How to calibrate the upper and lower mold centers of a press brake
Calibrating the upper and lower mold centers of a press brake is a key step to ensure bending accuracy and product quality. The following are a series of specific steps and methods for calibrating the upper and lower mold centers of a press brake:
Check mold wear
First check whether the mold is worn. If the mold is worn, it should be replaced with a new one in time, because the worn mold will cause the bending accuracy to decrease.
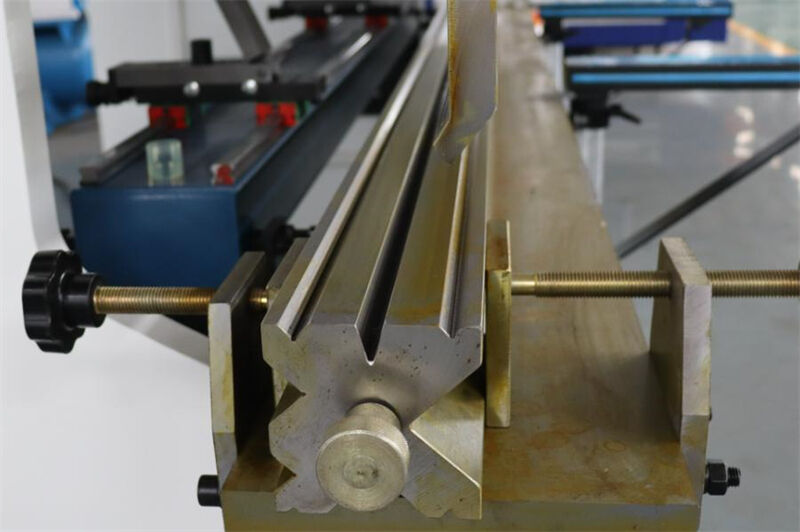
Adjust the slide stroke
According to the thickness of the folding plate and the size of the V-shaped opening of the lower die, adjust the slide stroke distance. This can be done through the button on the electrical box to control the extension length of the piston, thereby adjusting the slide stroke.
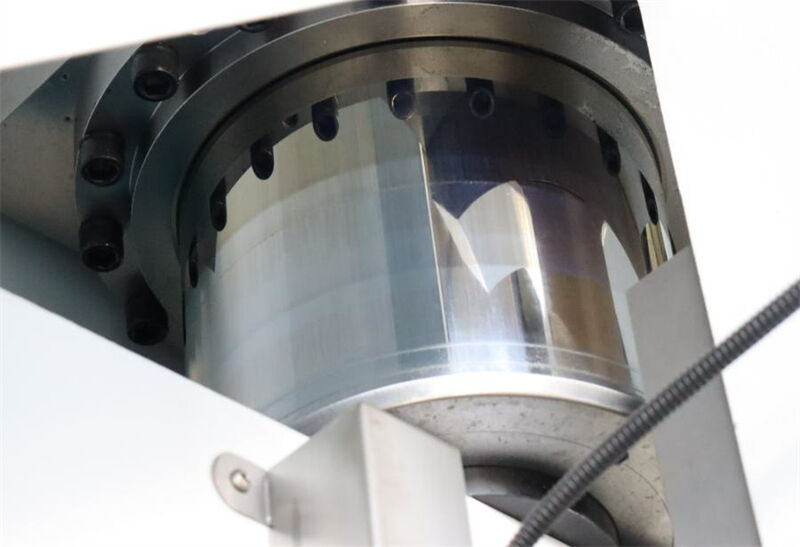
Adjust the mold gap
Measure the gap between the upper and lower molds, and adjust the gap according to the thickness of the plate being folded. A reasonable gap is crucial to ensure bending accuracy.
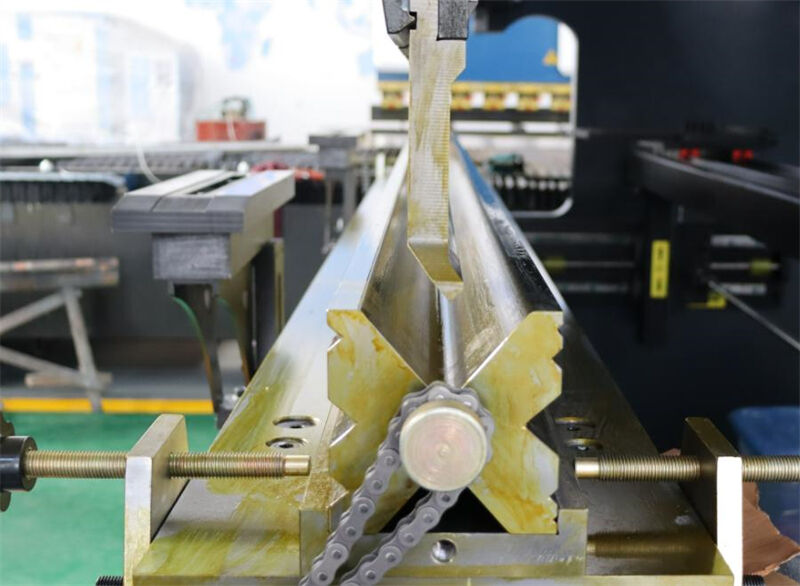
Adjust the upper limit of the slider
When the slider rises, adjust the position of the travel switch to make the slider stay at the desired position to reduce the idle distance of the slider and improve production efficiency.
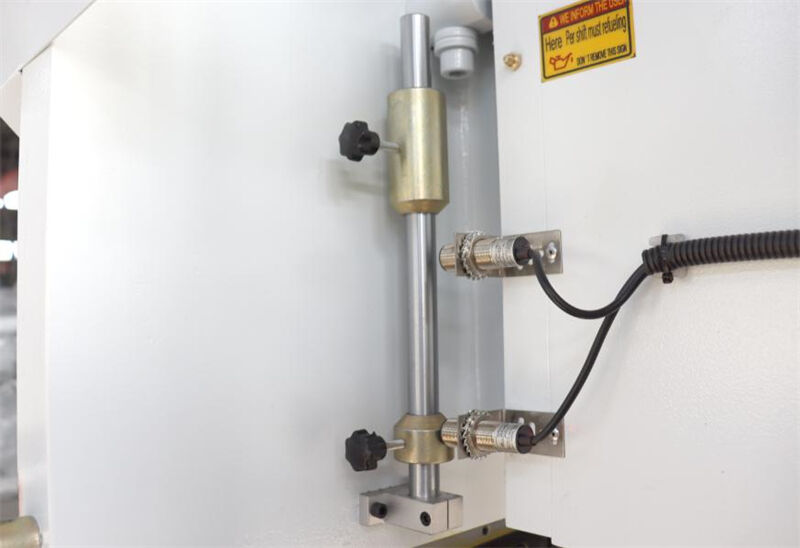
Adjust the bending angle
If it is found that the bending angles of the two ends of the workpiece are inconsistent, the angle of the workpiece can be adjusted by fine-tuning the screws of the worktable panel to make the angles basically consistent.
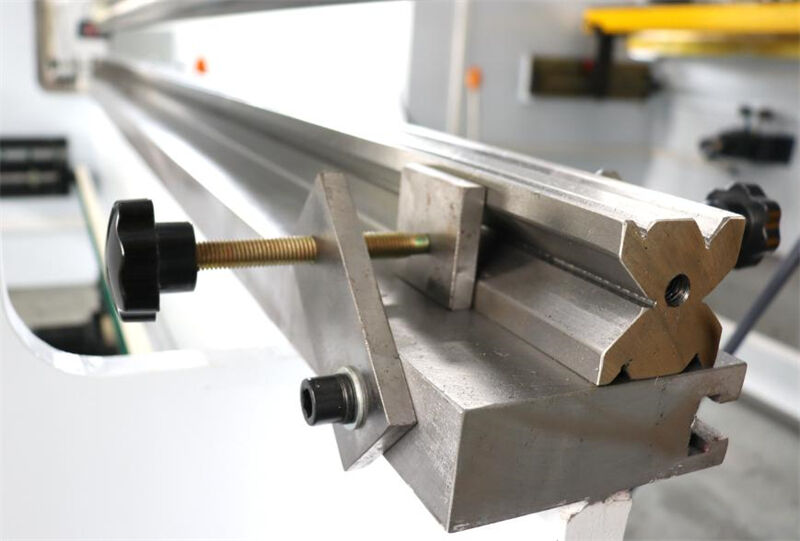