Der Kernwert von Pressbremsen in der Herstellung von Fahrstuhl- und Hebezeug-Ausrüstung
Inhalt
1. Präzisionsformung: Der Kernprozess für den Aufbau sicherer Grundlagen
2. Technische Konformität: Vollständige Sicherheit von der Konzeption bis zur Produktion
3. Effiziente Produktion: Strategien zur Optimierung von Geräteparametern
4. Langfristige Wartung: Kritische Maßnahmen für die Betriebsstabilität
5. Branchenkenntnisse: Tiefe Analyse hochfrequenter Fragen
6. Technologische Fortschritte: Innovative Wege zum intelligenten Fertigen
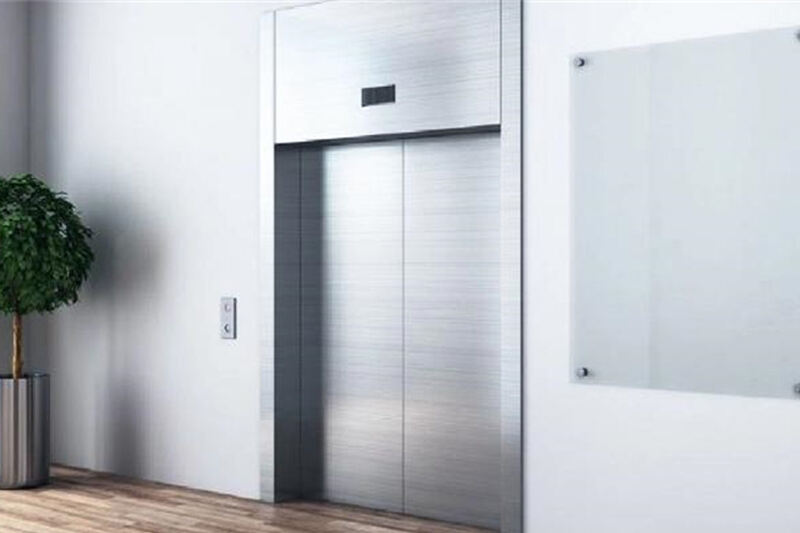
1. Präzisionsformung: Der Kernprozess für den Aufbau sicherer Grundlagen
Die Funktionsfähigkeit kritischer Komponenten wie Fahrstuhlkabinen und Krantragwerke basiert auf der präzisen Umformung von Metallteilen. Pressbremsen ermöglichen mit ihrem hochtonnigen Druck und CNC-Genauigkeit die Verarbeitung hochfestiger Legierungen (z. B. verschleißfestes Stahl, luftfahrttaugliches Aluminium) in komplexe Geometrien, wie die gekrümmten Querschnitte von Fahrstuhlführungsleisten oder Verstärkungsrippen für Kranausleger. Durch mehrachsige Formkonfigurationen erreichen diese Maschinen scharfe Winkelbiegungen mit Radien von bis zu 2 mm, wodurch kompakte Raumforderungen erfüllt werden, während gleichzeitig sichergestellt wird, dass die Materialgitterstruktur unbeschädigt bleibt, um Spannungskonzentrationen und potenzielle Brüche zu vermeiden.
In individuellen Szenarien können Pressbremsen drehbare Rohrbiegemodule oder segmentierte Formen integrieren, um Herausforderungen bei der Fertigung unregelmäßiger Komponenten wie Lifttürkoppelmechanismen zu bewältigen. Zum Beispiel benötigen Lifttürpanele fortschreitendes Biegen, um kontinuierliche Wellenstrukturen zur Verbesserung der Verformungsresistenz zu erstellen, während Kran-Seilrolle-Aufhängungen Schritt-für-Schritt-Biegetechniken erfordern, um die Lastverteilung auszubalancieren.
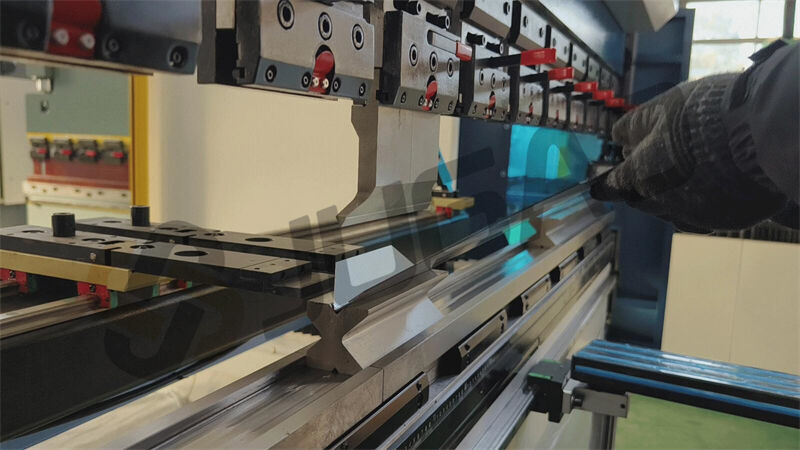
2. Technische Konformität: Vollständige Sicherheit von der Konzeption bis zur Produktion
Globale Sicherheitsstandards (z. B. EN 81, ISO 4306) legen strenge Toleranzeinschränkungen für tragfähige Komponenten fest. Zum Beispiel müssen Winkelabweichungen bei Fahrstuhlführungsprofilen innerhalb von ±0,3° gehalten werden. CNC-Pressbremsen verwenden Laser-Dynamik-Monitoringsysteme zur Echtzeit-Korrektur von Bearbeitungsparametern, kombiniert mit automatischer Rücklängskompensation, um manuelle Betriebsfehler zu eliminieren. Darüber hinaus ermöglichen die in den Maschinen integrierten Prozessdatenbanken die Einsatzaufnahme vordefinierter Programme durch einen Klick, um eine konsistente mechanische Leistung bei serienmäßig hergestellten Teilen gemäß den Designspezifikationen sicherzustellen.
Zur Risikominderung Vorhersagealgorithmen der KI, die in Pressbremsen eingebettet sind, Materialrücklauf und rammtiefe automatisch. Zum Beispiel wird beim Verarbeiten von Kranausgleichsgewichtsblöcken aus AR500-Stahl das System die Biegekurven dynamisch an Materialhärteeigenschaften anpassen, um Verschiebungen bei der Zusammenstellung aufgrund von Rücklauf zu verhindern.
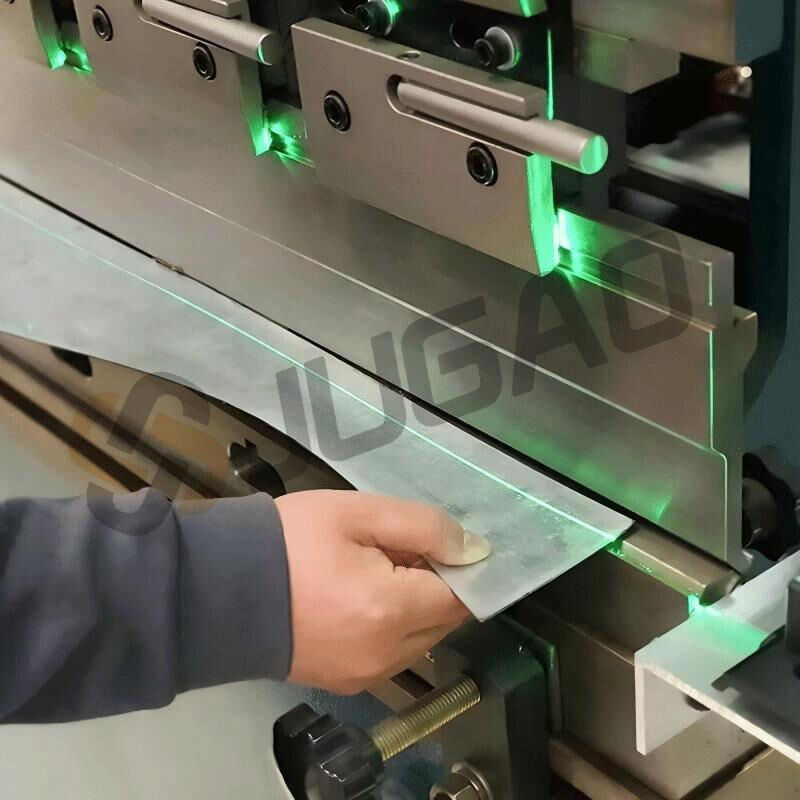
3. Effiziente Produktion: Strategien zur Optimierung von Geräteparametern
**Schlüsselschritt 1: Präzise Formenauswahl**
Wählen Sie Formen basierend auf Materialeigenschaften und Bearbeitungszielen aus. Spiegelglatte V-Formen (Öffnungsgröße = 8×Materialdicke) werden für Edelstahl-Liftwände empfohlen, um Oberflächenkratzer zu minimieren, während Tiefprofil-Formen (Öffnung ≥30mm) in Kombination mit fortschreitenden Druckmodi ideal für dicke Kranaufhängungskomponenten sind, um eine Formüberlastung zu verhindern.
**Schritt 2: Intelligente Parameterkalibrierung**
Erreichen Sie eine Unter-Millimeter-Positionierung der Rücklaufrichtung durch CNC-Systeme, validiert durch Lasainterferometer. Für Mikrotoleranze-Komponenten wie Lifttürrahmen sorgen geschlossene Regelkreise dafür, dass die Rücklaufrichtungsverschiebung ≤0,05mm bleibt.
**Schritt 3: Vorproduktionssimulation**
Führen Sie Probefalzungen mit Ausschussmaterialien durch, bevor Massenfertigung beginnt. Zum Beispiel erfordern Kranhaken Rissneigungstests bei 90°-Falzungen während des Prototypenbaus, wobei Anpassungen der Verweildauer (empfohlen 3-5 Sekunden) vorgenommen werden, um verborgene Mängel zu eliminieren.
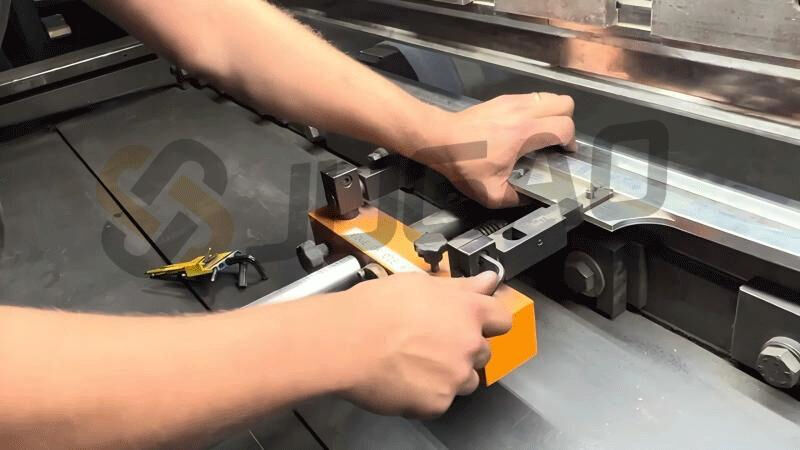
4. Langfristige Wartung: Kritische Maßnahmen für die Betriebsstabilität
- **Tägliche Inspektionen**: Überwachen Sie die Viskosität und Temperaturschwankungen des Hydrauliköls (idealer Bereich: 40-60°C), ersetzen Sie Filter rechtzeitig und überprüfen Sie die Stabilität des Servomotor-Encoder-Signals, um Unterbrechungen des CNC-Programms zu verhindern.
- **Monatliche Protokolle**: Verwenden Sie magnetische Partikeluntersuchung, um Oberflächenmikrorisse an Formen zu erkennen, und prüfen Sie die Härte von Hochfrequenzstanzern erneut (≥58 HRC).
- **Fehlerprognose**: Tritt während der kontinuierlichen Betriebszeit ein Winkeldrift auf, priorisieren Sie die Überprüfung der Parallelität der Maschinenschienen (Toleranz ±0,01mm/m) und die Synchronisationsgenauigkeit der Hydraulikzylinder.
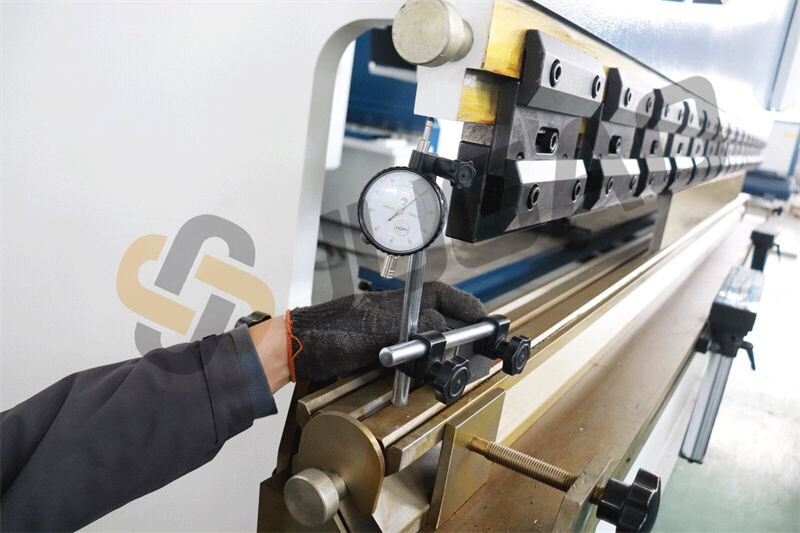
5. Branchenkenntnisse: Tiefe Analyse hochfrequenter Fragen
**Q1: Empfohlene Pressbremsemuster für den Verarbeitung von Fahrstuhlführungsprofilen?**
Wir empfehlen CNC-Elektro-Hydraulikpressbremsen mit Doppelservuantrieb (z. B. JUGAO 8+1-Achsen-CNC-Hydraulikpressbremse mit DA-66T-Controller), die eine Schleifenregelgenauigkeit von bis zu ±0,1° und eine Multivorgangskoppelung bieten, um Positionierungsfehler zu minimieren.
**Q2: Wie kann man Kantenrissbildung bei der Biegebearbeitung von Edelstahl verhindern?**
Verwenden Sie uferierte Materialien (Härte ≤HB200) mit einer Biege radius ≥4T (T = Materialdicke). Wenden Sie PTFE-basierte Schmierstoffe an, um die Reibung zwischen Formen und Blättern zu reduzieren.
**Q3: Wie setzt man Kalibrierintervalle für das Equipment?**
Führen Sie eine vollständige Kalibrierung aller Parameter alle 200 Betriebsstunden unter normalen Bedingungen durch. Kalibrieren Sie Druckkurven neu, wenn Sie das Material wechseln (z. B. von 6061 Aluminium zu S355JR Stahl).
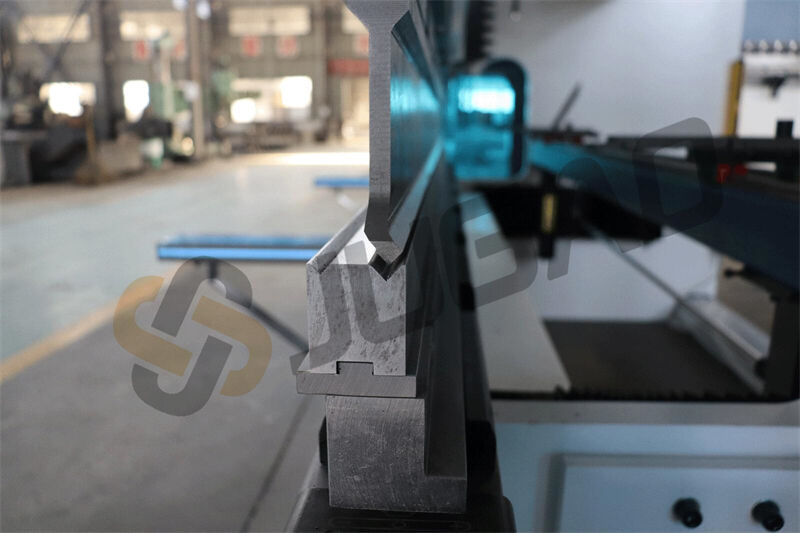
6. Technologische Fortschritte: Innovative Wege zum intelligenten Fertigen
Durch die Integration von Industry 4.0-Technologien ermöglichen neueste Pressbremsen ferngestützte Diagnose und Prozessoptimierung über IoT-Plattformen. Zum Beispiel warnen big-data-getriebene Systeme zur Vorhersage der Formlebensdauer 30 Tage im Voraus vor Ersatznotwendigkeiten, während AR-unterstützte Schnittstellen Echtzeitbiegeparameter projizieren, um menschliche Fehler zu minimieren.
Schlussfolgerung
Als das "Prozessherz" der Fahrstuhl- und Kranherstellung beeinflussen Pressbremsen direkt die Sicherheits- und Effizienzgrenzen der Industrie. Durch die Umsetzung verfeinerter Parametermanagement, proaktiver Wartungsstrategien und intelligenter Upgrades können Hersteller unter strengen Industriestandards Durchbrüche in Qualität und Produktivität erzielen. Für maßgeschneiderte Lösungen bietet das Ingenieurteam von JUGAO eine umfassende Unterstützung von der Ausrüstungsauswahl bis zur Prozessoptimierung.