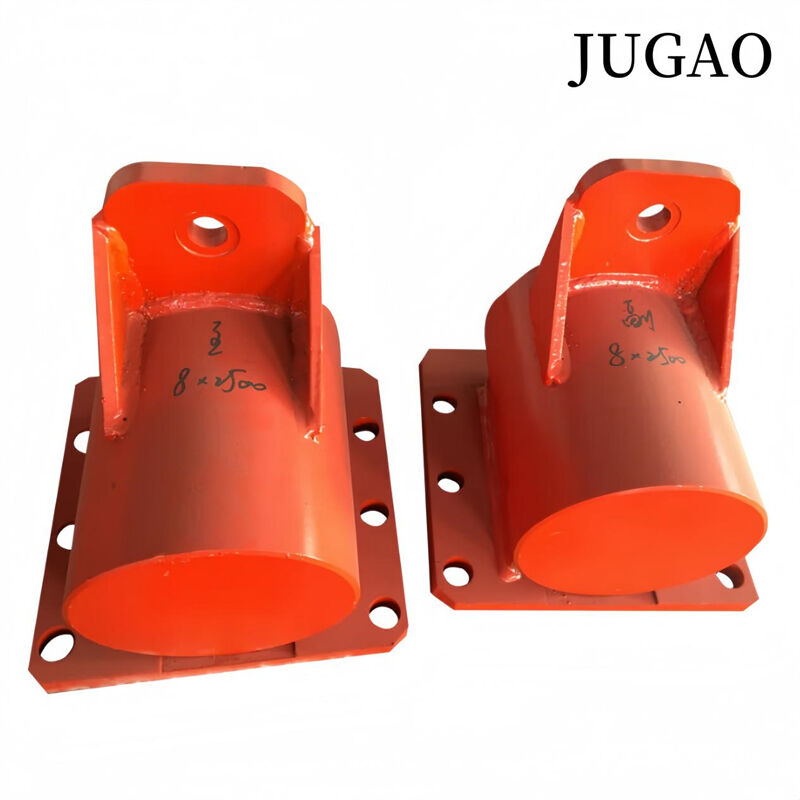
What are the Factors that Affect the Quality of the Working Fluid? What are the Hazards?
1. Impurities. Impurities include dust, abrasives, burrs, rust, varnish, welding slag, flocculent material, etc.. Impurities can not only wear the moving parts, and once stuck in the spool or other moving parts, will affect the normal operation of the entire system, resulting in machine failure, accelerating component wear and tear, so that the system performance decreases, generating noise.
2. Water. The water content in the oil refers to the technical standards of GB/T1118. 1-1994, if the water in the oil exceeds the standard, it must be replaced: otherwise, not only will damage the bearings, but also make the surface of the steel parts rust, which in turn will emulsify the hydraulic oil, deteriorate and generate precipitates, prevent the cooler from conducting heat, affect the work of the valve, reduce the effective working area of the oil filter, and increase the abrasion of the oil The effect.
3. Air. If gas is present in the hydraulic oil circuit, the overflow of bubbles will cause impacts on the pipe wall and components, leading to cavitation and subsequently preventing the system from functioning properly. Over time, this may also result in component damage.
4. Oxidation generation. General mechanical hydraulic oil working temperature is 30 ~ 80 ℃, the life of the hydraulic oil and its working temperature is closely related. When the operating oil temperature rises above 60℃, for every subsequent increase of 8℃, the oil's service life is reduced by half; specifically, the lifespan of oil at 90℃ is roughly 10% of that at 60℃, due to oxidation.
Oxygen reacts with oil in carbon and oxygen compounds, causing the oil to undergo slow oxidation. This leads to a darkening of the oil, an increase in viscosity, and eventually, the formation of oxides that may not dissolve in the oil. These oxides settle as a brown, mucus-like layer somewhere in the system, easily blocking components in the control oil channel. Consequently, ball bearings, valve spools, hydraulic pump pistons, and other parts experience increased wear, affecting the normal operation of the entire system.
Oxidation will also produce corrosive acid. The oxidation process starts slowly and when it reaches a certain stage, the oxidation speed will suddenly accelerate and the viscosity will follow a sudden rise, resulting in a higher working oil temperature, a faster oxidation process and more accumulated deposits and acid content, which will eventually make the oil unusable.
5. Physico-chemical reactants. Physico-chemical reactants can lead to changes in the chemical properties of the oil. Solvents, surface active compounds, etc.can corrode metals and deteriorate the fluid.
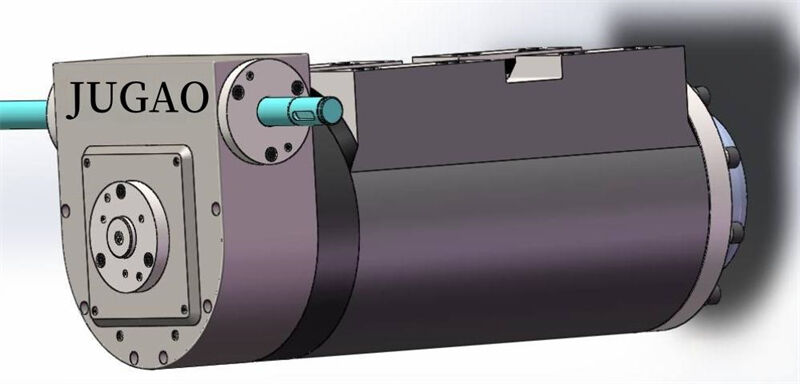
How can I tell if There is Water in the Hydraulic System?
Put 2-3ml of oil into a test tube, leave it for a few minutes so that the bubbles disappear, then heat the oil (e.g. with a lighter) and listen at the top of the test tube to see if there is a slight “bang bang” of water vapour, if there is, then the oil contains water.
Put a few drops of oil on a red-hot iron plate, and if a “snort” sound is made, it means that the oil contains water.
The water content of hydraulic oil is checked by comparing a faulty oil sample with a new one. A glass beaker filled with fresh oil is placed under light, revealing its clarity. The oil sample appears cloudy with 0.5% water content and turns milky at 1% water content. Another method involves heating a milk-like or smoky sample; if it clears after some time, the fluid likely contains water.
If the fluid contains a small amount of water (less than 0.5%), it is usually not scrapped unless the system requirements are very stringent. Water in the fluid will speed up the oxidation process and reduce lubricity. After a period of time, the water will evaporate, but the oxidation products it causes will remain in the fluid and cause further damage later.
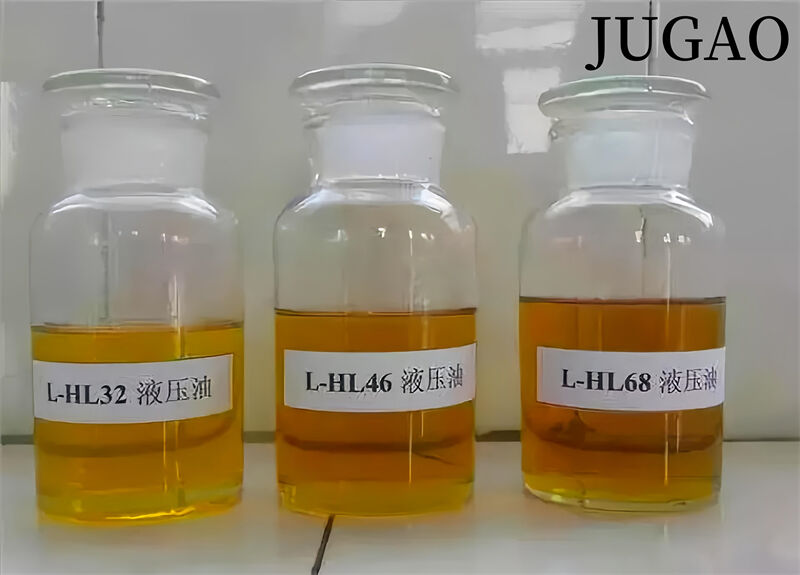
What Should I do if there is Water in the Hydraulic Fluid?
Since water is denser than oil, allowing it to stratify naturally can remove most of the water.
Stir the hydraulic oil in a pan and heat it gradually to 105°C to eliminate the residual water, ensuring no air bubbles remain in the oil. Overseas, a filter made of paper that absorbs water but not oil is used to filter out water.
If the oil contains a significant amount of water, most of it will eventually settle to the bottom. If necessary, a centrifuge is used to separate the oil from the water.
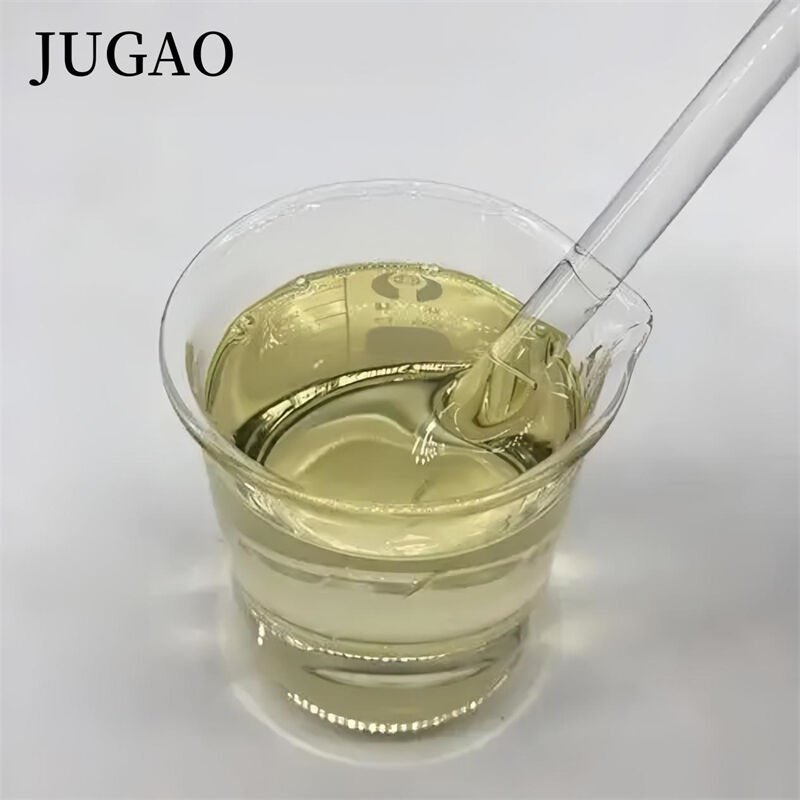
The air content in hydraulic fluid is typically expressed as a volume percentage, distinguishing between dissolved air and entrained air. Dissolved air is uniformly distributed within the fluid and does not significantly affect the fluid's bulk modulus of elasticity or viscosity. However, entrained air exists as bubbles with diameters ranging from 0.25 to 0.5mm and can greatly influence the fluid's properties. Excessive air content can lead to cavitation (the rupture of bubbles under low pressure) and the 'diesel effect' (explosive combustion of air-oil mixtures under high pressure), potentially causing material corrosion. The air separation pressure, at which air is released from the fluid, typically ranges from 100 to 6700Pa.
The volume percentage of air contained in the hydraulic medium, known as the air content, is categorized into two forms: dissolved air, which is uniformly dissolved in the medium and does not affect its volume elasticity or viscosity, and mixed air, which exists as bubbles with diameters ranging from 0.25 to 0.5mm and can significantly impact the medium's properties. Uniformly dissolved air in the hydraulic medium does not affect the bulk elastic modulus and viscosity. However, entrained air bubbles with a diameter of 0.25~0.5mm can significantly alter these properties, potentially leading to system instability and pressure fluctuations. In addition, the air content is too large, there is vapor corrosion (bubble cracking at low pressure) and the “diesel effect” (high pressure air-oil mixture explosion) risk. These phenomena will lead to material corrosion.
At high air pressure, air dissolves in the hydraulic fluid. In addition, when the pressure of the working fluid is below a certain value, the hydraulic medium will boil and produce a large amount of vapour, this pressure is called the saturation vapour pressure of the medium at this temperature. Mineral oil hydraulic fluid exhibits a saturation vapor pressure ranging from 6 to 200Pa at 20 ℃, which is similar to that of water emulsions. At the same temperature, water has a saturation vapor pressure of 2338Pa.
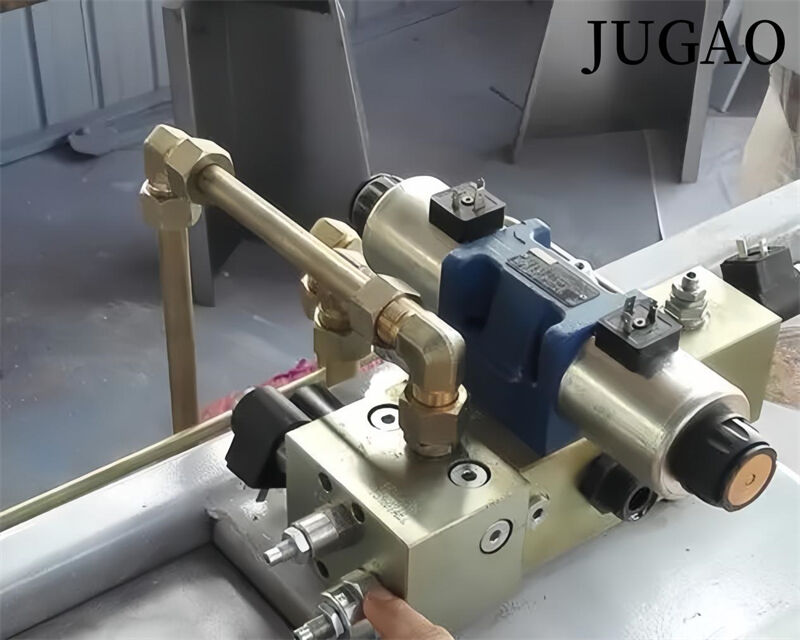
What is the standard for cleanliness of working fluids? What is the meaning?
ISO 4406, the internationally recognized standard for assessing the cleanliness of hydraulic fluids, is widely adopted by industries to ensure the proper functioning and longevity of equipment. The ISO 4406 standard specifies the contamination level of hydraulic fluids by counting particles larger than 2μm, 5μm, and 15μm in a known volume, typically 1mL or 100mL, and expressing these counts with a three-digit code (additional standards are also listed in Table 6-21). Particles larger than 2μm and 5μm are referred to as “dust” particles. The particles most likely to cause serious consequences in hydraulic systems are those larger than 15μm. The use of 5μm and 15μm is now also in accordance with ISO standards.
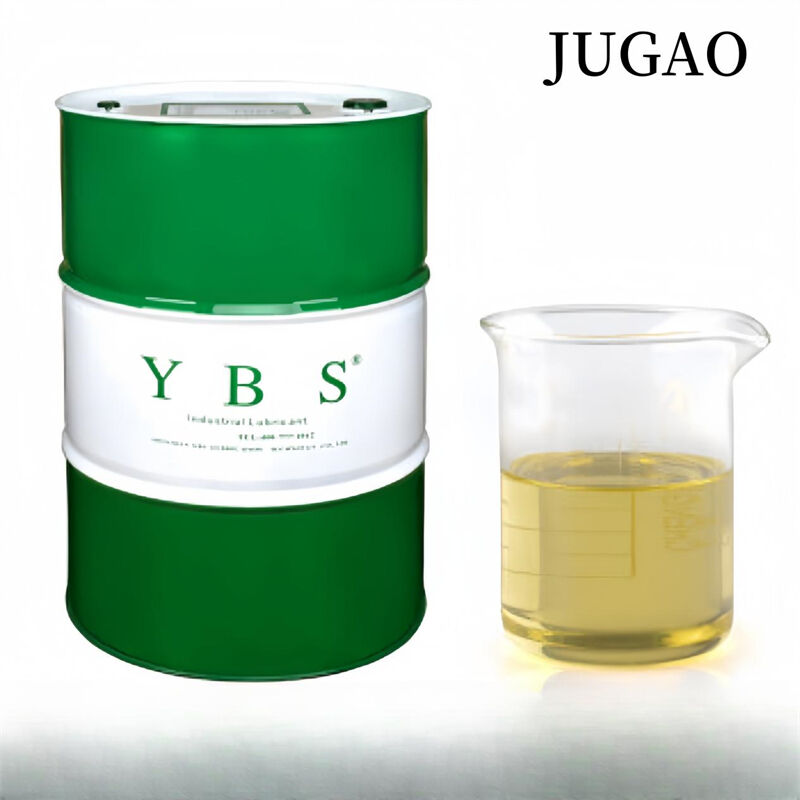
What are the Different Methods of Oil Change?
●Fixed cycle oil change. This method relies on various factors, including equipment type, working conditions, and oil products, determining the replacement of hydraulic oil after six months, a year, or between 1000 to 2000 working hours. While this method is commonly applied in practice, it lacks scientific rigor. It fails to promptly detect abnormal contamination of hydraulic oil, leading to either unnecessary changes or delays in replacement, neither of which adequately protects the hydraulic system or ensures the rational use of hydraulic oil resources.
●On-site identification method for oil change. This method involves pouring the hydraulic oil to be identified into a transparent glass container for comparison with new oil, conducting a visual inspection to determine the degree of contamination through intuitive judgment, or performing a nitric acid leaching test with pH test paper on-site to decide whether the hydraulic oil to be identified needs to be replaced.
●Comprehensive analysis of oil change. This method involves regular sampling and testing of hydraulic oil to assess its physical and chemical properties, ensuring continuous monitoring of its condition and facilitating timely oil changes based on actual usage and test results. This method, grounded in scientific principles, ensures accuracy and reliability in oil changes, aligning with established hydraulic system maintenance practices. However, it often requires a certain amount of equipment and laboratory equipment, the operation technology is complicated, the laboratory results have a certain lag, and must be handed over to the oil company for laboratory testing.
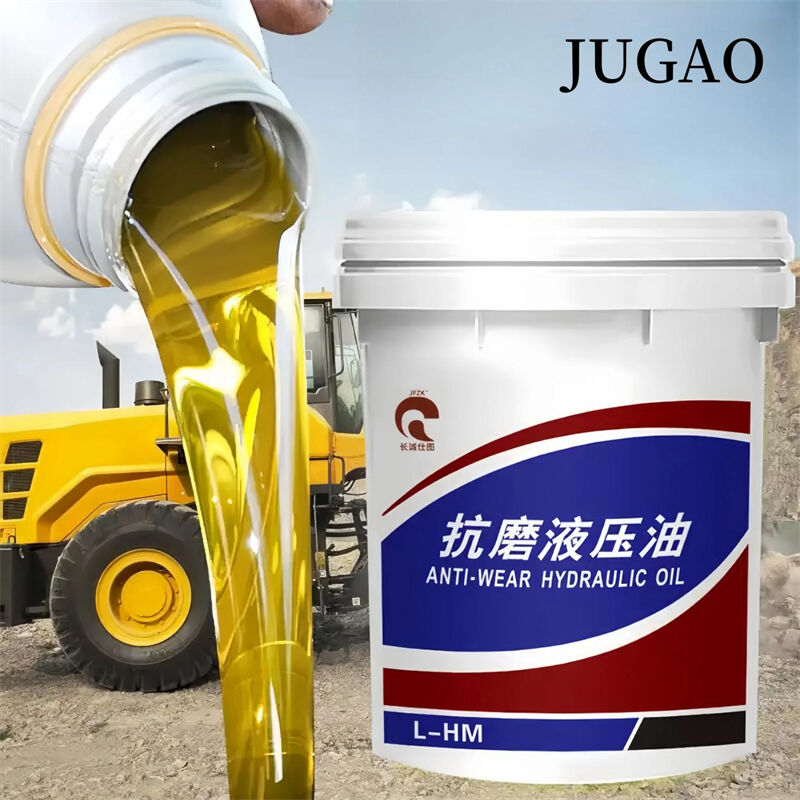
What is the Simple Practice of Judging the Quality of Hydraulic Oil and Handling Measures?
If a quality problem is found to exist that does not meet the requirements of use, the hydraulic oil must be replaced.
The following is a brief introduction to hydraulic oil quality determination methods and handling measures in four areas: inspection items, inspection methods, analysis of causes and basic countermeasures.
1. Transparent but containing small black spots, indicating debris contamination; filter the oil.
2. Appearing milky white, suggesting water contamination; separate the water from the oil.
3. A pale color may indicate mixing with foreign oil; check the viscosity and, if within acceptable limits, continue using the oil.
4. If the color darkens, becomes turbid, or contaminated, and signs of pollution or oxidation are observed, then it needs to be replaced.
5. Compare the odor with new oil; if there is a strange smell or a burnt odor, it needs to be replaced.
6. Tasting and smelling it, if there is a sour taste, it is considered normal.
7. Bubbles that appear after production, which easily disappear after shaking, are normal phenomena.
8. In terms of viscosity, it needs to be compared with new oil, taking into account temperature factors, and whether other oils have been mixed in, taking appropriate measures as needed.
9. If water is found, it needs to be separated.
10. For particulate matter, observe the results using the nitric acid immersion method and perform filtration.
11. For impurities, dilution method is used for treatment, followed by observation of results and subsequent filtration operation.
12. In the corrosion experiment section, specific corrosion methods were adopted, followed by observation of the results based on experimental requirements.
13. In pollution detection, the spot method is used for testing and the observation results are recorded based on actual conditions.
About Gary Olson
As a dedicated author and editor for JUGAO CNC, I specialize in crafting insightful and practical content specifically designed for the metalworking industry. Leveraging my years of experience in technical writing, I concentrate on delivering comprehensive articles and tutorials that empower manufacturers, engineers, and professionals to stay abreast of the latest advancements in sheet metal processing, such as CNC press brakes, hydraulic presses, shearing machines, among others.