Nilai Inti dari Mesin Press Brake dalam Pembuatan Peralatan Elevator dan Pengangkatan
Konten
1. Pembentukan Presisi: Proses Inti untuk Membangun Fondasi Keselamatan
2. Kepatuhan Teknis: Jaminan Siklus Penuh dari Desain hingga Produksi
3. Produksi Efisien: Strategi untuk Optimasi Parameter Peralatan
4. Pemeliharaan Jangka Panjang: Langkah-Langkah Kritis untuk Stabilitas Operasional
5. Wawasan Industri: Analisis Mendalam tentang Pertanyaan Berfrekuensi Tinggi
6. Perkembangan Teknologi: Jalur Inovatif Menuju Manufaktur Cerdas
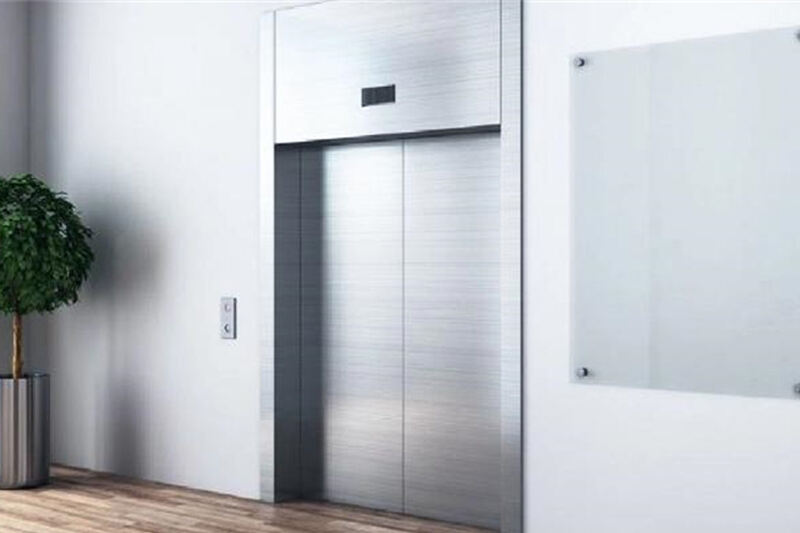
1. Pembentukan Presisi: Proses Inti untuk Membangun Fondasi Keselamatan
Fungsionalitas komponen kritis seperti kabin lift dan rangka penopang derek bergantung pada pembentukan presisi bagian logam. Pemipih (press brakes), dengan tekanan ber-tonase tinggi dan presisi CNC, memungkinkan pengolahan paduan kuat (misalnya, baja tahan aus, aluminium kelas penerbangan) menjadi geometri kompleks, seperti penampang melengkung rel panduan lift atau rusuk penguatan untuk lengan derek. Melalui konfigurasi cetakan multi-akses, mesin-mesin ini mencapai lipatan sudut tajam dengan jari-jari sekecil 2mm, memenuhi persyaratan ruang yang kompak sambil memastikan struktur gred material tidak rusak untuk mencegah konsentrasi stres dan retakan potensial.
Dalam skenario yang disesuaikan, press brakes dapat mengintegrasikan modul penyiku pipa putar atau cetakan segmen untuk mengatasi tantangan dalam pembuatan komponen tidak beraturan, seperti mekanisme tautan pintu lift. Sebagai contoh, panel pintu lift memerlukan penyiku bertahap untuk menciptakan struktur bergelombang terus-menerus guna meningkatkan ketahanan deformasi, sementara bracket katrol crane membutuhkan teknik penyiku bertahap untuk menyeimbangkan distribusi beban.
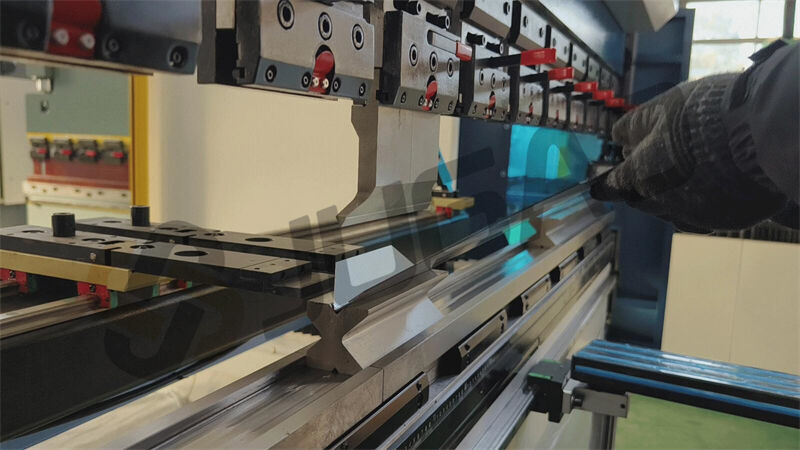
2. Kepatuhan Teknis: Jaminan Siklus Penuh dari Desain hingga Produksi
Standar keselamatan global (misalnya, EN 81, ISO 4306) menetapkan persyaratan toleransi yang ketat pada komponen penopang beban. Sebagai contoh, deviasi sudut lentur rel panduan lift harus dikendalikan dalam rentang ±0,3°. Patahan CNC menggunakan sistem pemantauan dinamis laser untuk koreksi parameter mesin secara real-time, dikombinasikan dengan kompensasi backgauge otomatis untuk menghilangkan kesalahan operasional manual. Selain itu, database proses bawaan mesin memungkinkan pengambilan ulang program yang telah disetel dengan satu klik, memastikan kinerja mekanis yang konsisten pada bagian-bagian yang diproduksi massal sesuai spesifikasi desain.
Untuk mitigasi risiko, algoritma AI yang tertanam dalam patahan memprediksi springback material dan secara otomatis menyesuaikan kedalaman ram. Misalnya, saat memproses blok konterbobot kran dari baja AR500, sistem secara dinamis memodifikasi kurva penyiku berdasarkan karakteristik kekerasan material untuk mencegah ketidakselarasan perakitan yang disebabkan oleh springback.
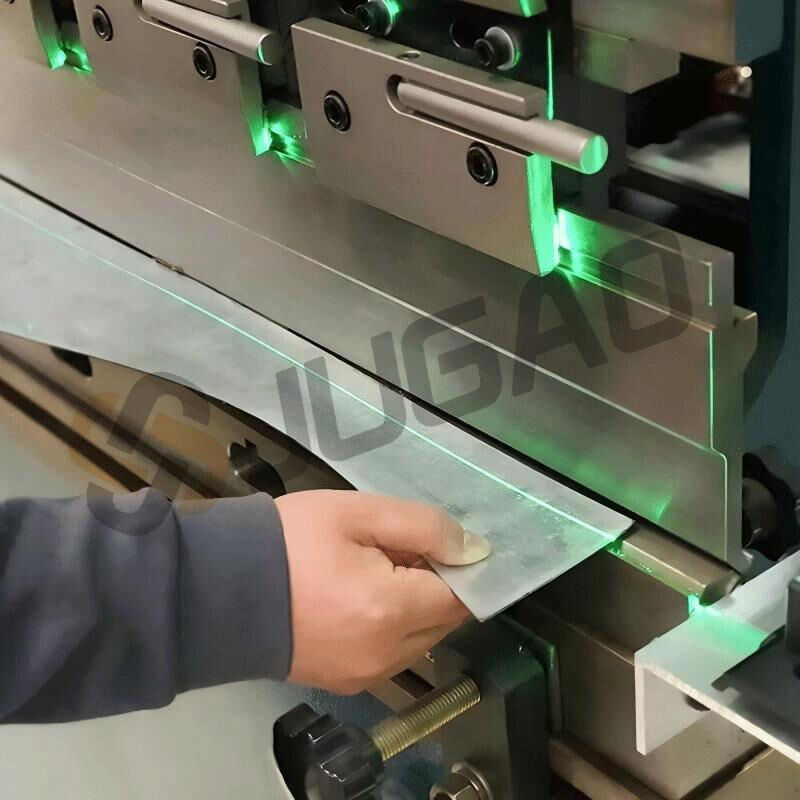
3. Produksi Efisien: Strategi untuk Optimasi Parameter Peralatan
**Langkah Kunci 1: Pemilihan Cetakan Presisi**
Pilih cetakan berdasarkan sifat material dan tujuan pemrosesan. Cetakan V dengan polesan cermin (ukuran bukaan = 8×ketebalan material) direkomendasikan untuk panel lift baja tahan karat agar meminimalkan goresan permukaan, sedangkan cetakan dengan alur dalam (bukaan ≥30mm) yang dipasangkan dengan mode tekan bertahap ideal untuk komponen engsel crane tebal guna mencegah kelebihan beban cetakan.
**Langkah Kunci 2: Kalibrasi Parameter Berbasis Kecerdasan**
Capai posisi backgauge sub-milimeter melalui sistem CNC, divalidasi oleh interferometer laser. Untuk komponen mikro-toleransi seperti bingkai pintu lift, mekanisme umpan balik loop tertutup memastikan offset backgauge ≤0,05mm.
**Langkah Kunci 3: Simulasi Pra-Pemroduksian**
Lakukan uji lipat menggunakan material limbah sebelum produksi massal. Sebagai contoh, kait crane memerlukan pengujian kecenderungan retak pada lipatan 90° selama prototipe, dengan penyesuaian waktu tahan (direkomendasikan 3-5 detik) untuk menghilangkan cacat tersembunyi.
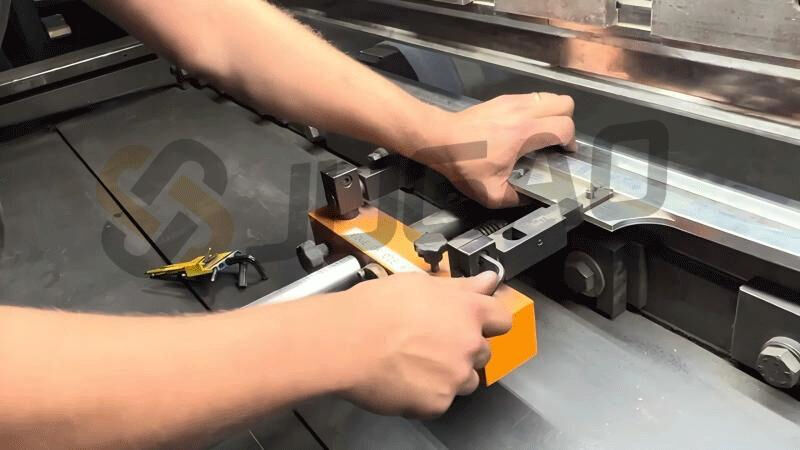
4. Pemeliharaan Jangka Panjang: Langkah-Langkah Kritis untuk Stabilitas Operasional
- **Pemeriksaan Harian**: Awasi kekentalan dan fluktuasi suhu minyak hidrolik (rentang ideal: 40-60°C), ganti filter tepat waktu, dan verifikasi stabilitas sinyal encoder motor servo untuk mencegah gangguan program CNC.
- **Protokol Bulanan**: Gunakan pemeriksaan partikel magnetik untuk mendeteksi retakan mikro permukaan pada cetakan dan uji ulang kekerasan pukulan frekuensi tinggi (≥58 HRC).
- **Prediksi Kerusakan**: Jika terjadi penyimpangan sudut selama operasi berkelanjutan, prioritaskan pemeriksaan paralelisme jalur mesin (toleransi ±0.01mm/m) dan akurasi sinkronisasi silinder hidrolik.
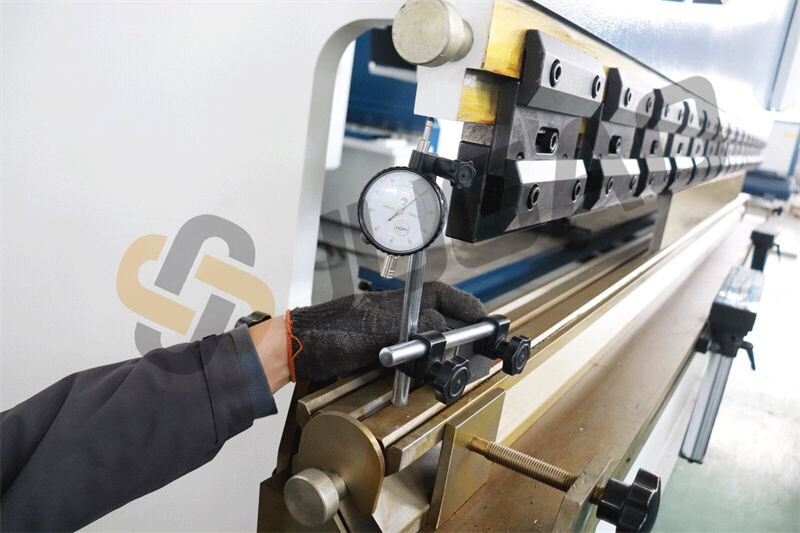
5. Wawasan Industri: Analisis Mendalam tentang Pertanyaan Berfrekuensi Tinggi
**Q1: Rekomendasi model press brake untuk pengolahan rel panduan lift?**
Kami merekomendasikan press brake hidrolik CNC dengan dua penggerak servo (misalnya, JUGAO 8+1 Axis CNC Hydraulic Press Brake dengan Pengontrol DA-66T), menawarkan akurasi kontrol loop tertutup hingga ±0.1° dan integrasi multi-proses untuk meminimalkan kesalahan reposisi.
**Q2: Bagaimana cara mencegah retak tepi selama pembengkokan stainless steel?**
Gunakan bahan yang sudah dilebur (kerasnya ≤HB200) dengan jari-jari lengkung ≥4T (T = ketebalan bahan). Gunakan pelumas berbasis PTFE untuk mengurangi gesekan antara cetakan dan lembaran.
**Q3: Bagaimana menentukan interval kalibrasi peralatan?**
Lakukan kalibrasi penuh parameter setiap 200 jam operasi dalam kondisi normal. Kalibrasi ulang kurva tekanan saat berganti bahan (misalnya, dari aluminium 6061 ke baja S355JR).
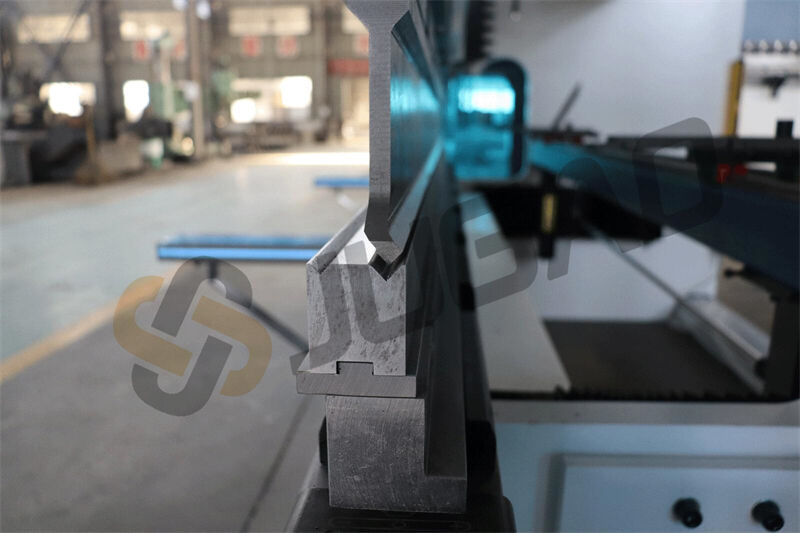
6. Perkembangan Teknologi: Jalur Inovatif Menuju Manufaktur Cerdas
Dengan integrasi teknologi Industry 4.0, pres brake generasi berikutnya memungkinkan diagnostik jarak jauh dan optimisasi proses melalui platform IoT. Sebagai contoh, sistem prediksi umur cetakan yang didorong oleh big data memberikan peringatan penggantian 30 hari sebelumnya, sementara antarmuka berbantuan AR menampilkan parameter penyiku real-time untuk meminimalkan kesalahan manusia.
Kesimpulan
Sebagai "jantung proses" dalam pembuatan lift dan derek, pres rem secara langsung memengaruhi batas keamanan dan efisiensi industri. Dengan menerapkan manajemen parameter yang cermat, strategi pemeliharaan proaktif, dan peningkatan cerdas, produsen dapat mencapai terobosan dalam kualitas dan produktivitas di bawah standar industri yang ketat. Untuk solusi yang disesuaikan, tim insinyur JUGAO menawarkan dukungan end-to-end dari pemilihan peralatan hingga optimasi proses.