CNC Press Brake Laser Angle Measurement Device
Jan.25.2024
CNC Press Brake Laser Angle Measurement Device
From Germany
The market share of CNC press brakes is increasing, and the requirements for high-end NC press brake configurations are also becoming higher. Among them, the demand for laser angle measurement devices is gradually being accepted. JUGAO brings a in-depth analysis of laser angle measurement devices.
No 1. Angle detection overview Description of Laser Check
The laser angle detection compensation device measures the bending angle by scanning the laser projected onto the surface of the sheet using a CMOS/CCD camera. The angle between the laser and the observation axis of the camera determines the measurement distance, and these data are used to calculate the angle between the sensor and the sheet. The bending angle is also calculated using a second sensor in the opposite direction.
Real-time measurement is achieved through the use of the Laser Check sensor and a high-speed GigE camera, with a refresh rate of up to 100Hz. The compensation process starts during bending and continues in real-time until the bending force drops to a preset value. For equipment with a tonnage of 250T or more, strain measurement devices need to be installed on the C-shaped openings on both sides of the bending machine frame. This is because the deformation "tension" of the side walls under the reaction force during the bending process can cause "errors" in the movement of the grating ruler. Installing strain measurement devices allows for the measurement of the deformation of the frame openings on both sides. The deformation is fed back to the CNC through the strain measurement devices and amplifiers, and real-time communication with the CNC system is used to calculate the springback angle and perform real-time compensation.
High precision measurement of bending angle and sheet metal springback coefficient
Non-contact operation
Not affected by material thickness
Not affected by mold shape, no need for any mold adjustment
Can set different measurement positions
The movable sensor can perform multi-point compensation measurement and correction, such as Y1, Y2, and deflection compensation correction.
Can be used in parallel with 2 sensors
Calculate the sheet metal springback characteristics using a strain gauge
Connect to Delem system via Ethernet (Modbus)
Flexible and convenient application, precision calibration completed before shipping.
Apologies for the confusion earlier. Here's a revised translation:
The laser angle detection compensation device on the bending machine can detect the characteristics of different materials during the downward pressing process of the slide block. It effectively solves angle issues caused by variations in plate thickness, inconsistent springback, surface oxidation layer, and changes in rolling patterns. Throughout the bending process, real-time communication is maintained with the CNC system to calculate and control the precise position of the slide block's bottom dead center. The CNC controls the Y1, Y2, and deflection compensation systems to compensate for angle accuracy, ensuring that the desired perfect result is achieved in the first bending operation!
No 2. Working Principle
No 3. Accuracy The accuracy error of the sensor itself is within ±0.2°, and the actual angle accuracy in practical applications is generally within ±0.3°.
However, the actual bending accuracy is influenced by factors such as the CNC system, machine tool precision, die, sheet material, bending process, length of the bent workpiece for detection, environment, and temperature, which can lead to variations in accuracy. In order to improve the bending accuracy, the sensor needs to be calibrated after installation to eliminate installation errors.
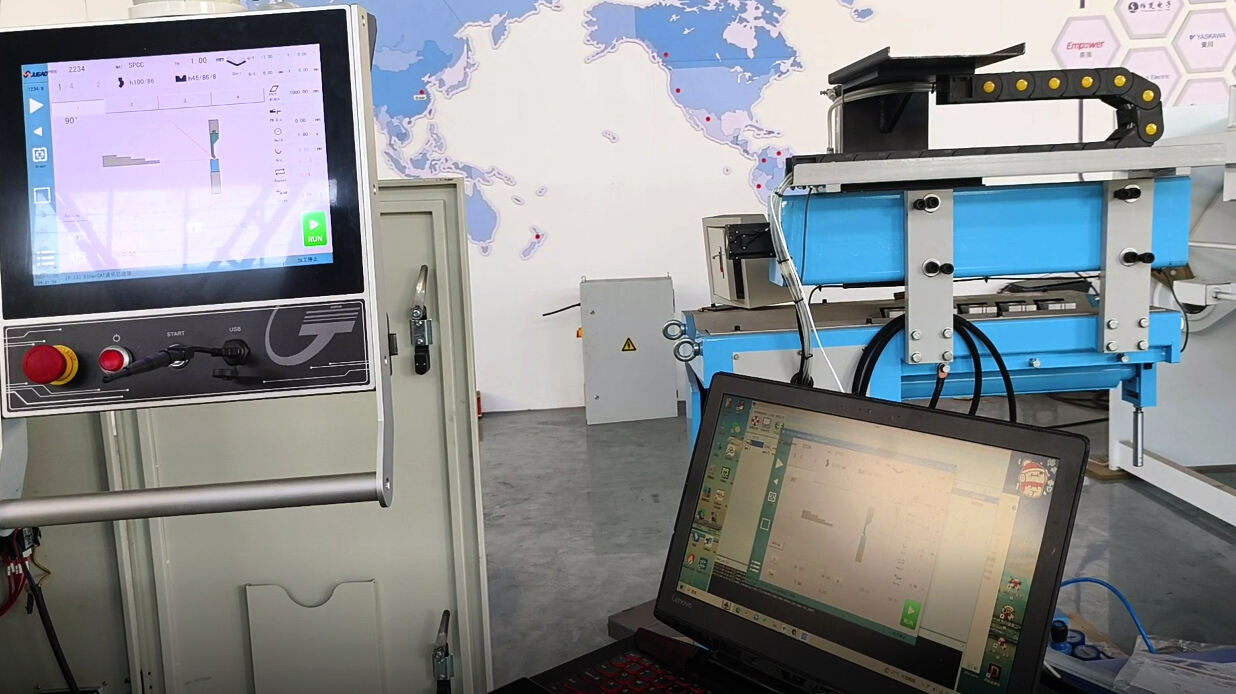
No 4. Advantages:
High precision measurement of bending angle and sheet metal springback coefficient
Non-contact operation
Not affected by material thickness
Not affected by mold shape, no need for any mold adjustment
Can set different measurement positions
The movable sensor can perform multi-point compensation
measurement and correction, such as Y1, Y2, and deflection compensation
correction.
Can be used in parallel with 2 sensors
Calculate the sheet metal springback characteristics using a strain gauge
Connect to Delem system via Ethernet (Modbus)
Flexible and convenient application, precision calibration completed before shipping.
No 5. Application:
Angle detection: can be set to detect only the first piece or initial N pieces; can also be set to follow the first piece detection mode after the first piece, saving cycle time. During processing of the same batch of workpieces, random sampling can be performed as needed.
For workpieces with complex bending steps or small bending surfaces, the first bend can be detected to ensure satisfactory results. The remaining bending steps can use the "learning" mode of the first bend for detection, saving bending cycle time.
Can move freely along the length direction of the sheet, with a maximum speed of 1000/s.
Can set to detect the midpoint or endpoints of the workpiece, or set to detect three points on the left, middle, and right within the full length range.
Depending on the different bending workpieces, a longitudinal expansion axis can be added. When using different lower dies for bending different types of workpieces, the laser angle detection device can automatically move and adjust the angle detection area to adapt to the different lower dies required for different workpieces. Generally, it can cover the range of V6-V180 lower dies.
The sensor has an accuracy of within ±0.2°, and the angle accuracy is generally within ±0.3°.
Workpiece angles ranging from 30° to 180° can be detected.
The minimum edge length that can be irradiated and detected must be ensured to be above 20mm (refer to the diagram).
The market share of CNC press brakes is increasing, and the requirements for high-end NC press brake configurations are also becoming higher. Among them, the demand for laser angle measurement devices is gradually being accepted. JUGAO brings a in-depth analysis of laser angle measurement devices.
Not only is angle detection sensor important, but it is also crucial to establish a seamless connection with the bending machine to form a complete angle compensation correction system. This system includes an angle detection device, control system connection ports, customized software, strain measurement devices, and a drive shaft for sensor movement. With these components, a closed-loop system can be formed for real-time angle measurement and compensation.
Laser Check
No 6. The laser angle measurement device is compatible with CNC systems such as DELEM's DA66T and DA69T. In addition, it requires the addition of a DELEM DM-101RS module and the DELEM Software development code OP-W-SENSOR. The mechanical part needs to add related devices such as movable axes.