بهینهسازی فرآیندهای خمش برای کیفیت بیشتر در تولید فلزی
بهینهسازی فرآیندهای خمش برای کیفیت بیشتر در تولید فلزی
جدول مطالب
1. نقش اساسی بهینهسازی فرآیند خم شدن
چرا بهینهسازی خم شدن مهم است
عوامل کلیدی مؤثر بر کیفیت خم شدن
راهنمای مراحل بهینهسازی عملیات خمش
انتخاب تجهیزات مناسب
تنظیم ابزار دقیق
آمادگی و مدیریت مواد
کالیبراسیون و تضمین کیفیت
3. حل مشکلات رایج در عملیات خمش
شناسایی عیوب خم شدگی مکرر
راهحلهای پیشگیرانه برای نتایج منظم
4. پاسخهای کاربردی به سوالات متداول دیوارک مکانیکی
بهترین روشها برای کالیبراسیون دیوارک مکانیکی
فرکانس نگهداری و تعمیرات برای عملکرد اوج
5. اندیشههای نهایی درباره دستیابی به خم شدن بدون عیب
در زمینه رقابتی ساخت فلزات، بهینهسازی فرآیندهای خمش سنگینه اصلی تحویل دادن محصولات با دقت بالا و بدون عیب است. آیا شما یک کارگاه کوچک را اداره میکنید یا یک تسهیلات تولید بزرگ مقیاس، تکمیل تکنیکهای خمش شما میتواند به طور قابل توجهی کارایی را افزایش دهد، زباله را کاهش دهد و کیفیت محصول را بالا ببرد. این راهنما به استراتژیهای عملی برای کامل کردن عملیات خمش شما میپردازد تا هر خمش به معیارهای دقیق برسد.
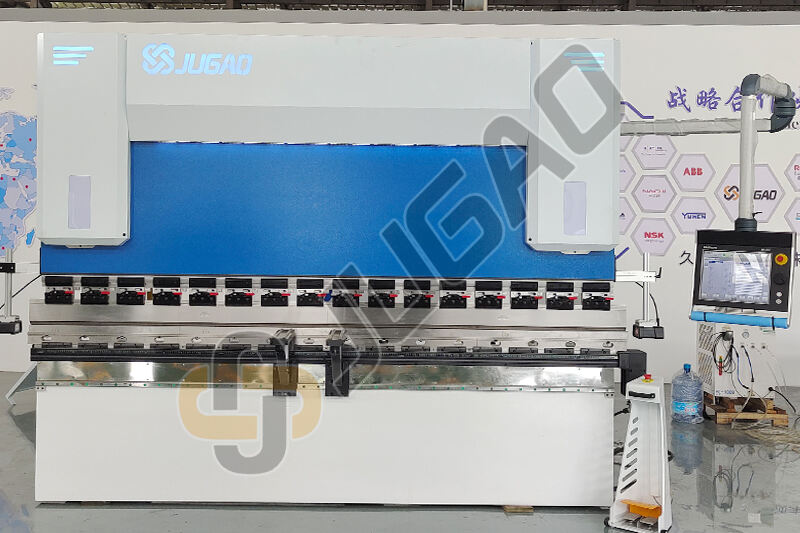
1. نقش اساسی بهینهسازی فرآیند خم شدن
چرا بهینهسازی خم شدن مهم است
دقت در خمش مستقیماً بر روی سلامت محصول، ظاهر و عملکرد تأثیر میگذارد. فرآیندهای بهینهسازی مجدد کارها را کاهش میدهد، ضایعات مواد را کم میکند و چرخههای تولید را کوتاه میکند - رانندههای کلیدی برای کارایی هزینه و رضایت مشتری.
عوامل کلیدی مؤثر بر کیفیت خم شدن
موفقیت بر سه ستون پایه تکیه دارد:
توانایی تجهیزات – هماهنگی مشخصات ماشین با نیازهای مواد.
دقت ابزار - استفاده از ماتریسها و ضربهدهندههای مناسب برای هندسه قوس.
همگن بودن مواد - تضمین یکپارچگی در خواص فلزی و حالت سطحی.
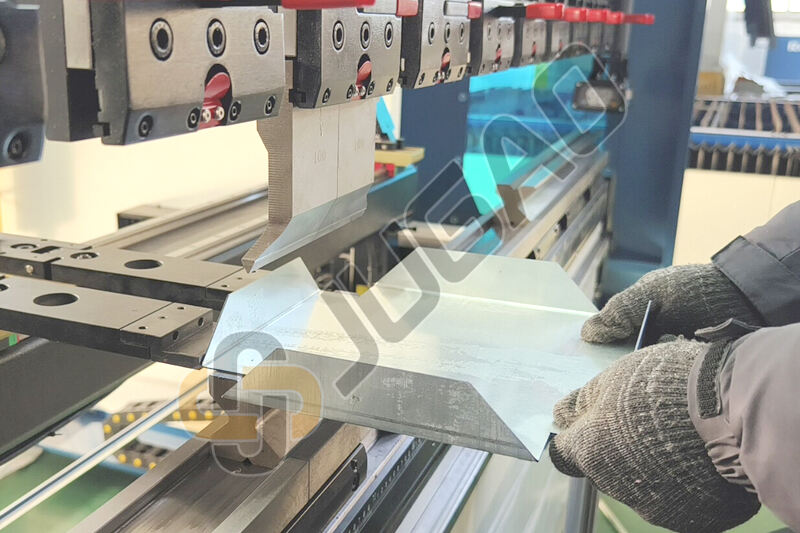
راهنمای مراحل بهینهسازی عملیات خمش
مرحله ۱: انتخاب تجهیزات مناسب
انتخاب یک ماشین فشاری بر اساس:
تنnage و طول بستر – هماهنگی با ضخامت ماده و پیچیدگی خم شدن.
سیستمهای کنترل – دستگاههای مجهز به CNC تکرارپذیری بیشتری برای طراحیهای پیچیده ارائه میدهند.
نکته حرفهای: ترمزهای هیدرولیک در خم شدن فلزات ضخیم برتری دارند، در حالی که مدلهای برقی صرفهجویی در انرژی را برای مواد نازک فراهم میکنند.
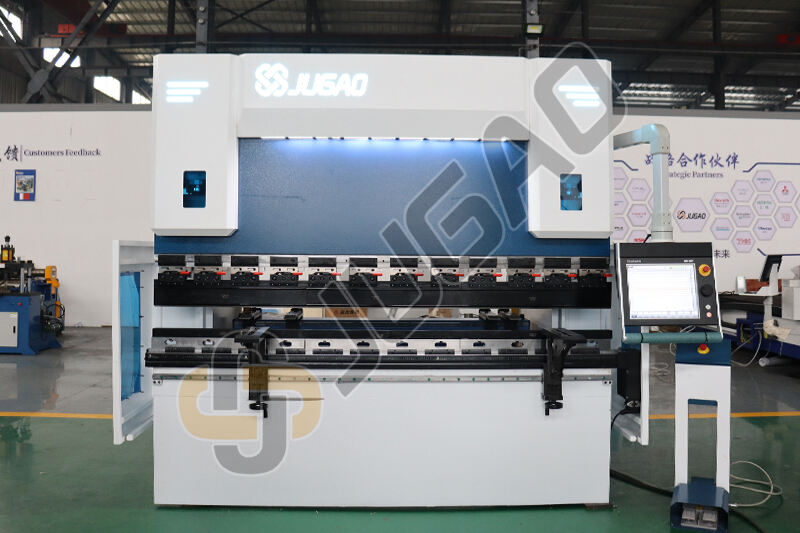
مرحله 2: تنظیم دقیق ابزارها
انتخاب دای و پانچ – به جداول سازنده مراجعه کنید تا ابزار مناسب را انتخاب کنید.
جلوگیری از بازگشت نورس – از تکنیکهای تعویض یا خمش هوایی برای فلزات انعطافپذیر استفاده کنید.
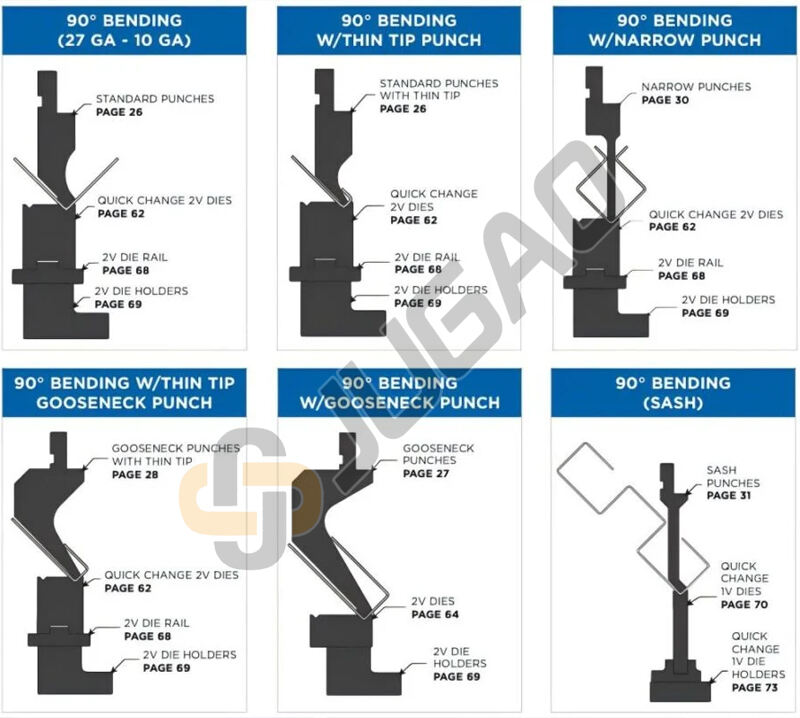
مرحله 3: آمادگی و دستیابی به مواد
آمادهسازی سطح – آلودگیها مثل روغن یا مقیاس را حذف کنید تا عیوب پیش بیاید.
نشانگذاری پیش از خم شدن – خطوط لیزر یا خط کشی دقت خم شدن را تضمین میکند.
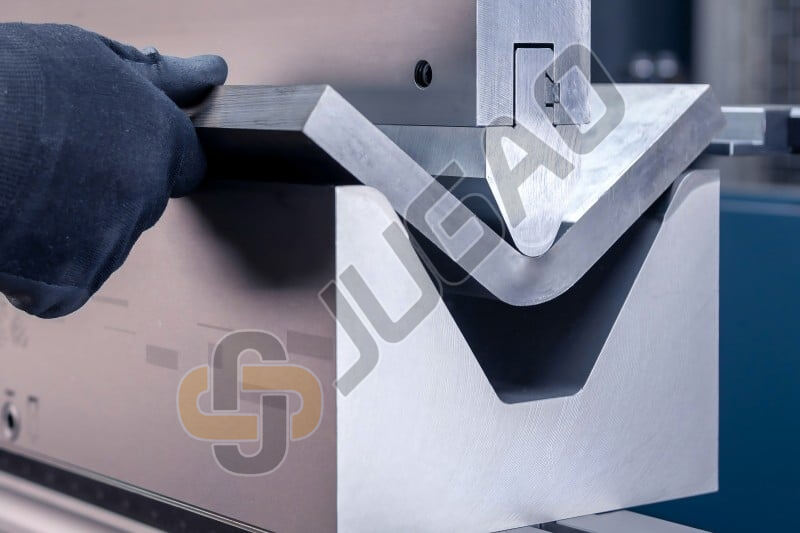
مرحله 4: کالیبراسیون و تضمین کیفیت
هماهنگی پشت آهنگرد – موقعیت را با ابزارهای اندازهگیری دیجیتال بررسی کنید.
آزمایش زنده کردن – اجرای نمونهای از تولید برای تأیید تنظیمات قبل از تولید کامل.
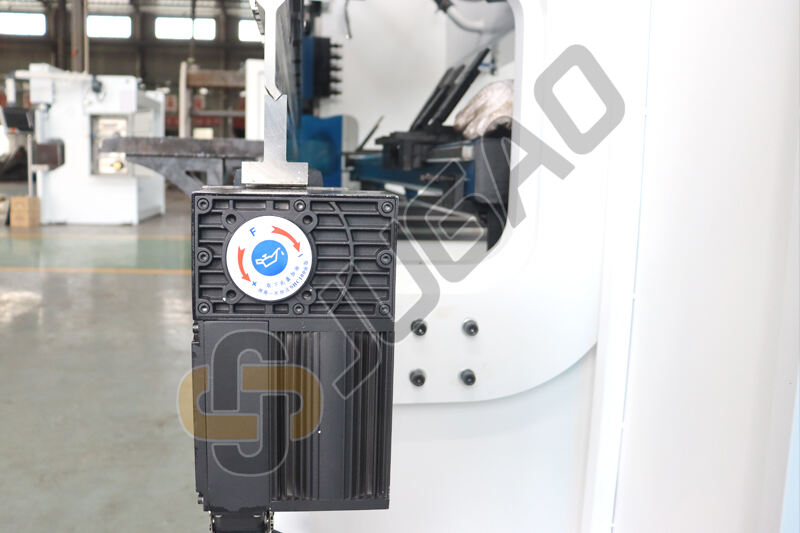
3. حل مشکلات رایج در عملیات خمش
شناسایی عیوب خم شدگی مکرر
زاویههای ناسازگار – معمولاً ناشی از سپیده شدن ابزار یا عدم هممرکزی.
چخخراش روی سطح – ناشی از ابزارهای آلوده یا دستکاری نادرست مواد.
راهحلهای پیشگیرانه برای نتایج منظم
بررسیهای مداوم ابزار – جایگزینی ماتریسهای سپیده شده به صورت فوری.
روشهای روغن کاری – کاهش اصطکاک برای افزایش عمر ابزار و بهبود پوشش.
4. پاسخهای کاربردی به سوالات متداول دیوارک مکانیکی
پ: کدام روش برای کالیبراسیون ماشین فشارگیر قابل اتکا است؟
ج: شروع با سطحبندی ماشین، سپس از یافتهی زاویه دیجیتال برای تنظیم دقیق رام و مهرهها استفاده کنید. برای عملیاتهای حجمزیاد، کالیبراسیون منظم لیزر توصیه میشود.
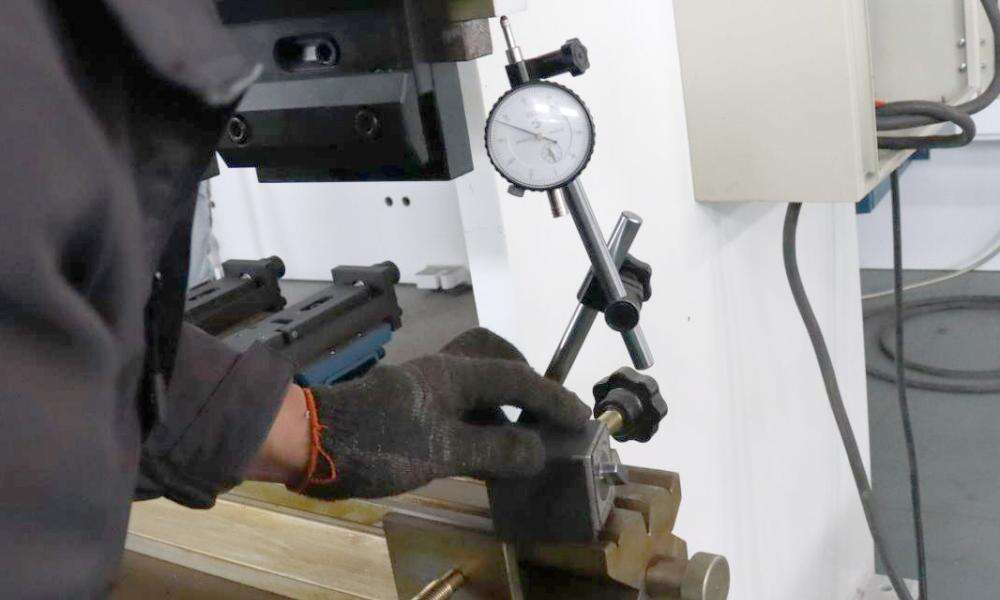
پ: نگهداری چقدر باید انجام شود؟
ج: هر ۵۰۰ ساعت کار، بررسیها را برنامهریزی کنید، با تأکید بر سیستمهای هیدرولیکی، راهنماها و مولفههای الکتریکی.
5. اندیشههای نهایی درباره دستیابی به خم شدن بدون عیب
دستیابی به بهینهسازی خم شدن نیازمند ترکیبی از دانش فنی و اجراي دقیق است. با سرمایهگذاری در تجهیزات مناسب، حفظ استانداردهای صریح و مواجه شدن فعال با مشکلات، سازندگان میتوانند دقت و کارایی بینظیری را به دست آورند. برای مشاوره شخصی یا حل مشکلات پیشرفته، با JUGAO CNC MACHINE همکاری کنید تا عملیات شما همواره در جلوهای نوین باشد.
امروز بهینه کنید—فردا برتر شوید.
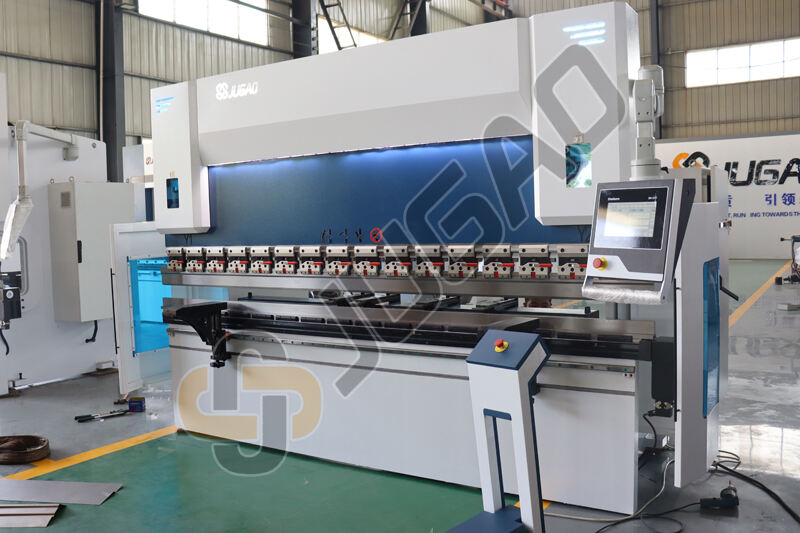
نکات کلیدی:
✔ سازگاری تجهیزات و ابزارها را اولویت بدهید.
✔ روالهای دقیق آمادهسازی مواد و کالیبراسیون را اجرا کنید.
✔ نگهداری پیشگیرانه را برای حفظ عملکرد اتخاذ کنید.
این نسخه اصلاحشده، روشنایی، جریان و عملیاتپذیری را در حال حفظ زمینه فنی نسخه اصلی، افزایش میدهد. اگر نیاز به تکمیلهای بیشتری دارید، با شرکت JUGAO CNC MACHINE تماس بگیرید!