คุณค่าหลักของเครื่องดัดโลหะในอุตสาหกรรมการผลิตอุปกรณ์ลิฟท์และยก
เนื้อหา
1. การขึ้นรูปอย่างแม่นยำ: กระบวนการหลักสำหรับการสร้างพื้นฐานความปลอดภัย
2. การปฏิบัติตามข้อกำหนดทางเทคนิค: การรับรองแบบครบวงจรตั้งแต่การออกแบบไปจนถึงการผลิต
3. การผลิตที่มีประสิทธิภาพ: กลยุทธ์ในการปรับปรุงพารามิเตอร์ของเครื่องจักร
4. การบำรุงรักษาในระยะยาว: มาตรการสำคัญสำหรับเสถียรภาพของการดำเนินงาน
5. ข้อมูลเชิงลึกของอุตสาหกรรม: การวิเคราะห์อย่างลึกซึ้งเกี่ยวกับคำถามที่พบบ่อย
6. การพัฒนาเทคโนโลยี: เส้นทางนวัตกรรมสู่การผลิตอัจฉริยะ
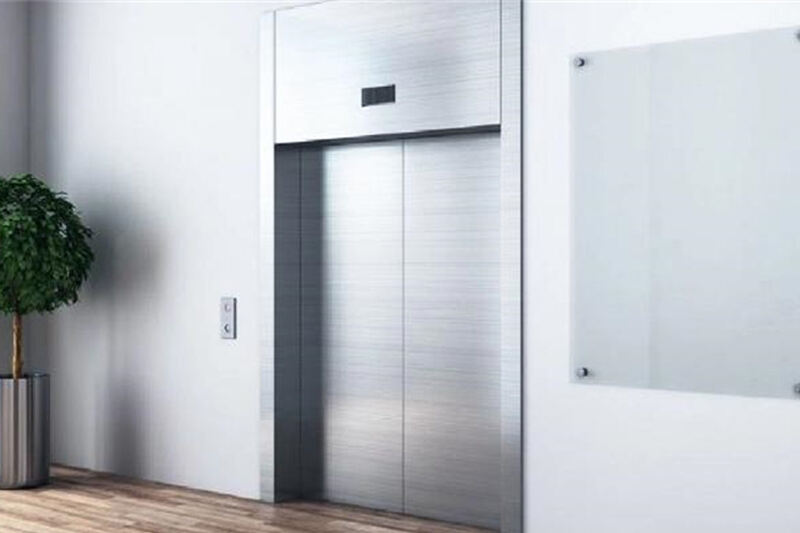
1. การขึ้นรูปอย่างแม่นยำ: กระบวนการหลักสำหรับการสร้างพื้นฐานความปลอดภัย
การทำงานของชิ้นส่วนสำคัญ เช่น ห้องโดยสารลิฟต์และเฟรมรับน้ำหนักของเครนขึ้นอยู่กับการปั้นชิ้นส่วนโลหะให้แม่นยำ เครื่องพับแผ่นโลหะด้วยแรงกดในระดับตันสูงและความแม่นยำแบบ CNC ทำให้สามารถประมวลผลโลหะอัลลอยที่มีความแข็งแรงสูง (เช่น เหล็กทนการสึกหรอ อัลูมิเนียมเกรดสำหรับอุตสาหกรรมการบิน) ให้กลายเป็นรูปร่างที่ซับซ้อน เช่น หน้าตัดโค้งของรางนำทางลิฟต์ หรือโครงสร้างเสริมความแข็งแรงของแขนเครน โดยผ่านการกำหนดรูปแบบแม่พิมพ์หลายแกน เครื่องเหล่านี้สามารถพับมุมที่คมได้ด้วยรัศมีเล็กถึง 2 มม. เพื่อตอบสนองความต้องการของพื้นที่จำกัด ในขณะเดียวกันยังคงโครงสร้างตาข่ายของวัสดุไม่ให้เสียหาย เพื่อป้องกันจุดรวมของแรงดึงและรอยแตกที่อาจเกิดขึ้น
ในสถานการณ์ที่ปรับแต่งได้ เครื่องพับโลหะสามารถรวมโมดูลงอท่อหมุนหรือแม่พิมพ์แบบแบ่งส่วนเพื่อแก้ไขปัญหาในการผลิตชิ้นส่วนที่ไม่สมมาตร เช่น กลไกเชื่อมต่อประตูลิฟต์ ตัวอย่างเช่น แผงประตูลิฟต์ต้องการกระบวนการงอแบบค่อยเป็นค่อยไปเพื่อสร้างโครงสร้างร่องลึกต่อเนื่องสำหรับการต้านทานการเสียรูปที่ดีขึ้น ในขณะที่ชุดตะกร้าลิฟต์เครนต้องใช้เทคนิคการงอแบบขั้นบันไดเพื่อให้การกระจายโหลดสมดุล
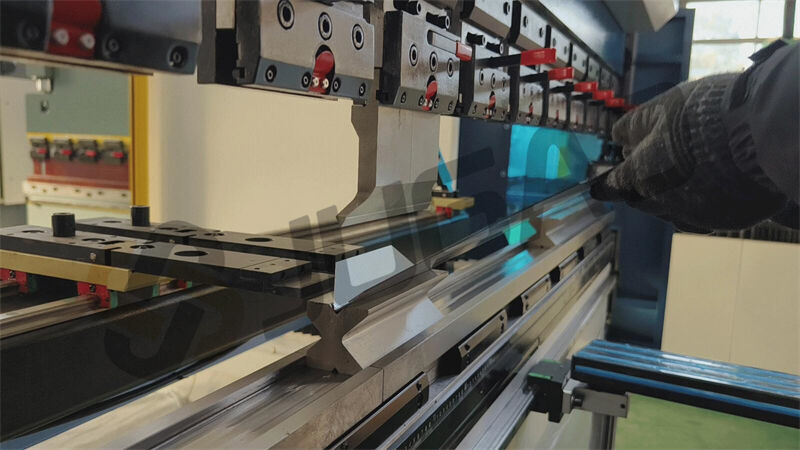
2. การปฏิบัติตามข้อกำหนดทางเทคนิค: การรับรองแบบครบวงจรตั้งแต่การออกแบบไปจนถึงการผลิต
มาตรฐานความปลอดภัยระดับโลก (เช่น EN 81, ISO 4306) กำหนดข้อกำหนดความอดทนอย่างเข้มงวดสำหรับชิ้นส่วนที่รองรับน้ำหนัก ตัวอย่างเช่น การเบี่ยงเบนของมุมงอของรางนำทางลิฟต์จะต้องควบคุมไว้ในช่วง ±0.3° เครื่องพับโลหะด้วยระบบ CNC ใช้ระบบตรวจสอบด้วยเลเซอร์แบบเรียลไทม์เพื่อแก้ไขพารามิเตอร์การผลิต และทำงานร่วมกับระบบชดเชยระยะวัดอัตโนมัติเพื่อกำจัดข้อผิดพลาดจากการดำเนินงานด้วยมือ นอกจากนี้ เครื่องเหล่านี้ยังมีฐานข้อมูลกระบวนการในตัวที่สามารถเรียกโปรแกรมที่ตั้งไว้ล่วงหน้าได้เพียงคลิกเดียว ซึ่งช่วยให้มั่นใจถึงสมรรถนะกลไกที่คงที่สำหรับชิ้นส่วนที่ผลิตจำนวนมากตามข้อกำหนดการออกแบบ
สำหรับการลดความเสี่ยง อัลกอริธึม AI ที่ฝังอยู่ในเครื่องพับโลหะสามารถทำนายการยืดตัวกลับของวัสดุและปรับความลึกของแรมอัตโนมัติ ตัวอย่างเช่น เมื่อทำการประมวลผลบล็อกน้ำหนักต้านของเครนจาก AR500 สตีล ระบบจะปรับเปลี่ยนเส้นโค้งของการงอตามลักษณะความแข็งของวัสดุ เพื่อป้องกันการไม่ตรงกันในการประกอบที่เกิดจากแรงยืดตัวกลับ
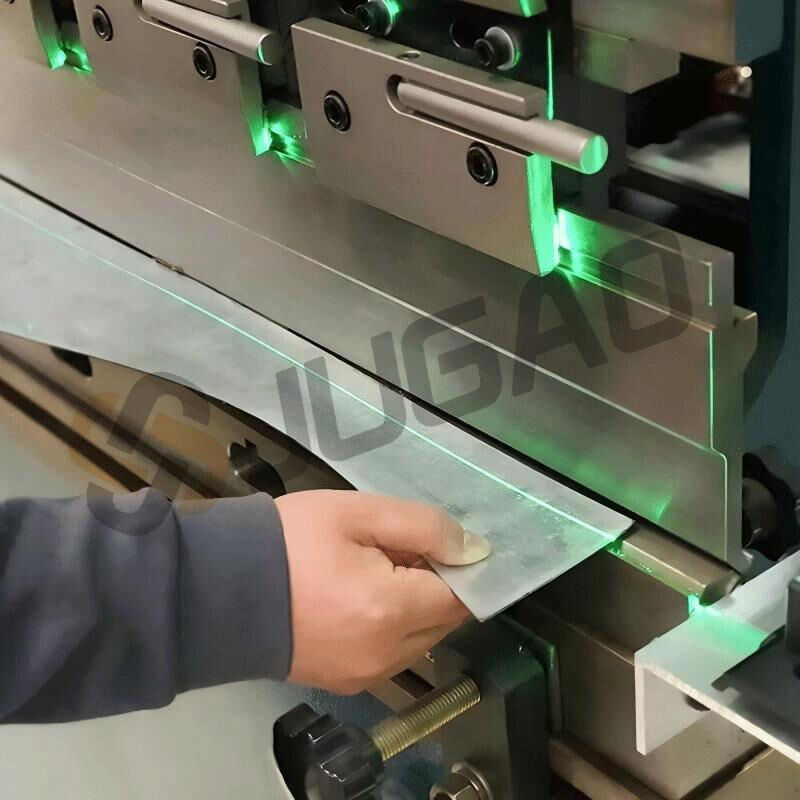
3. การผลิตที่มีประสิทธิภาพ: กลยุทธ์ในการปรับปรุงพารามิเตอร์ของเครื่องจักร
**ขั้นตอนสำคัญที่ 1: การเลือกแม่พิมพ์ที่แม่นยำ**
เลือกแม่พิมพ์ตามคุณสมบัติของวัสดุและเป้าหมายการขึ้นรูป แนะนำให้ใช้แม่พิมพ์ V-dies ที่ผ่านการขัดเงาแบบกระจก (ขนาดช่องเปิด = 8×ความหนาของวัสดุ) สำหรับแผงลิฟต์สเตนเลส เพื่อลดรอยขีดข่วนบนผิว และใช้แม่พิมพ์แบบ deep-groove (ช่องเปิด ≥30mm) พร้อมโหมดแรงกดแบบค่อยเป็นค่อยไปสำหรับชิ้นส่วนอุปกรณ์ยกเครนที่หนา เพื่อป้องกันไม่ให้แม่พิมพ์เกินกำลัง
**ขั้นตอนสำคัญที่ 2: การปรับพารามิเตอร์อย่างชาญฉลาด**
บรรลุการวางตำแหน่ง backgauge ระดับย่อยกว่าหนึ่งมิลลิเมตรผ่านระบบ CNC โดยได้รับการตรวจสอบจากเลเซอร์อินเตอร์เฟอโรมิเตอร์ สำหรับชิ้นส่วนที่ต้องการความเที่ยงตรงในระดับจุลภาค เช่น กรอบประตูลิฟต์ กลไกการตอบสนองแบบ closed-loop feedback จะช่วยให้มั่นใจว่า backgauge offset ≤0.05mm
**ขั้นตอนสำคัญที่ 3: การจำลองก่อนการผลิต**
ทำการทดลองขึ้นรูปโดยใช้วัสดุเศษก่อนการผลิตจำนวนมาก เช่น ตะขอเครนต้องทดสอบความเสี่ยงต่อการแตกระหว่างการสร้างต้นแบบที่มุม 90° โดยปรับเวลาหยุด (แนะนำ 3-5 วินาที) เพื่อกำจัดข้อบกพร่องที่ซ่อนอยู่
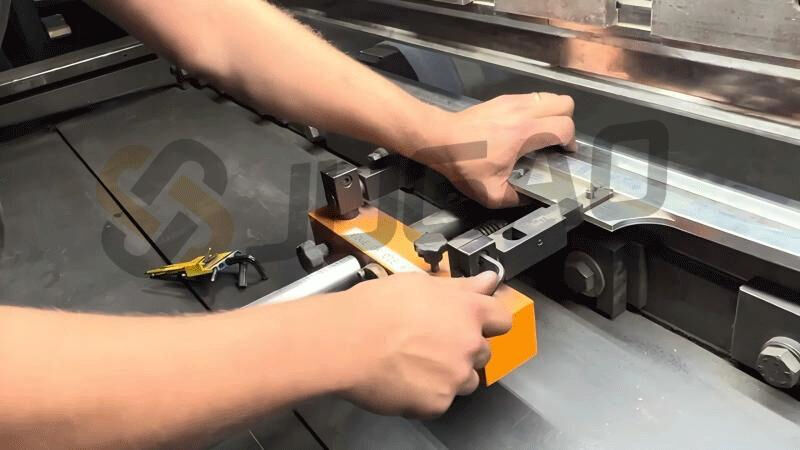
4. การบำรุงรักษาในระยะยาว: มาตรการสำคัญสำหรับเสถียรภาพของการดำเนินงาน
- **การตรวจสอบประจำวัน**: ติดตามความหนืดและความผันผวนของอุณหภูมิน้ำมันไฮดรอลิก (ช่วงที่เหมาะสม: 40-60°C) เปลี่ยนไส้กรองทันที และตรวจสอบความเสถียรของสัญญาณเอนโคเดอร์มอเตอร์เซอร์โว เพื่อป้องกันการหยุดทำงานของโปรแกรม CNC
- **โปรโตคอลรายเดือน**: ใช้วิธีการตรวจสอบอนุภาคแม่เหล็กเพื่อตรวจจับรอยแตกร้าวขนาดเล็กบนพื้นผิวของแม่พิมพ์และทดสอบความแข็งของกระบอกหมุนความถี่สูงอีกครั้ง (≥58 HRC)
- **การคาดการณ์ข้อผิดพลาด**: หากเกิดการเบี่ยงเบนของมุมในระหว่างการทำงานต่อเนื่อง ให้ตรวจสอบความขนานของทางเดินเครื่องเป็นลำดับแรก (ความอดทน ±0.01mm/ม.) และความแม่นยำของการทำงานร่วมกันของกระบอกไฮดรอลิก
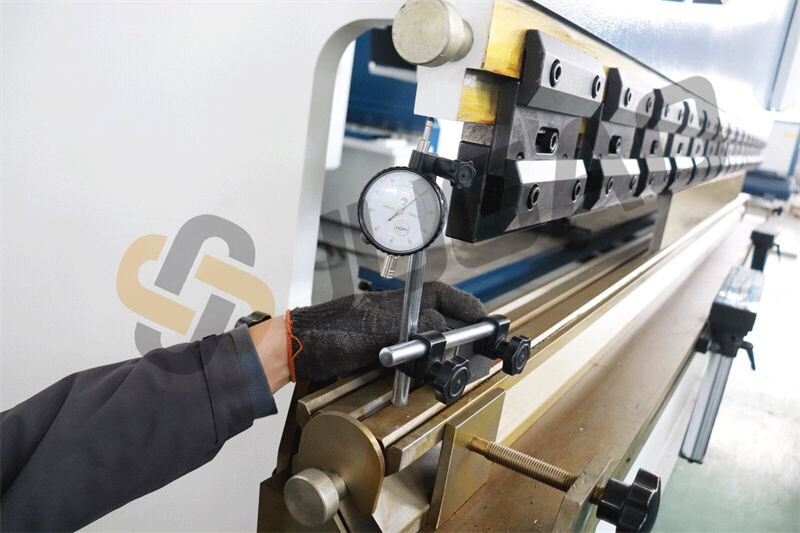
5. ข้อมูลเชิงลึกของอุตสาหกรรม: การวิเคราะห์อย่างลึกซึ้งเกี่ยวกับคำถามที่พบบ่อย
**คำถามที่ 1: เครื่องกดเบรกแบบใดที่แนะนำสำหรับการประมวลผลรางนำทางลิฟต์?**
เราแนะนำเครื่องกดเบรกไฮดรอลิกควบคุมด้วยระบบ CNC พร้อมมอเตอร์เซอร์โวดับเบิลไดรฟ์ (เช่น JUGAO 8+1 Axis CNC Hydraulic Press Brakes พร้อม DA-66T Controller) ซึ่งมีความแม่นยำในการควบคุมแบบลูปปิดสูงถึง ±0.1° และสามารถรวมกระบวนการหลายขั้นตอนเพื่อลดข้อผิดพลาดจากการปรับตำแหน่ง
**คำถามที่ 2: วิธีป้องกันไม่ให้ขอบแตกขณะงอเหล็กกล้าไร้สนิม?**
ใช้วัสดุที่ผ่านกระบวนการอบอ่อน (ความแข็ง ≤HB200) โดยมีรัศมีการงอ ≥4T (T = ความหนาของวัสดุ) ใช้สารหล่อลื่นที่มีฐานเป็น PTFE เพื่อลดแรงเสียดทานระหว่างแม่พิมพ์และแผ่นโลหะ
**คำถามที่ 3: วิธีตั้งช่วงการ较เทียบอุปกรณ์?**
ทำการ较เทียบแบบเต็มพารามิเตอร์ทุกๆ 200 ชั่วโมงในการทำงานภายใต้เงื่อนไขปกติ ตรวจสอบเส้นโค้งแรงดันใหม่เมื่อเปลี่ยนวัสดุ (เช่น จากอลูมิเนียม 6061 เป็นเหล็ก S355JR)
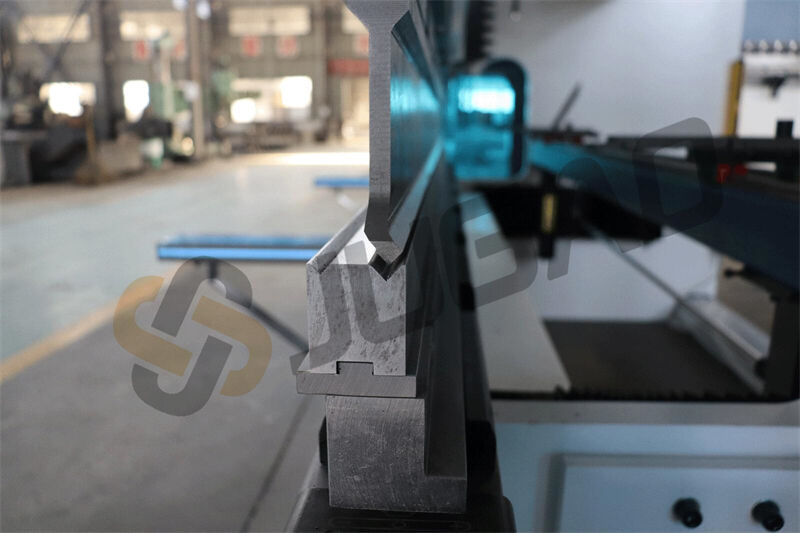
6. การพัฒนาเทคโนโลยี: เส้นทางนวัตกรรมสู่การผลิตอัจฉริยะ
ด้วยการรวมเทคโนโลยีอุตสาหกรรม 4.0 เครื่องกดขึ้นรูปรุ่นถัดไปสามารถวินิจฉัยจากระยะไกลและปรับแต่งกระบวนการผ่านแพลตฟอร์ม IoT ได้ เช่น ระบบทำนายอายุการใช้งานแม่พิมพ์ที่ขับเคลื่อนโดยข้อมูลขนาดใหญ่จะแจ้งเตือนการเปลี่ยนภายใน 30 วันล่วงหน้า ในขณะที่อินเทอร์เฟซที่ช่วยด้วย AR จะแสดงพารามิเตอร์การงอแบบเรียลไทม์เพื่อลดข้อผิดพลาดของมนุษย์
สรุป
ในฐานะ "หัวใจของกระบวนการ" ในการผลิตลิฟท์และเครน เครื่องกดงอมีอิทธิพลโดยตรงต่อความปลอดภัยและความสามารถสูงสุดของอุตสาหกรรม โดยการนำเอาการจัดการพารามิเตอร์ที่ละเอียดอ่อน การบำรุงรักษาเชิงรุก และการอัปเกรดแบบอัจฉริยะ มาใช้ ผู้ผลิตสามารถบรรลุความก้าวหน้าในด้านคุณภาพและความสามารถในการผลิตภายใต้มาตรฐานอุตสาหกรรมที่เข้มงวดได้ สำหรับโซลูชันที่ออกแบบเฉพาะ JUGAO ทีมวิศวกรของเราให้การสนับสนุนแบบครบวงจรตั้งแต่การเลือกอุปกรณ์จนถึงการปรับปรุงกระบวนการ